Brewery wanted a socially and environmentally responsible system for this food and beverage application.
Blue-White Industries
02/12/2019
Stone Brewing Company, located in Escondido, California, is a strong advocate for environmental responsibility. It has grown from a small microbrewery to one of the largest craft breweries in the United States. Its goal has been to brew quality beers while maintaining a commitment to sustainability, business ethics and the art of brewing. The grounds at Stone Brewing have won several awards for environmentally responsible landscape architecture. The facility is built within a flood retention basin and draws on reclaimed materials, including second-hand plants.
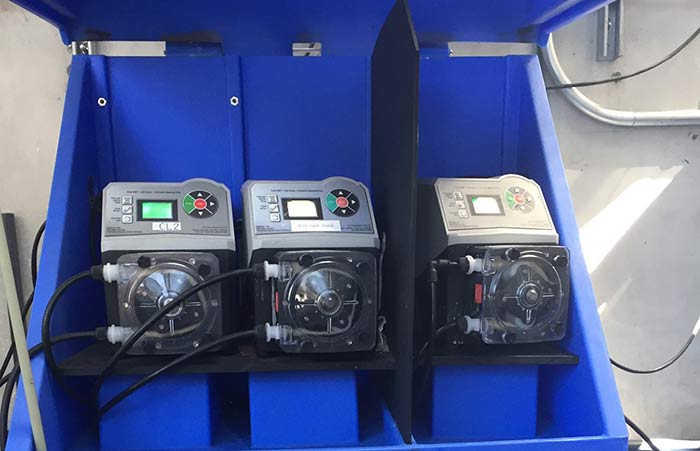
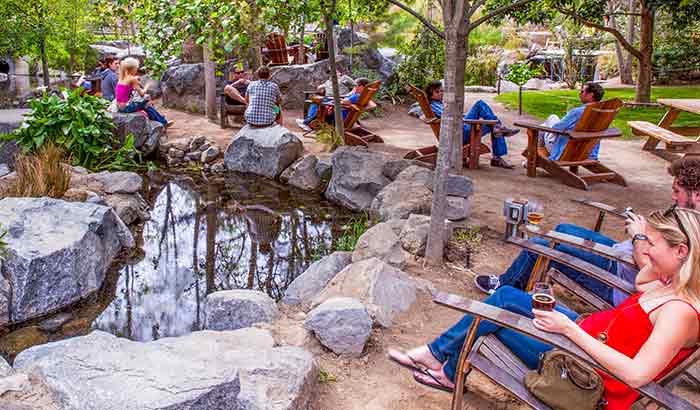
Solving the Wastewater Dilemma
Stone Brewing is regulated by the county and state and is required to meet wastewater discharge protocols. The brewery and the packaging hall generate approximately 100,000 gallons of wastewater per day. To achieve the standards required for safe disposal of wastewater, Stone Brewing needed to find reliable, operator- friendly metering pumps that would deliver accurate amounts of chemical into the treatment system.The Right Pump
Stone Brewing installed four peristaltic chemical metering pumps to assist with the purification of the wastewater. Two of the pumps inject a solution of 12.5 percent sodium hypochlorite for use in the membrane bioreactor (MBR) filter backwashes. MBR processes can produce high-quality effluent so that it can be discharged into coastal waterways or reclaimed for urban irrigation. One of the pumps injects 93 percent sulfuric acid prior to reverse osmosis. This is also used in the process of removing effluent materials from the water molecules. The final pump injects 12 to 14 percent sodium hydroxide to bring the reclaimed water to a pH of 8 so it does not corrode the pipes.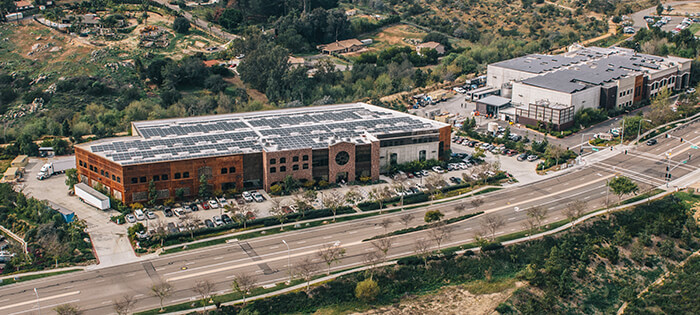