In past “Pumping Prescriptions” columns this year, I have discussed the procedure of piping size selection when given the process flow requirement and how this affects the pump’s power consumption. In this column, two computer calculation tools will be detailed. The tools are the Energy Consumption Calculator and the Pump Performance Estimator. Both can be found at pump-magazine.com/pump_magazine/pump_magazine.htm. These tools provide a quick and basic evaluation of piping’s effect on pump energy and the effect’s associated cost. As always, the best way to understand a concept is with an example. In our example, a process must move water at a rate of 8,000 gallons per minute. The water must be transported 5 miles across flat terrain with no significant elevation. In this type of application, most of the hydraulic losses result from pipe friction. The process flow is a non-stop 24 hours per day and seven days per week.
Energy Consumption Calculator
The Energy Consumption Calculator should be used first. This tool will estimate the friction losses associated with pumping the water through a selected pipe diameter (18 inches) and length (5 miles or 26,250 feet). A straight run of pipe is assumed with no additional losses for bends, turns or other restrictions along the way. More detailed programs are available to handle more complex piping. However, for this type of calculation, a simplified straight piping run will suffice. Clean (or relatively clean) water is assumed to flow through reasonably new pipe in this calculation. For old, rusty or partially clogged piping, additional adjustments must be made. For example, entering a smaller pipe diameter will simulate a partial blockage. Table 1 shows the first iteration of the Energy Consumption Calculator’s results.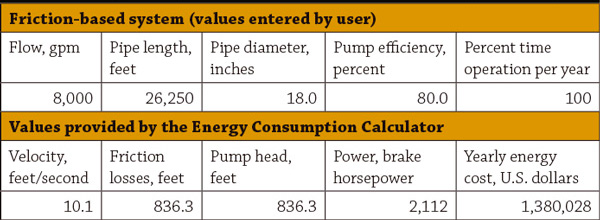
Pump Performance Estimator
Once the pump head (836.3 feet) has been determined, the Pump Performance Estimator can be used to define a more accurate pump efficiency value. The pump efficiency adjustment is calculated by the Pump Performance Estimator (see Table 2). Notice that the more accurate pump efficiency is 83.9 percent, which reduces the required power to 2,013 horsepower.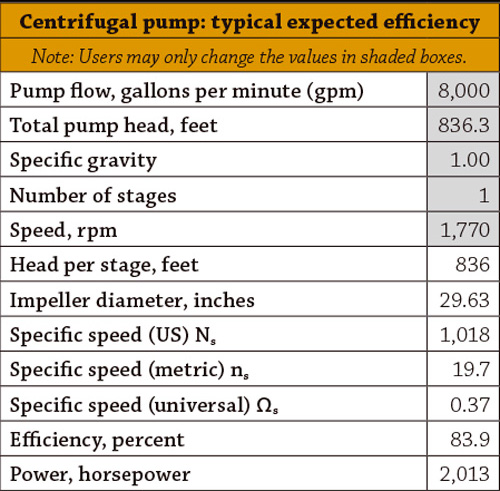
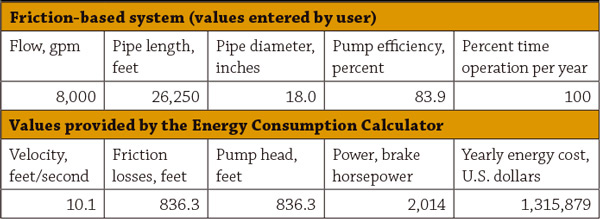
Alternate Pipe Diameter
What happens if the pipe diameter is larger? We will enter the same flow, distance and efficiency information but change the pipe diameter to 20 inches (see Table 4).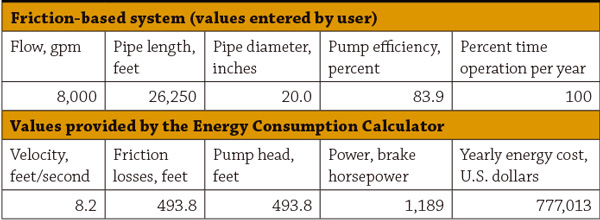