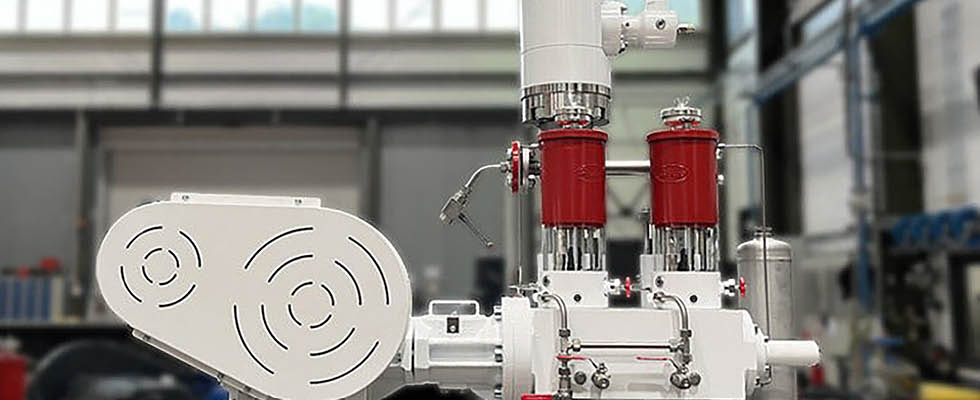
With the maturation of reciprocating pumps, the piston actuated round-diaphragm pump was the standard in pumping higher pressure and flows than other positive displacement pumps. The need for an equally efficient but more laminar design with a more hermetic ability was required, as contamination throughout the diaphragm—and even the associated air compressors and air/fluid combination valves—became known with the old style round-diaphragm design.
In hose-diaphragm pumping, each double hose that could rupture would also have a secondary hose. If both hoses rupture, the fluid being pumped would only contaminate one cylinder and not be pumped under pressure throughout the pump. Therefore, the next generation of reciprocating pumping of heavy, solids-ladened fluids and slurries would be conveyed by means of a double-walled hose that is both hermetic and isolated. During fluid disruption events, a hose-diaphragm pump, bolstered by a complement of air-regulated pulsation dampeners, flow, ball, double ball and various other mechanically actuated check valves and valve monitoring equipment, would be a better option than that of a round-diaphragm pump.
The hose-diaphragm pump can achieve higher flows and pressures, like the old round-style diaphragm pumps. It can reach peristalsis like a regular hose pump while being fixed and double walled as one hose inside the other. The same elastomer rules for chemical compatibility and operational physics would still apply. The range of applications for the hose-diaphragm pump would be mostly the same as any larger round-diaphragm pump, such as filter press, oil and gas applications, chemical, petrochemical, wastewater, etc. The design of hose-diaphragm pumps is more likened to a human vein being elastically distorted or slightly squeezed, rather than a plunger pushing back and forth upon the fluid and a sloshing taking place in a valve housing, only to move to the round-diaphragm housing to be pumped. The hose diaphragm produces a hermetic, more linear path for the fluid to travel, thus achieving almost perfect peristalsis pumping.
As stated, the double-walled hose provides hermetic, leak-proof pumping, with the second outer hose acting as a safety for the first. These can also be manufactured in several elastomers to match the fluid for chemical compatibility. They usually have a life span of about 10,000 hours. Double ball valves are also common with this type of pump, which most round-diaphragm pump manufacturers do not offer. No special valve extraction or maintenance tools are generally required. These pumps can have a swing-away valve housing that allows the ability to change out a valve in under 30 minutes, with no special tools. The monobloc style drive and crank save space, as they have a more compact and less horizontal profile with motors that can be placed vertically, as opposed to most round-diaphragm pump designs. Since the fluid only comes in contact with the inside of the hose, special construction materials for the housing are not usually necessary unless the pump is in a vaporous environment. This saves money and adds to the life of the pump, since the chances of a chemical attack do not exist. These types of pumps have the ability to reverse the direction of the flow from inlet at the bottom, to inlet at the top to allow thick and abnormally heavy viscous slurries to flow downward and pass through better.
The piston actuated hose-diaphragm pump can help pump difficult media at high pressures and flows, with high efficiency, safety and maintenance friendliness. The durability, life span and modularity are helpful in difficult applications.