The manufacture, transfer, handling and use of dangerous chemicals such as acids, caustics and solvents—which can be corrosive, toxic and hazardous to life and the environment—can pose significant challenges for steel pumps. Specific types of steel pumps may cover only a narrow chemical-resistance band, which, in some cases, can limit the applications they can handle—particularly those involving dangerous chemicals. One alternative for successful chemical-manufacturing and handling operations is the plastic pump. Within this subset, end users can choose from many types of pump technologies: for example, lobe, gear, vane, centrifugal and progressive cavity. Some of these technologies, however, can have potential shortcomings that may make them impractical for chemical-related applications. Some of these challenges include the inability to run dry or self-prime, use of leak-prone mechanical seals, shear-producing operation, inability to deadhead, limited viscosity ranges and elevated maintenance costs.
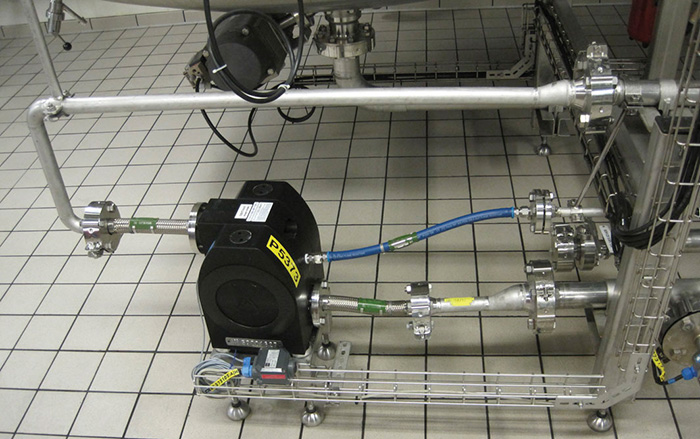
Benefits of Solid-Body Pumps
While plastic AODD pumps can be ideal for operations that manufacture or transfer dangerous chemicals, one question remains: Should the pump be constructed of injection-molded plastic or from a solid block of plastic? A reliable and proven choice for these applications is the plastic solid-body AODD pump, specifically one that is machined from a solid block of polyethylene (PE) or polytetrafluoroethylene (PTFE). The materials are also available in PE-conductive and PTFE-conductive formulations for use in potentially explosive atmospheres. End users seem to prefer solid-body plastic AODD pumps over their injection-molded cousins. One reason is that solid-body pumps are inherently thick-walled, providing stability during the pumping process. Injection-molded pumps can have small cavities or crevices in the body where liquids can accumulate and leak paths can form. Because injection-molded pumps are lightweight, any motion during the pumping process is transferred to surrounding system components and piping, which can lead to equipment damage.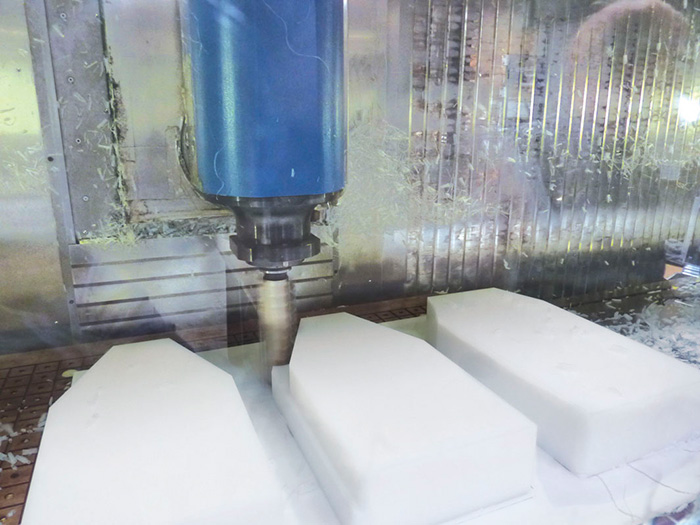
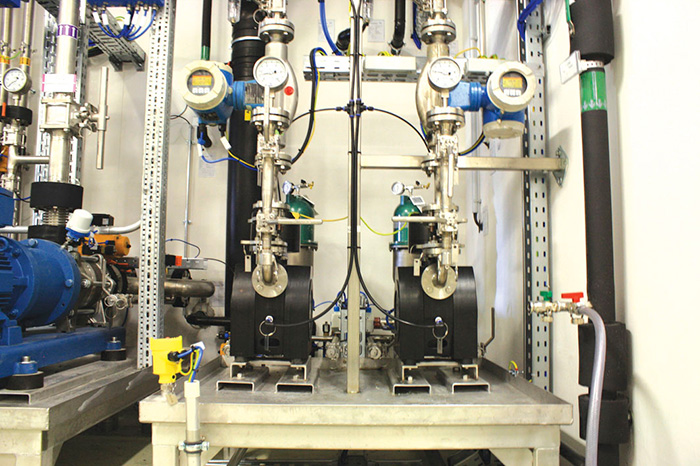