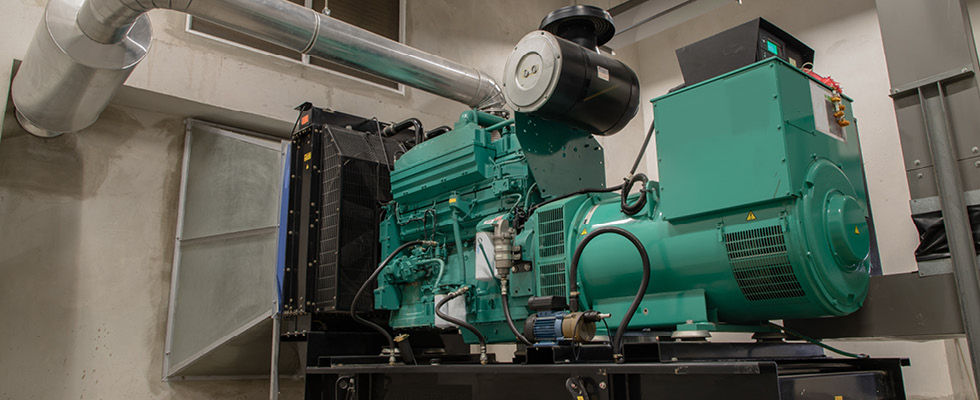
Municipal facilities depend on a stable, uninterrupted power supply to operate reliably and effectively. If that power supply is interrupted, emergency standby generators come online to power facilities; however, improperly sized generators could fail to operate reliably, leading to potential interruption of critical public services. This article summarizes the basics of sizing an emergency standby generator, outlines options for starting and controlling motors and compares the impacts on generator stability of two types of variable frequency drives (VFDs). It will also explain the benefits of using active front end (AFE) VFDs when designing systems that require generators.
Sizing Generators
To size a generator, consider these factors:
- Maximum required load
- Typical load variation
- Average generator load factor
- Running hours per year
Typically, standby generators for municipalities provide emergency power at full load for the full duration of an outage. The average load factor of a standby-rated generator should be no more than 70% full load rating, applied to varying loads and run for up to 200 hours/year. The maximum load required is determined by performing a load analysis—summing electrical voltage and current kilovolt-amperes (kVA) required to start motors and keep them running, plus additional draw (e.g., lighting/heating, ventilation and air conditioning [HVAC]). Two components tied to the load analysis are starting (peak) kVA and continuous (running) kVA.
Continuous kVA is the sum of all electrical loads while running at full load conditions.
Peak kVA is the largest, short-term draw that occurs at start, dictated by the device used to control the facility’s motors. The larger the kVA, the larger the size and cost of the generator.
To reduce generator size but provide enough power, select a motor starting device that reduces peak kVA. Three common starting devices that impact peak kVA requirements are:
Direct on-line (DOL)/across-the-line starting, or full-voltage non-reversing starter (FVNR), is a method that instantaneously applies full voltage to motor windings. When applied, a short-duration spike or inrush of current occurs, 6 to 8 times the continuous or running current. Because the motor comes to full speed quickly, it can cause mechanical damage or hydraulic surges in the system. Its peak kVA is the largest value of all starting methods.
Soft start, or reduced voltage solid state (RVSS) starting, is a method of reducing inrush current while bringing the motor to full speed. Voltage is applied to the motor windings and controlled by either stepping or softly increasing the voltage to maximum. The inrush current can be reduced to 3.5 to 4 times the running current. Peak kVA is less than the DOL method but still more than desirable.
VFDs, or variable speed drives (VSDs), start and control a motor without high inrush current. They draw only the current needed to operate the motor at required speed and load, eliminating peak kVA so running kVA becomes the only value needed.
Using VFDs reduces the generator size to continuous required kVA; however, VFDs can introduce distortion to the power supply that must be minimized to <10% total harmonic distortion (THD), which is mandated by standards such as IEEE519. Excessive distortion may result in heating of the generator alternator and can cause instability or trips.
Understanding Common VFD Technology & How Each Type Impacts THD
VFDs vary the voltage and frequency delivered to the motor to control starting, stopping and speed. Importantly, they gradually increase speed during starting and then control speed during operation to accurately control pressure and flow.
There are three common VFD types, and all impact THD differently:
1. Passive input or diode bridge type VFD: This VFD uses a semiconductor device called a diode rectifier (a passive power conversion device that only allows one-way power flow) to convert alternating current (AC) power to direct current (DC) power. This rectification process creates voltage waveform distortion in large amounts, well above the mandated 10% THD. A common solution to reduce this uses external harmonic filtering in series with the VFD to minimize negative impacts. This typically results in lowering the THD to around 10% to 12% depending on size/cost.
2. 18-pulse VFD: This is another passive input VFD that uses a special power conversion transformer and two additional rectifiers to power the VFD. It creates less THD than the harmonic filter design, typically between 5% and 10% THD. The technology relies on harmonic cancellation, which decreases as line-to-line input voltage imbalance increases. The addition of either this technology or a harmonic filter is often recommended to reduce THD to acceptable levels when using a generator. However, there are often additional cost, size and heat loss needs.
3. Active input/active front-end (AFE) type VFDs: This VFD uses input transistors that rapidly switch the incoming AC voltage on and off to actively convert the AC power to DC power. This input power conversion process does not distort the AC voltage and therefore does not create a large THD. These transistors do create high frequency harmonics, but they are typically absorbed by a high frequency filter mounted inside the VFD. AFE VFDs typically create no more than 3% to
4% THD without costly additional external filters.
VFD Selection for Stable Voltage & Current
Either type of VFD, passive input or AFE, will keep the generator from tripping, provided the VFD solution design brings THD to less than 10% or if the generator is oversized enough to absorb alternator heating caused by higher THD.
A passive input unfiltered diode bridge VFD without external harmonic filtering produces a THD of 35% to 45% and typically requires generator up-sizing to twice the running kilowatts (kW) since the distortion must be absorbed by an oversized alternator. This often leads to a larger engine, making the generator larger and more expensive. Unfiltered VFD units are not as costly, but this is negatively offset by the larger generator.
However, a passive input VFD with an 18-pulse filter (5%-10% THD) or an AFE VFD (4% THD) moves the generator upsizing factor to just 1.4 times the running kW. Low THD VFDs allow the user to “right-size” the generator closer to the site’s running load. They may be more costly than passive VFDs, as there is a major cost offset in generator upsizing when using these designs.
The generator size almost doubles between the different types of VFDs. Sizing the generator using an unfiltered passive input VFD requires a 350-kW generator. When changing to a low-harmonic VFD, the generator size drops to 200 kW.
The larger generator allows for an oversized alternator to absorb additional heat created by the large amount of THD. After factoring in the additional cost of lower-harmonic VFDs, like 18-pulse and AFE, the total equipment cost (VFDs and smaller generator) is 8% to 10% less than the alternative. The cost comparison shows a lower total equipment cost by spending more on a low-harmonic AFE VFD solution to achieve low THD, resulting in a smaller generator.
Benefits of Active Front-End VFDs Extend Beyond Low Harmonic Distortion
Along with reduced generator size and cost, AFE drives outperform passive input VFDs, providing high power factor and output voltage boost to the motor without sending energy back into the generator.
AFE VFDs control and adjust the power factor, an indicator of energy efficiency in AC power circuits, to maximize the efficiency of the load on the generator. This also helps size the generator to the actual load.
Output voltage boost to the motor is a benefit that AFE VFDs provide to extend motor life by reacting to low input voltage and in turn boosting output voltage to the motor so there is no overcurrent or excessive heating.
AFE VFDs typically regenerate (send energy back) to the source. Regenerating power is not welcomed since generators are not designed for prolonged absorption of power. Too much regeneration causes the generator to become unstable and protect itself by tripping offline.
Correctly sizing an emergency generator with an AFE will help reduce costs and provide reliable power to keep supply treatment processes running uninterrupted. AFE drives provide benefits to municipal operations in the form of lower operating costs, extended equipment life and reduced equipment downtime.