Although power failures at pumping stations are rare, industry experts responsible for the safety and efficiency at these complex installations are not taking chances. They spend countless hours and costly resources to prevent any power outage, distortion or noise from disturbing the operation of the strategic equipment and processes at various installations throughout the world. Studies by the U.S. Department of Interior’s National Petroleum Council have concluded that power failures would have significant impact on electric-powered pumping stations because most of them are entirely dependent on purchased electric power. “Power-dependent pipelines would experience a reduced rate of throughput in many of the pump stations along the system,” according to one report. Thanks to today’s advancements in technology and digitally controlled instrumentation in all phases of the industry, the chances of power outages or even total shutdowns have been substantially reduced. The primary reason is state-of-the-art uninterruptible power supply (UPS) systems. Because many pumping stations are located in remote and rugged environments, the UPS systems may not be in an enclosed facility or near other operations. These systems are often installed in rooms designed to house electronics and other switchgear. These rooms—the battery room, for example—may be climate-controlled and located on site close to some type of process control, lighting and/or safety system in a production facility. Also, the installation may be exposed to wide temperature swings, humidity and even corrosive environments, resulting in more frequent failures that can be extremely costly. Today’s pumping station installations are virtual computer centers, complete with large-scale integration (LSI) and very large-scale integration (VLSI) technologies, resulting in chips containing thousands of semiconductors and their interconnections. The power rating of these logic and memory devices has decreased while response time has improved tremendously.
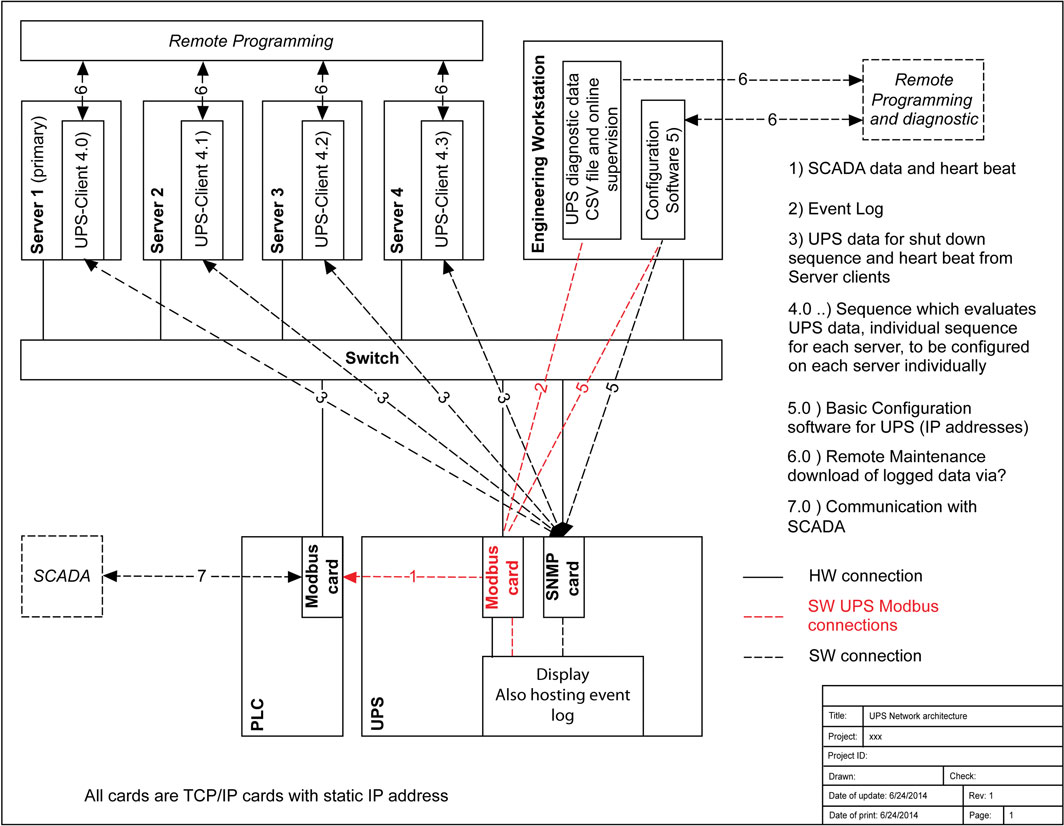
Why a UPS?
When a power outage or severe power quality deterioration occurs, pipelines and pumping systems must enter into safe network shutdown procedures. These protocols are controlled by various servers that monitor and control the system parameters; however, incidents take place when the systems do not operate correctly, even when the predetermined power-down protocols were followed. These malfunctions occur when the UPS batteries are drained of power, triggering a power loss in the backup batteries that causes failures in many, if not all, of the control systems deployed at a pumping station or pipeline control mechanism. These malfunctions are unacceptable since improper sequencing of pump valve shutdown protocols can lead to huge problems, including auto-shutdown valves failing to activate and, in the worst case, ruptured lines. The latest UPS technology guards against these malfunctions, ensuring that the servers send the proper shutdown communications prior to and after a power loss. The newest software built into UPS systems more accurately monitors remaining battery life and controls server shutdown protocols based on real information of true battery life. It can provide the information needed to prevent system errors that cause the servers to lose power before commencing a shutdown of the pump systems.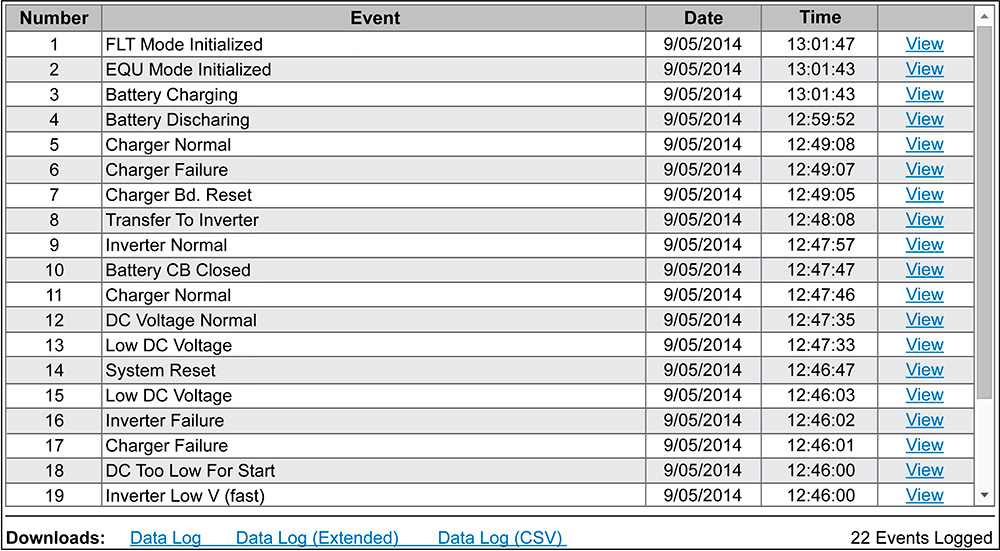