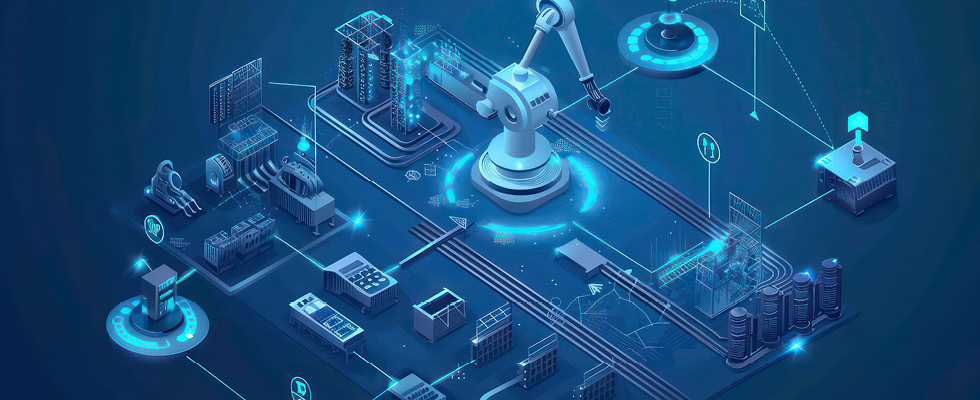
Unplanned and unscheduled downtime represents one of the costliest events at any industrial or manufacturing plant. A 2024 study on the cost, causes and consequences of unplanned downtime surveyed more than 100 manufacturers globally at the field service and IT decision-maker level in the United States, United Kingdom, France and Germany. The research also surveyed around 350 companies in other sectors globally across the medical, oil and gas, energy and utilities, telecoms, distribution, logistics and transport sectors, among others. The results showed that 82% of companies have experienced at least one unplanned downtime incident over the past three years; most have suffered two or more.1
Every Industry Is Affected
Unfortunately, no industry is immune to this situation. The following are a number of examples of the costs of unplanned downtime due to pump failures in a variety of markets. A 2016 study by Kimberlite, an oil and gas market research company, quantified the costs unplanned downtime have on the industry.
According to the study, the cost of downtime is not cheap. On average, offshore organizations experience $38 million annually in costs from unplanned downtime. Organizations with the worst measured performance saw financial impacts north of $88 million annually.2
One cause of unplanned downtime in this industry is when the seal fails on a pipeline booster pump, reducing the flow to refineries and resulting in leaking product. Leaking fluids can pose environmental and safety risks, especially if the pumped media is hazardous or flammable. Pump seal leaks can also cause damage to the pump’s internal components, such as bearings and shafts, leading to premature failure and expensive repairs.
The failure of a centrifugal pump from cavitation during batch production at a chemical or life sciences plant poses many challenges to ensuring the integrity of controlled environments and preventing contamination. If a pump used to empty a bioreactor at a critical time is malfunctioning, it may be a problem with the variable frequency drive, motor or pump—but in either case, the result is reduced yield for the batch due to extended reaction time.3 Any small amount of unplanned system downtime can result in a decline in product quality and brand reliability.
A mining company can also experience unplanned downtime when a slurry pump seizes after a bearing failure, resulting in halted operations and a potential for safety and environmental hazards. In the rigorous, demanding world of mining, slurry pumps are often run to breaking point before intervention. The punishing conditions in which mining machinery operates accelerate wear and tear that leads to frequent malfunctions, breakdowns and unexpected downtime. Research shows that, on average, these downtimes cost $180,000 per incident, and mining manufacturers are forced to allocate 35%-50% of their annual budgets to maintenance.4
Turning to the critical utility and power industry, if a boiler feed pump suffers impeller damage, output is reduced, causing brownouts, and contractual penalties may also be incurred for this downtime. One hour of downtime costs electric utilities $300,000. However, the consequences of downtime extend beyond monetary costs. Additional impacts of unplanned outages include not being able to deliver services to customers, lost production time on critical assets and an inability to service and support equipment.5
Technology Improves Overall Equipment Effectiveness
Plant personnel often use manual data collection to capture losses and generate efficiency metrics—or, if they have embarked on an overall equipment effectiveness (OEE) journey, they use line-level data collection.
However, this information is often grossly inaccurate. For example, a national bottling company’s reports indicated there were five stops during the week on a line when there were actually more than 75 stops a day, or about 375 stops a week. Additionally, the lack of real-time data meant plant personnel received information the next day on how well they performed the previous day, further impeding progress.
In manufacturing, minor stops refer to brief interruptions in production that are typically resolved within minutes. These pauses can result from various factors, including equipment malfunctions, material shortages, tool changes or even brief operator interventions. Since an average production line stops an astounding—and costly—20,000 times per year, there is a lot of room for improvement. These interruptions, typically lasting less than three minutes, may seem inconsequential at first glance. However, their cumulative impact on productivity and profitability can be staggering, as previously referenced.
Understanding Production Stops
Tracking minor stops provides visibility into their frequency, duration and root causes. This awareness allows organizations to identify patterns and implement targeted solutions to minimize interruptions. By collecting data on minor stops, organizations can analyze trends and make informed decisions regarding equipment maintenance, process improvements and resource allocation. Capturing data from machine assets provides immediate insights for both people and systems, enabling them to make better, faster decisions and drive automation.
Recently, researchers studied over 100 global manufacturing operations worldwide to benchmark performance and correlate over 20 manufacturing key performance indicators (KPIs). To determine a manufacturer’s competitive position, OEE was used as the top indicator of performance. Each manufacturer was ranked by OEE and all other KPIs were viewed in context of this order. Some of the key findings include:
- Best-in-class and average organizations exhibit an OEE more than two times over laggards.*
- Knowledge sets apart best-in-class performers over laggards. Only 0.5% of downtime reasons are unknown for best-in-class vs. 15.7% unknown downtime reasons exhibited by laggards, a factor of over 30 times.
- The poorest performing operations exhibit 6x more minor stops per year than the best operations.
*Best-in-class OEE ranks in the top 25%; average OEE ranks in the middle 50%; laggard OEE ranks in the bottom 25%.
Results from this study can offer the industry strategic and operational direction for organizations to improve their competitiveness. All organizations, no matter how high they rank, always have areas to improve. Companies ranking on the lower end of the scale can immediately determine where to start their improvement efforts.
Data Is Key to Increasing Efficiency
While accurate, real-time data is pivotal to operations, harnessing this data effectively requires advanced technology and analytical capabilities. Vast amounts of data are collected for industry reporting, predictive maintenance and safety enhancements, for example, but organizations may be challenged to effectively manage and analyze the data. While monitoring and alarms can improve system efficiency, they do not automate the labor-intensive reporting process or provide much-needed analytics that extract raw or summary values over a discrete time period.
Automated third-party reporting software, however, tracks all areas in a production facility. The finished reports are then distributed directly to preferred destinations, which streamlines the decision-making process and enhances operational efficiency. The ability to harness this data effectively can lead to smarter decision-making, improved processes and a competitive edge. Analyzing historical data allows operations management to identify patterns, trends and anomalies that may otherwise go unnoticed. Historical data analytics can help organizations transition from reactive to proactive planning and keep planning aligned with operations. As the data is collected, it is summarized as key metrics, and the final output is published into a formatted document accepted by regulatory agencies.
Integrating additional software accelerates digital transformation with advanced data collection for OEE and manufacturing execution systems (MES), enabling plant personnel to have valuable insights into the operations and helping them make better and more informed decisions. By deploying third-party advanced software, manufacturing plants can accelerate and drive OEE uplift, avoid problems before they occur and reduce engineering time by up to 70%. Additionally, for a $1 billion company, every 1% improvement in OEE—like integrating advanced software that reduces equipment downtime—is worth approximately $7 million annually, further lessening costs and improving operational efficiencies.
Preventative Maintenance
Integrating third-party software to provide root cause analysis (RCA) identifies which asset issues led to underproduction or unplanned downtime. This process is vital in maintenance management, as it leads to more reliable operations, reduces downtime and saves costs in the long run. The software reports provide detailed data analysis, identify trends and facilitate communication—crucial for effective root cause identification and resolution.
The goal of an effective maintenance and reliability program is to provide the right maintenance on the right assets at the right time. The goal of a maintenance program is to reduce the failures (rates/frequency), to prolong the production uptime and to reduce production loss. However, many companies in the chemical process industries, for example, prefer to replace malfunctioning equipment with the latest technology instead of performing a critical evaluation of the maintenance plans.6 Material starvation in chemical processing can indicate unoptimized maintenance intervals upstream, causing the buffer inventory system between upstream and downstream assets to run dry before the maintenance is complete. This then creates unplanned downtime.
Implementing a preventative maintenance plan with RCA prevents recurring issues from happening by eliminating their root causes and providing information on the issues’ origins through insightful software reports. One hundred percent of the downtime captured includes stoppages of less than 10 minutes, which is often missed by manual data collection.
Predictive Maintenance
While preventative maintenance relies on best practices and historical data, predictive maintenance (PdM) takes measurements from machine operations as they are occurring and uses this data to raise red flags when indications of a problem are noted.7 Like preventative maintenance, PdM is a proactive approach and maintenance is only performed on machines when it is necessary. McKinsey Global Institute reports that implementation of PdM practices across manufacturing will have a $240 to $627 billion cost savings across the industry.
In the previously referenced Kimberlite study, companies in the oil and gas industry that use a data-driven, predictive approach see their downtime reduced by 36% compared to those with a reactive maintenance strategy. The result is $34 million in cost savings annually.
Supervisory control and data acquisition (SCADA) systems serve as the backbone of predictive maintenance initiatives by providing real-time data acquisition, monitoring and control capabilities across industrial processes. By harnessing the power of real-time data and predictive analytics, businesses can proactively address potential equipment failures before they escalate, thereby significantly reducing costly unplanned downtime. Seamlessly integrating third-party software that provides autonomous alerts, historical data analytics and reports with SCADA systems can lead to smarter decision-making, improved processes and a competitive edge.
Using asset data helps predict when a failure may occur by catching asset malfunctions as early as possible. This helps avoid the need for more significant maintenance activities or lengthy and costly downtime. Leveraging aggregated data offers economies of scale for managers. With a summation of performance across all machines, larger performance inefficiencies become evident, and managers can develop a deeper understanding of their machine performance, people performance and process performance.
Meeting Industry Challenges
The efficient operation of machinery and processes is vital to meeting production targets, maintaining quality control and increasing profitability. Regardless of the industry, machines breaking and stopping is one of the most common causes of unplanned downtime. Equipment failure and technical glitches can bring a production line or system to a sudden halt, but it does not have to be this way. The integration of accelerator plug-in apps and advanced software allow companies to be nimble and targeted with improvements for operational efficiencies.
References
- Sundeep Ravande, “Unplanned Downtime Costs More Than You Think,” Forbes Technology Council, February 22, 2022
- maxgrip.com/resource/article-the-cost-of-unplanned-downtime (accessed November 20, 2024)
- pharmaceuticalprocessingworld.com/equipment-reliability-is-key-to-operational-integrity-in-life-sciences-manufacturing (accessed November 20, 2024)
- cdsvisual.com/blog/confronting-the-high-cost-of-downtime-mining-industry-with-ai (accessed November 20, 2024)
- dispel.com/blog/how-digital-transformation-reduces-unplanned-downtime-in-the-energy-sector (accessed November 20, 2024)
- pmc.ncbi.nlm.nih.gov/articles/pmc7543700 (accessed November 26, 2024)
- advancedtech.com/blog/preventive-vs-predictive-maintenance (accessed November 18, 2024)
- maxgrip.com/resource/article-the-cost-of-unplanned-downtime (accessed November 21, 2024)