Dissolved Air Flotation (DAF) is a wastewater treatment process for removing suspended solids, oils, fats and other contaminants using air bubble flotation. This method dissolves air under pressure into water, mixes the dissolved air and water with the waste stream and releases the air from solution while in contact with the contaminants. Air bubbles form, attach to the solids, increase their buoyancy and float the solids to the water’s surface. Air is injected under pressure into a recycle stream of clarified DAF effluent. This recycle stream is then combined and mixed with incoming wastewater in an internal contact chamber where dissolved air comes out of solution in the form of very fine bubbles that attach to the contaminants. The bubbles and the contaminants rise to the surface and form a floating bed of material that is removed by a surface skimmer into an internal hopper for further handling.
Smart Measurements
Making smart measurements of the compressed air system will reduce maintenance and energy costs as well as ensure proper operation for all equipment requiring consistent air delivery. The measurement equipment is relatively inexpensive. Monitoring power use, air flow and air pressure ensures a properly working system, but other measurements like dew point and temperature can also help a system operate with better results. By measuring the air flow, pressure and energy use, users can generate a baseline of the system operation. Typical flow data in a compressed air system is measured in cubic feet per minute (CFM)..jpg)
Raw Water Intake
Raw water intake into the DAF is another critical measurement that requires consideration before implementing a flow strategy. Since most treatment systems start with flash-mixing sulfuric acid and ferric chloride into the raw water to adjust pH, and the water will be disinfected for bacterial using some form of oxidation like sodium hypochlorite and then sodium hydroxide, care should be taken to ensure that the flow meter selection takes material corrosion protection in mind. Depending on the plant process, some raw water intakes may include a percentage of solid wastes, such as raw water from poultry processing, making the selection of flow meters with no moving parts or even non-invasive flow meters like clamp-on ultrasonic meters more attractive. Similar to the air flow rate flow meter, the influent raw water flow meter will require an electronic output for communication to the DAF programmable logic controller (PLC) or control interface unit to set the ideal rate for the optimum air to solids ratio. Adjusting the raw water intake to the DAF with the correct amount of air flow to the air diffuser will require accurate, reliable measurements for optimum control. The most important operational parameters for contaminant removal by dissolved air flotation are air pressure, total raw water/recycle or slip stream flow rate, influent total suspended solids (TSS) including oil and grease, bubble size and dispersion. Air pressure, recycle and influent TSS are normally related in an air-to-solids (A/S) ratio expressed as Equation 1.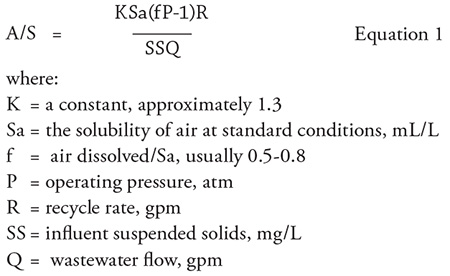