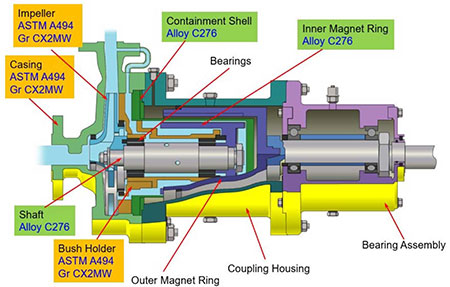
Hydrofluoric (HF) acid is hydrogen fluoride in water. It is highly corrosive and is known for the ability to penetrate almost any material it comes in contact with. HF acid is often used to dissolve materials such as glass, ceramics, metals and organic matter. It is also used in the refining industry to produce gasoline.
HF alkylation, or HF acid alkylation, is a chemical process used to refine high-octane gasoline components. In the HF alkylation process, feedstocks such as isobutane, olefin, propylene or butylene are mixed with HF acid. This reaction creates branched chain alkylates, which produce “anti-knock” properties in gasoline. Alkylates are blended with other gasoline components to increase octane levels and to improve the quality of gasoline blends.
HF alkylation produces higher quality gasoline, but it also poses significant safety and environmental risks due to its toxic and corrosive nature.
For decades, pumps and other equipment used in HF acid alkylation have been vulnerable to corrosion because HF acid by its very nature attacks imperfections in cast components. This can lead to pump failures, product leakage and environmental and safety concerns. HF acid typically damages pumps in the following ways:
Corrosion: HF acid corrodes pump internals made of commonly used metals including carbon steel, stainless steel and cast iron. Prolonged exposure to HF acid can reduce material integrity, corrode pump components and lead to the loss of mechanical strength.
Chemical attack: Due to its highly aggressive nature, HF acid can chemically attack the surface of most metal components, causing them to degrade and wear away over time. This reduces efficiency and leads to leaks.
Seal and gasket damage: HF acid has a proven track record for degrading seals, gaskets and other elastomeric materials commonly used in pumps. This typically leads to a loss of containment, leaks and safety hazards. For this reason, sealless magnetic drive pumps are the preferred choice for handling HF acid in refining applications.
Eliminating pump seals eliminates one of the most prominent risk factors, but there are other important design features to consider in any pump used for HF acid service:
Casing: The outer shell or housing of the pump, this is the part of the pump that contains and directs the flow of fluid through the pump discharge and encloses the internal components. The material of the casing is chosen based on factors such as the fluid being pumped, operating conditions and corrosion resistance requirements. Common materials for casings include cast iron, stainless steel and plastics or composites; however, many of these materials are vulnerable to HF acid.
Casting: A pump’s casting refers to the manufacturing process where molten material (usually metal or plastic) is poured into a mold cavity, which contains the desired shape of the component. Once the material solidifies, the mold is removed, leaving behind the finished casting. Castings are integral to the production of pump components, including casings, impellers and other parts. These cast components play crucial roles in the performance of the pump. Various materials can be used for casting, including cast iron, stainless steel and carbon steel as well as nonmetallic plastics and composites. This variety enables pump designers to select properties that are tailored to the specific requirements of the pump application.
Selecting Pumps for HF Acid Service
The primary goals for selecting pumps used in HF acid service are performance, reliability and safety. Handling HF acid presents safety risks to pump operators and maintenance personnel. Leaks or accidental spills of HF acid can result in exposure to corrosive vapors and fumes, skin contact and inhalation of toxic gases, which can be fatal to plant personnel.
For these reasons, the following criteria should be considered when selecting pumps for HF acid service:
- Sealless magnetic drive pump technology with full compliance with American Petroleum Institute (API)
685 standards - Specially adapted material design from high nickel alloys that have a proven track record standing up to HF acid
- Extensive testing and validation using nondestructive examination (NDE) for the pump casing
- Secondary containment
- Monitoring technology with leak detection
- Aftermarket services process expertise from professionals that are intimately familiar with HF acid service
Sealless Magnetic Drive Technology
Mechanical seals can leak over time. With HF acid service, seal leaks are inevitable. Removing the seals removes the most common point of failure. Sealless pumps are somewhat like conventional centrifugal pumps, but they do not have packed glands or seals. The seals are replaced by a static containment shell or shroud that forms a completely sealed liquid end or pressure boundary, removing any potential leak paths. Sealless magnetic drive pumps do not require seal support systems and have fewer working parts, so they are easy to design, install and maintain.
Specially Adapted Material Design
Decades of experience have shown that standard cast iron, stainless steel and carbon steel do not stand up to the aggressive nature of HF acid. A combination of materials has been created specifically for HF acid service. This industry-approved design features Alloy C276 wrought parts and Alloy C22 castings. The pump casing casting uses a specially adapted and repeatable manufacturing process that ensures integrity in HF acid service.
Nondestructive Examination
In addition to an adapted casting process, manufacturers designing pumps for HF acid service should implement a tailored NDE process to check for imperfections in the casting and also to validate the casting’s integrity for use in HF Acid. This process, combined with the following traditional methods of NDE (in line with the API 685 standard) verifies pump suitability for HF acid service:
- Visual inspection
- Radiography
- Dye penetrant testing
- Positive material identification
Secondary Containment
To further guard against the unlikely occurrence of a primary containment shell leak and to meet increasing safety and environmental regulations on-site, a secondary containment system should be deployed, featuring a dry-running mechanical seal between the rotating drive shaft and the static coupling housing.
This forms a secondary pressure boundary and provides a fully independent secondary containment system. In the unlikely event of a primary containment shell breach, the pump would be shut down, and any leaked fluid would be contained within the secondary containment area, preventing escape to the atmosphere.
Monitoring Devices
Instrumentation devices should be used to continuously monitor the condition of the pump and to detect the occurrence of any leaks within the pump primary containment boundary. Monitoring technology provides vital information for temperature anomalies in the pump internals and absorbed power. It helps to warn operators of adverse conditions, and it provides data that can be used to undertake early remedial action that can minimize future maintenance and maximize a pump’s operating life.
Process Expertise & Local Aftermarket Services
Addressing all of the criteria for pumps used in HF acid service provides a solid foundation for success. But even with all of the best practices implemented, any piece of rotating equipment will require service over a long period of time. Operators deploying pumps for HF acid service are aware of the issues that pose problems for their pumps.
It is easier for operators to plan and implement maintenance when they work with a pump manufacturer whose global aftermarket service and support group understands these problems and possesses expertise on the process. This makes the ordering (and receiving) of spare parts easier, simplifies repairs and refurbishments and helps to maximize a plant’s uptime.
HF alkylation will continue to be a critical part of the refining process for many years to come. The good news is, the best practices associated with safely handling the harsh chemicals required by the process are well understood by refineries, and the pumping technology best suited for these processes is ready to be deployed.