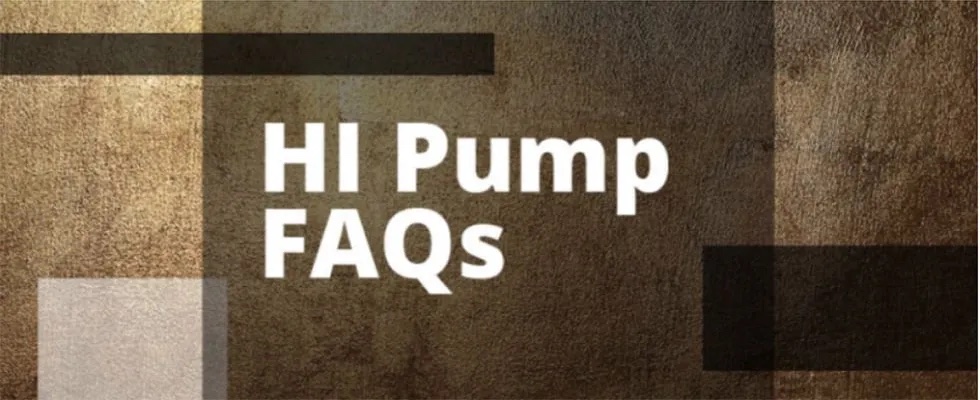
A pump driver is the device responsible for powering a pump. It applies the torque necessary to spin the shaft in most typical designs, thereby moving the impeller and the fluid in the pump. There are a variety of drivers, each with their own applications. The most common is an electric motor, specifically an asynchronous induction motor. Image 1 details the key components of a typical three-phase induction motor, which can be described as follows:
Stator – The stator is a stationary cylinder that houses metallic windings. When a varying electric current is applied to these windings, they create a rotating magnetic field.
Rotor – The stator’s rotating magnetic field is used to turn the rotor, another cylinder within the stator’s outside diameter, which contains electric conductor bars mounted around it. The magnetic field interacts with the rotor’s conductor bars to turn the rotor.
Shaft – The rotor is connected to the shaft, which connects the rotor to the pump and transfers its rotational energy to the impeller.
Bearings – The rotor and shaft are supported by bearings that allow them to turn smoothly. They minimize the friction experienced by the rotor and allow for as much energy transfer as possible to occur from the incoming electric power to the pump.
Housing or casing – All the components of the motor are housed in a protective casing that shields them from the environment and supports heat transfer.
IMAGE 1: A labeled model of a typical asynchronous induction motor In certain situations, drivers other than an asynchronous induction motor are used. Electronically commutated motors function similarly to the induction motors described above but require a variable frequency drive to operate. They are generally more efficient and can adjust in real time to conform to varying demands. When electric power is not available, internal combustion engines can also be used as a pump driver. A third alternative driver is a steam turbine, which uses the energy from high-pressure steam to turn the pump. Steam turbines are often used in environments where steam is generated to support the process, such as power plants and paper mills.
Pump drivers are responsible for creating the rotational motion necessary for a pump to function. There are a wide variety of drivers for various situations, and the ones discussed here are some of the most common. The Hydraulic Institute features more in-depth discussions on pump driver function applications in their webinars, available at training.pumps.org.