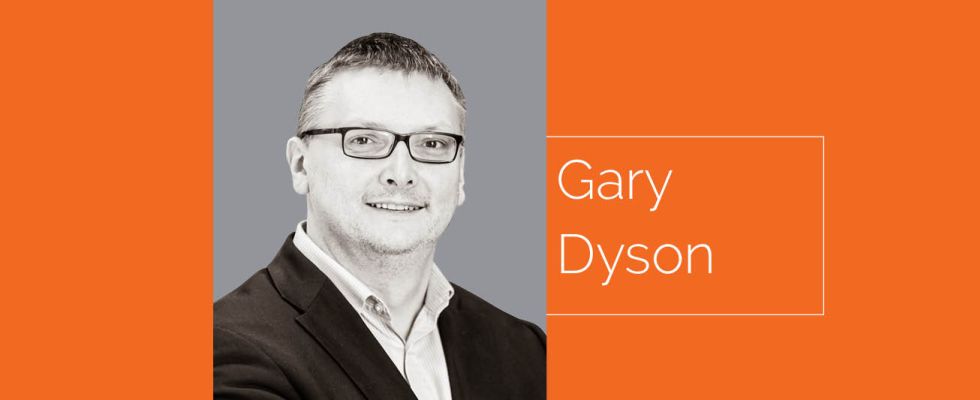
It is good practice to view pump efficiency as a combination of three factors coming together to determine the headline efficiency number. These factors are:
Mechanical Efficiency:
The amount of mechanical power required to turn the rotor and overcome friction from bearings, seals, disc
friction, etc.
Hydraulic Efficiency:
The design’s capability to process the fluid through the passageways of the impeller and casing effectively.
Volumetric Efficiency:
The design’s ability to move all the fluid that enters the suction nozzle out to the discharge nozzle. Generally, wear ring geometry has a significant impact on this.
Pumps of different specific speeds (Ns) have different characteristics that influence which of these factors is dominant. A low-Ns pump will be low flow and higher head per stage. This leads to a high differential pressure across the wear ring landing, and this driving force across the ring leads to a bigger loss. Additionally, low-Ns pumps will have a relatively low flow, so as a percentage of total flow, the lost flow across the ring will be higher.
The reverse would be true for a high-Ns pump, and the volumetric loss would be a smaller percentage.
Understanding the dominating factors based on the distribution of losses makes it easier to target the correct methodology for improving pump efficiency. There have been many claims made about the ability of new materials to significantly improve pump efficiency by reducing the wear ring clearances by 50%. These claims are generally true but only in specific instances where the dominating factor within the distribution of loss is volumetric.
When looking at pump curve, it is tempting to view pump efficiency as independent of the process. Pump modifications to improve pump efficiency can be valuable, but the actual objective is saving consumed power as opposed to improving pump efficiency.
Improving pump efficiency numbers against the original pump manufacturers curve may be mostly insignificant, as the pump is just one element in an interconnected system where piping system, driver efficiency, pump efficiency and process requirements all overlap to provide the real answer. An approach based on overall system efficiency is the way to target the largest power savings.
Some Considerations of Loss
Control valve
Spending money on power to generate head from a pump and then throwing away this head across a control valve is a common practice, as pumps are often sized for multiple process conditions. Is the pump a match to the process?
Operating regime
Having a highly efficient pump and running that pump 50% back from best efficiency point (BEP), where efficiency and reliability are considerably less, is a consequence of an incorrectly sized machine.
Driver configuration
Each component of the drive chain has an efficiency number. Every value for motor and gear box must be taken into consideration when assessing the actual power consumption.
Drive component efficiency
Some variable speed systems have a dramatic reduction in efficiency when the machine is not running at maximum speed.
Process
There may be aspects of the process that damage efficiency. For example, abrasive and hot fluids can damage pump efficiency and reliability. Maintenance is expensive, and addressing reliability issues may be preferable to addressing power consumption.
Pump efficiency should not be the primary objective when looking at the cost of ownership. The complex interconnecting variables of pump, driver, process and system provide a greater opportunity for savings. Understanding where to target efforts to generate the largest saving with the least effort/cost is an important consideration.