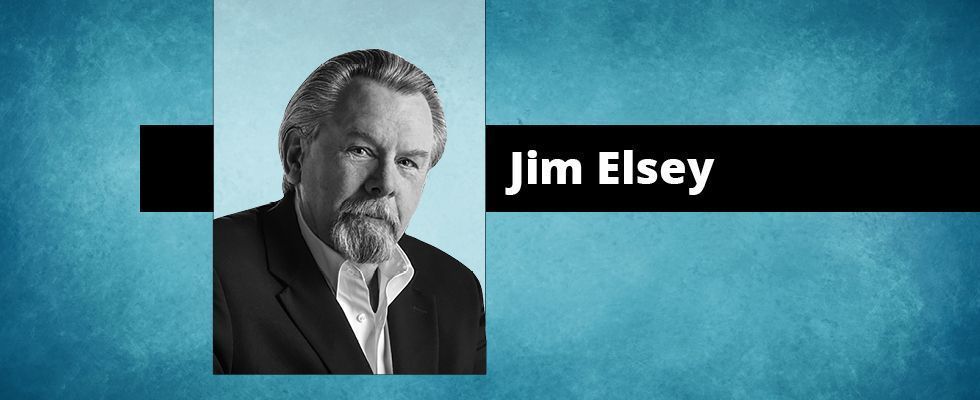
I often talk with pump owners/operators who question why a given pump is not performing to the manufacturer’s published performance curve. Of course, there is a long list of reasons why this problem can occur, and I will explain a list of potential issues in this column. One possible answer is that the pump is performing just fine but it could be that you are not measuring the performance correctly.
Initially, understand that pump performance tests conducted in the field (in situ testing in the owner/operator’s system) are rarely as accurate as a factory test. The disjunct is normally due to the accuracy, calibration schedule and placement of the instruments. Other pertinent factors are the size and geometry of the piping. Further, there is a long list of items that includes the proper calculations, methods and compensation of/for the readings for torque-speed, atmospheric pressure, acceleration head, temperature, specific gravity, viscosity, air entrainment, net positive suction head available (NPSHa), critical submergence, Newtonian properties, friction losses and elevation corrections to a specific datum point.
Additionally, pumps tested at the test facility will have the proper settings, clearances and lubrication. They also have the positive benefit of being new.
Pressure Gauges & Transducers
Except where noted, I will use pressure gauges, digital gauges and transducers interchangeably in this column. These instruments are sold in a wide variety of accuracy grades where higher accuracy typically equates to higher cost. The accuracy of most gauges used in commercial and industrial applications is markedly less accurate than laboratory, precision or test instruments. A laboratory gauge may be accurate to +/- 0.05% over the entire span of the instrument range while most commercial units are doing well to be within +/- 2% of the reading and may be worse over the entire span.
There is a difference between accuracy and precision and again between accuracy and resolution. Just because a digital gauge reads pressure to two decimal places (resolution) does not mean it is accurate. Resolution is defined as the smallest increment of pressure change that the sensor can reliably detect. Accuracy is defined as how close to the actual true pressure the instrument reads. Precision is an indicator of consistent and repeatable measurements. The person reading the gauge along with the size of the dial (resolution) will also be a factor. The smaller the dial, the less resolution so the higher the tendency for human error in reading the gauge accurately. Many gauge dials in the field are 1.5 to 2 inches in diameter while a laboratory or test facility gauge may be 16 inches. The angle that the gauge is viewed will also come into play.
Note: Gauges of an incorrect range are often installed. It is good practice to use a gauge that will be midrange or the middle one-third range for the pressures you expect to be measuring. It will be difficult and inaccurate to attempt to measure the difference between 2 and 5 pounds per square inch gauge (psig) on a 0 to 200 pounds per square inch (psi) gauge.
Gauges in service/operation will lose accuracy due to temperature changes, vibration and pulsations. Pressure measurement is also subject to “drift” and over time there are hysteresis factors along with nonrepeatability and nonlinearity factors to be considered, which is why periodic calibration is also required to maintain accurate readings.
The test lab gauges will be calibrated on a rigid schedule at frequent intervals while many gauges in the field will not be calibrated with any rigor or at all. Apologies and kudos to the facilities that do have formal calibration schedules and procedures.
Where to Measure
The placement of the instruments makes a difference in the readings. In theory and practice, the manufacturer is guaranteeing the pump performance (head and flow at a minimum) within a given tolerance. The differential pressure data points for a pump are the suction and discharge flanges but those are also poor locations for instruments to report accurately. In the test facility, a pump’s suction and discharge pressures are normally monitored at least two pipe diameters away from the flanges (more is probably better), and yet we still need to correct the pressure (head) readings to account for the friction losses in those short pipe sections to bring the datum point back to the flanges.
Due to recirculation issues, especially at operating points on the left side of the pump curve, the suction pressure can be affected by recirculation issues that will cause erroneous readings. Wherever you measure pressure, the corresponding liquid velocity profile needs to be symmetric. Something as simple as the size and profile of the gauge tap and the position in relation to the geometric plane of the pump volute will deter from the accuracy.
The elevation of the gauge (plus or minus) in relation to the pump datum plane must also be compensated for in the calculation of head. Additionally, the temperature and density of the liquid and the local atmospheric pressure (elevation above sea level correction) must be considered. For pump testing, the base standard liquid is water and the temperature is 68 F or 20 C. If the water temperature falls between 50 and 86 F (10 to 30 C) there is little need to compensate for temperature as the error is minor.
Pressure gauge accuracy is affected by ambient temperature due to the change in the modulus of elasticity of the bourdon tube. Normally not an issue but in cases of extreme temperature changes, check with the manufacturer for values of range shift.
Pump Curves
The published pump performance curve from the manufacturer (aka factory curve or price book curve) represents typical hydraulic performance. Your pump performance in the field (better or worse) will be different for the reasons already stated and because there are casting and manufacturing tolerances in the total equation. The manufacturer tests the pump and publishes the results as validation and assurance of the performance and the veracity of the pump model. You should also know that most commercial and industrial pumps are not individually performance tested. The manufacturer is simply stating with a published curve that similar pumps of the same design, model and size will perform within some stated tolerance of the tested pump.
Most manufacturers will retest pumps periodically to revalidate the performance. The tolerance range will be dictated by the intended pump service and a few other factors including the power range. These general tolerances are normally within +/- 2% to 6% but could be higher depending on the pump test grade. Tolerances will be lower for an agreed guarantee point. Details are defined in American National Standards Institute/Hydraulic Institute (ANSI/HI) standard 14.6.
Manufacturing Tolerances
Pump volutes/casings and impellers are cast pieces. Inherent with the casting process are both dimensional and surface finish tolerances. Investment casting will yield markedly better dimensions and finishes over simple sand castings. Of course, implied by the descriptor “investment,” they also require higher costs. An impeller and casing with a smooth surface finish will be more efficient due to less friction than a piece that has a rough surface finish. In addition to casting tolerances, there are also manufacturing/machining tolerances and finishes. If you are manufacturing thousands of pumps per year, the ability to keep your tolerances and finishes within the same specification range over time and in large quantities is both paramount and the signature of a good manufacturer.
Other Factors
Air entrainment as little as 1% can negatively change the pump performance. Viscosity values even as low as 15 centipoise will deter from full pump performance. You will need to correct flow, head and efficiency for the liquid’s viscosity. See HI Standard 9.6.7 for details (“Effects of Viscosity on Pump Performance”).
If you don’t use the correct specific gravity to convert from pressure to head, the calculations will not be accurate. Flow meter placement and the type/technology selected will affect the instrument’s accuracy. Follow the manufacturer’s directions explicitly for the amount of straight run piping prior to the meter, and note some meters will be sensitive to orientation. Portable meters will present caveats on proper placement; your knowledge of the velocity flow profile and the presence/absence of solids in the liquid stream will be key to a successful installation.
Pipe size and geometry will typically present obstacles to obtaining measurement accuracy. In the name of reduced footprint, I often see 90-degree pipe elbows and suction strainers with low valve flow coefficients (Cv [high pressure drop]) immediately adjacent to the pump suction, which, in addition to affecting performance, will render both the pressure and flow readings inaccurate. I also witness suction side velocities over 10 to 15 feet per second (3 to 4.6 meters per second) and on a few occasions even more, which will make the pressure reading inaccurate because the gauge/transducer cannot sense the component of velocity head.
Pump performance is dependent on the proper operating clearances and settings. Please see the pump manual and/or manufacturer for guidance in this area.
Speed is a critical factor to pump performance. I don’t see this issue often but when I do, it sticks vividly in my mind. As examples: variable frequency drives (VFDs) set or programmed incorrectly, the wrong set of belts and sheave sizes, an incorrect gear size, an induction motor that single phases, a turbine that has a faulty governor, and at remote sites I see the diesel generator frequency switch set for 50-cycle operation on a 60-cycle application. When in doubt, measure the speed to eliminate the factor on the list of reasons for off-peak or nonperformance.
If the pump is cavitating, the performance will be adversely affected. Measure or calculate the net positive suction head (NPSH) margin to ensure the pump is operating in a satisfactory range. The pump will operate where the system curve intersects the pump curve.
It is common practice in some facilities to operate the pump at shutoff head even if for short periods to “check the health” of the pump. Due to recirculation issues, the pump performance at shutoff head (no flow) will be difficult to measure accurately because of rapid temperature changes and the inability to compensate for velocity head. I recommend that perhaps some small amount of flow will allow for a more accurate test and, of course, for only a brief moment. The more energy involved, the less I recommend this practice. It is a good decision to check with the manufacturer.
A pump test in the field will have different results than a test conducted at a manufacturer’s facility. There is always some degree of uncertainty. As they say in commercials: your results may vary. For more information on the subject of pump performance, please refer to my columns in the July 2017, August 2019 and February 2020 editions of Pumps & Systems magazine.