Pump repair and rebuild shops are integral to the pumping world. Industrial pumps are not a cheap commodity, so the ability to refurbish an old pump to extend its working life is immensely beneficial.
Pump rebuilders may come across a wide variety of pumps, from centrifugal slurry pumps to vertical submersible pumps. These pumps are used in many applications, including pulp and paper production, municipal water distribution and boiler feed applications. Despite the variety of pumps that rebuilders may encounter, they are often tasked with the same thing for each rebuild job they come across—bearing replacement.
The function of a bearing is to support a moving shaft. As such, there will inevitably be some rubbing that occurs during operation and, consequently, some bearing wear. This means bearings are often one of the first components in a pump that need to be replaced, regardless of what type of bearing is used. This is why it is important for pump rebuilders to become familiar with the different types of bearing materials used in pumps, especially more common ones like carbon graphite.
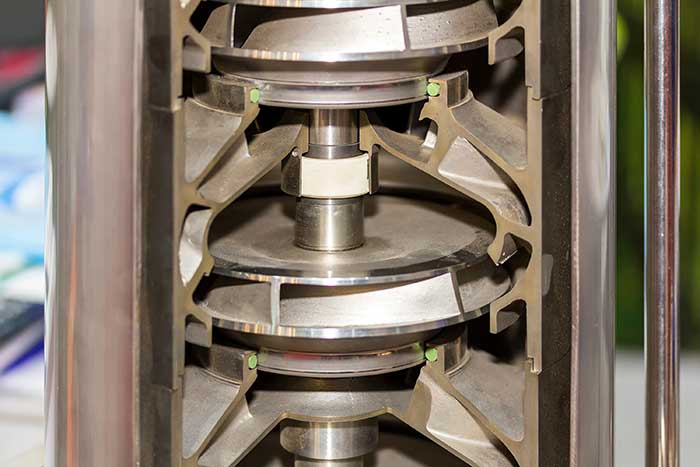
Carbon graphite bearings are used in pumps for many reasons. Since there is no metallic attraction between carbon graphite and the shaft, these bearings are not prone to galling or seizing, which is a known failure mode of other types of bearings. Carbon graphite is self-lubricating, so it can run dry in certain conditions without the need for grease or oil lubrication.
Carbon graphite bearings also have thermal and chemical resistance, which is crucial when pumping hot fluids or caustic chemicals.
Choosing the Base Carbon
The base carbon graphite of most bearing-grade carbons is coarse-grained carbon graphite rod. Coarse-grained carbon graphite rod is formed by extruding raw carbon graphite powders through a die of a set outer diameter (OD).
These “green” (or unbaked) extruded rods are then sent through a baking process, which carbonizes the binder to form what is referred to as mechanical carbon graphite.
After the baking process, the material should have sufficient strength and hardness to be used as a bearing in certain pumping applications.
Relative to compaction molded carbon graphite, which is a more fine-grained material, extruded carbon graphite is softer and is often a better choice for press fitting into a housing. This is one of the reasons why extruded grades have been historically specified in many pump designs and are often the material of choice for pump rebuilders.
Optimizing Dry Running & High Temperature Capabilities
For certain dry running or high temperature applications, carbon graphite may not have sufficient lubricity or oxidation resistance to operate.
In these situations, carbon graphite manufacturers can re-bake the material at high temperatures, causing the carbon graphite to graphitize and form plain graphite. This process increases the ratio of graphite grains to amorphous carbon within the carbon matrix.
The layered structure of the graphite grains causes the material to become much more lubricious, which enhances its dry running capability. Graphite also has less “active sites” that are prone to oxidation, allowing it to withstand exposure to higher temperatures for longer durations.
Proper Impregnation Type
Depending on the application, the base carbon/graphite can be used as the bearing material alone, or it can be impregnated with metals, resins, salts, etc. The type of impregnation used affects the ultimate material properties of the carbon graphite, so choosing the proper impregnation grade is essential.
The type of impregnation depends on the type of pump and the physical conditions the bearings will be exposed to. Although different types of impregnations exist, three in particular have proven to perform the best in a wide range of pump applications: babbitt, nickel and resin.
- Babbitt is a soft metal with strong lubricating properties. This is best for low temperature water applications where the bearing is running submerged.
- Nickel-impregnated carbon graphite is strong and has the best corrosion resistance. It is commonly used in boiler feed pumps and high load applications.
- Resin-impregnated carbon graphite provides chemical resistance and is usually used in lower-duty applications.
Although the properties of each impregnation type vary significantly, the primary function of each is to fill carbon graphite’s porosity. This is critical, because an impervious material is necessary for the formation of a hydrodynamic fluid layer between the bearing and the shaft needed in submerged applications.
This layer serves to extend the life cycle of the bearing, since it acts as a protective boundary between the two rubbing surfaces.
Installation Tips
Once the proper material grade is selected, pump rebuilders are tasked with installation of the bearing. Carbon graphite is a brittle and soft material, so it is important that bearings are handled with care during the installation process. Most carbon graphite bearings are press-fit into a housing, but may require some other means of installation in certain cases.
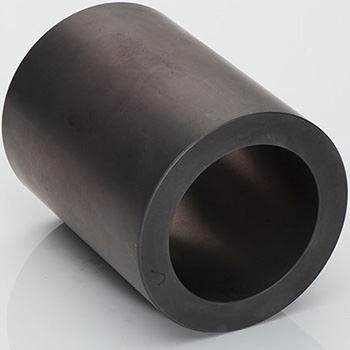
It is also important to use the correct interference. The interference depends on a number of factors, including application temperature, housing material, bearing material and other considerations. The manufacturer can assist with this calculation.
- For tight interference fits, heat the housing to decrease the interference during installation and allow the bearing to press-fit more easily.
- For tight interference fits, the carbon graphite bearing can also be cooled with liquid nitrogen to further reduce the interference.
- Guide the bearing into place with lead-in chamfers on both the bearing outer diameter and the housing inner diameter.
- Press fit bearings in a single motion at a constant rate.
Machining the ID: Running Clearance Properly
After the press fit, it is common that the ID may need to be machined to account for any “close-in” that occurred during installation as a result of the press fit.
It is possible to predict this “close-in” and design the bearing accordingly to avoid having to machine the ID. However, this may not be manageable if the tolerances and/or clearances are too tight.
When machining the ID, keep in mind that a proper running clearance must be maintained between the shaft and the bearing.
For most submerged applications, it is recommended that this running clearance is 0.1 to 0.3 percent of the shaft diameter. This allows for sufficient space for a hydrodynamic fluid layer to form, while preventing excess space that could cause rattling or increased localized wear.
Once the bearing is press fit and the ID is machined to size, the bearing installation is complete.