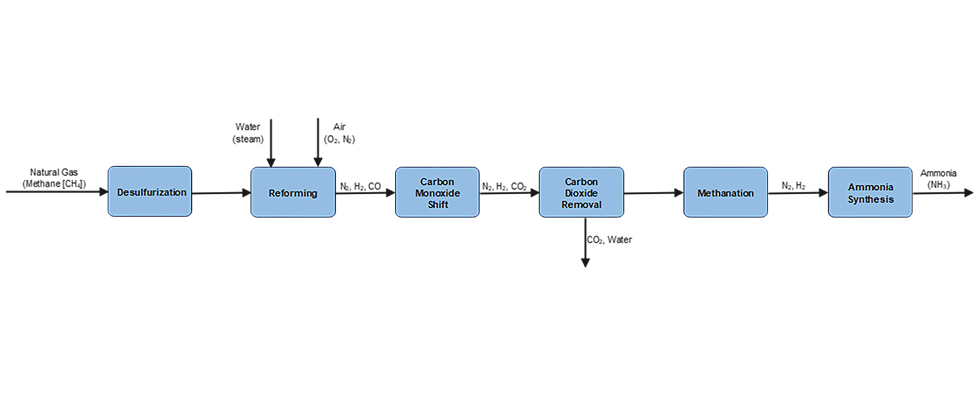
Hydrogen is the lightest and most abundant element in the universe. For decades, hydrogen has been used to make a wide range of products, including steel, chemicals, petrochemicals and fertilizers. Hydrogen plays an important role in refineries (in hydrocracker and hydrotreater applications). Over the last few years, hydrogen has become a key component for renewable energy via fuel cells and turbines, and it is also used to power a wide range of transportation vehicles, such as buses, cars, forklifts and large container ships.
To be used in its pure form, hydrogen has to be extracted from other molecules, such as water or hydrocarbons. To be stable, hydrogen must be a diatomic molecule (H2) with two electrons. H2 can be produced, or extracted from other molecules, in a number of ways. The most common processes include natural gas reforming, coal gasification, biomass gasification, biological production, solar production and electrolysis. Today, most hydrogen is produced using coal or natural gas as feedstocks. Both of these processes emit byproducts into the atmosphere, including carbon dioxide. So, while hydrogen itself is eco-friendly, the processes used to isolate the chemical element still produce an environmental footprint.
Using Hydrogen as Energy
Hydrogen can be stored for extended periods of time, which makes it a valuable complement to other sources in the electricity system. Hydrogen is an efficient fuel source, with high energy content per weight. On a mass basis, hydrogen has nearly three times the energy content of gasoline—120 megajoules per kilogram (MJ/kg) for hydrogen versus 44 (MJ/kg) for gasoline—but on a volume basis, the story is quite different. A volume of approximately 11 cubic meters (m3), or 388.5 cubic feet (about the volume of the trunk of a commercial vehicle), is needed to store just 1 kg of hydrogen—or a quantity needed to drive 100 kilometers (km). Gasoline has almost 3,000 times the volumetric density of H2 at atmospheric pressure. This means hydrogen compression is required in order to attain functional levels of energy density.
Methods for Compressing Hydrogen
There are three popular types of compressors used for hydrogen, and each has strengths and weaknesses.
Centrifugal compressors are a popular choice for pipelines, recirculation or drying applications in refineries where large gas flows are required. These types of compressors are highly reliable, are in accordance with API 617 standards and generally have low operating expenses (OPEX) due to a minimal number of wear and tear parts. When it comes to hydrogen, centrifugal compressors offer a moderate pressure ratio. Given the low molecular weight of hydrogen, this type of compressor requires multiple casings/stages to deliver the high compression ratios needed for mobility applications.
Reciprocating compressors are also designed to handle large gas flows. They deliver higher compression ratios and are generally considered easier to operate than centrifugal compressors. When it comes to many hydrogen applications, product purity and non-contamination of the gas is paramount. The oil-lubricated piston designs for reciprocating compressors can be prone to leaks and contamination of the H2 gas, so for mobility applications involving fuel cells, a reciprocating compressor is not the preferred choice.
Diaphragm compressors provide lower flow than reciprocating or centrifugal designs, but they are engineered to ensure zero leakage to the atmosphere and absolutely no contamination of the process gas, making it a preferred choice for mobility applications. Diaphragm compressors offer a high compression ratio (up to 10x per stage), and they are known for reliability and low maintenance requirements.
Which type of compressor is preferred? Ultimately, it comes down to the application, as each type of compressor features strengths for specific applications.
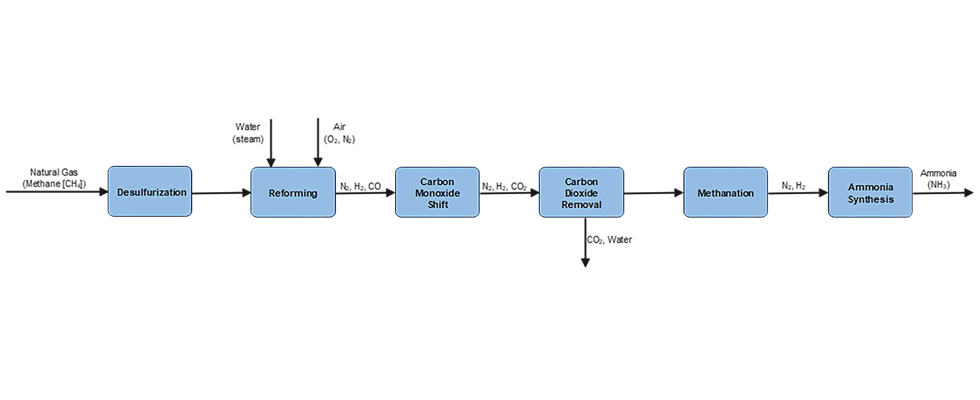
Pump Considerations for Processing Hydrogen
Electrolyzers are beginning to occupy a larger role in hydrogen processing. They use electricity to break water (H2O) into hydrogen and oxygen through a process called electrolysis. Most electrolyzers feature a cathode (negative charge), anode (positive charge) and a membrane. When electricity is applied, H2O splits into its component molecules, and H2 is extracted. Many types of pumps can be used to move large quantities of water into electrolyzers.
Water is not the only fluid pumped into an electrolyzer. Caustic chemicals, such as potassium hydroxide (KOH) or sodium hydroxide (NAOH) are required to increase the pH of water in the electrolyzer. During electrolysis, hydrogen is removed from water, which lowers the water’s pH on the anode side, making the water more acidic.
Just as water treatment plants pump caustic chemicals to balance (or increase) pH, electrolyzer applications do the same. As such, the pumps used must be able to stand up to the harsh nature of the chemicals being pumped, and they must do so for a long period of time. For this reason, sealless magnetic drive pumps are a popular choice for electrolyzer applications.
Pump Considerations for Transferring & Storing Hydrogen
Hydrogen is a diatomic gas under normal room temperature and atmospheric pressure; however, at extremely low temperatures and high pressures (known as the critical point), hydrogen undergoes a phase transition and becomes a liquid. The critical temperature is approximately -240.17 C (-399.3 F), and the critical pressure is approximately 12.8 bar (185 pounds per square inch [psi]).
To liquefy hydrogen, it is cooled to temperatures well below its critical temperature. The cooling process also involves applying pressure to bring it into a liquid state. Liquid hydrogen is used in various applications, including as rocket fuel, in cryogenic research and as a potential energy carrier for emerging technologies.
It is important to note that handling and storing liquid hydrogen requires specialized equipment and facilities due to the extreme cold temperatures involved. Liquid hydrogen is stored and transported in cryogenic containers that can maintain the low temperatures required to keep hydrogen in its liquid form.
NH3 to H2: An Efficient & Affordable Alternative for Transporting Liquid Hydrogen
To fully exploit the climate-friendly effect of green hydrogen, an efficient and sustainable alternative is needed. This is where ammonia comes into play. Ammonia can serve as a hydrogen and energy carrier. Today, ammonia is the second most traded chemical in the world, with more than 20 million tons transported by sea each year.
Ammonia (NH3) is produced commercially via the catalytic reaction of nitrogen and hydrogen at high temperature and pressure. This is known as the Haber-Bosch Process. The production consists of six steps, as shown in the process diagram in Image 1.
Green ammonia is made synthetically by combining nitrogen with hydrogen in a process called ammonia synthesis, using renewable energy sources with zero carbon emissions such as wind, solar, hydropower and geothermal energy. This process typically involves a feedwater pump and a circulation pump, which can be either centrifugal pumps or sealless magnetic drive pumps. It also requires an H2 drier, which is typically a centrifugal compressor, and a syngas compressor, which can be either a reciprocating or centrifugal compressor. Once produced, the liquid NH3 is moved using an ammonia pump, which can be either a centrifugal or a sealless magnetic drive pump.
Ammonia offers a number of advantages over liquid hydrogen. It is less flammable than hydrogen and requires less energy to liquefy and transport. Liquid hydrogen must be stored at cryogenic conditions at or below –240 C/-399 F, whereas ammonia can be stored at –33 C/-28.6 F at atmospheric pressure. Ammonia has a higher volumetric energy density than liquid hydrogen, so more energy can be transported via ammonia for the same volume than in the form of liquid hydrogen. Once green ammonia arrives at its destination, it can be split back into green hydrogen and nitrogen.
As a result of these factors, green ammonia is an ideal hydrogen and energy carrier. The infrastructure needed to handle green ammonia is already in place at ports, ships and tank farms.
Looking ahead, it is safe to say the use of hydrogen or ammonia to power ships, trains, trucks, buses, cars or forklifts without carbon dioxide (CO2) emissions will increase in the years ahead. The good news is the rotating equipment used to produce, transport and store these energy carriers has a long and successful track record of handling hydrogen and ammonia.