In July 2008, oil and gasoline prices reached an historic high in the United States with costs soaring upward of $4 per gallon. Similarly, oil costs reached a record $147 per barrel. This phenomenon marked a renewed interest in domestic oil and gas exploration, drilling and production. Though oil and gas prices have since stabilized, advancements in drilling technology and hydraulic fracturing have directed considerable attention to a corridor of the Northeast known for abundant natural gas reserves in underground shale deposits, which were previously too cost-prohibitive to pursue.
One of the United States' "big four" shale deposits (joining Barnett, Haynesville and Fayetteville), the Marcellus Shale formation, spans roughly 600 miles from southwestern New York to West Virginia, and along the Appalachian states. The "shale sweepstakes" has brought particular attention to the Pennsylvania and New York areas, where an 18 million-acre concentration of this rich organic black shale rock layer has a thickness of up to roughly 250 feet, at depths of 5,000 to 9,000 feet. With its proximity to the large, natural gas-consuming population of the East Coast, the Marcellus Shale has proven a lucrative exploration site.
Though the first natural gas well was tapped in the shale under Fredonia, N.Y. in 1821, the shale proved too dense for the gas to be collected.
However, improvements to horizontal drilling in the 1990s, in combination with hydraulic fracturing, made it possible for gas to be released from shale deposits as deep as 10,000 feet below the Earth's surface.
Traditional well boring injects a single, vertical path through layers of minerals. This single puncture proved fruitless for deriving natural gas from shale, since the shale play was too compressed to allow air to escape through the punctured path. In contrast, horizontal drilling begins with a vertical puncture, then makes a 90 degree bend just above the shale layer. The drilling continues to forge a lengthwise path through the shale bed, while disturbing far less of the surface.
With the horizontal well drilled and cased, a charge is set that perforates the casing and cement, causing fractures in the shale bed. Hydraulic fracturing injects millions of gallons of water, sand and lubricating agents at controlled high pressures down and across the well. Sand from the mixture fills into the resulting cracks, expanding them and holding them open enough to allow natural gas to escape out of the well. As the horizontal drilling process continues through the shale bed, plugs are inserted and removed in series to allow the gas to flow through multiple fracture points to the surface.
Recovered water is stored in open pits, then delivered to a treatment plant, while the natural gas is shipped by tanker truck to a pipeline for delivery-unless a pipeline is on site.
Despite higher production costs, shale bed drilling continues to be on the rise due to its lower carbon content than oil and coal, abundant availability, estimated well life (20 to 30 years) and minimal environmental impact.
Like most things, natural gas exploration, drilling and production in the Marcellus Shale require massive fluid transportation. In the areas of Mansfield and Troy (PA), elevation differences call for higher pressure pumps to deliver water from the frac tanks to the well site.
To understand the role pumps play in the shale fields, it is important to understand the path liquid takes throughout the process. Some companies use pumps to pull water from local ponds. Other companies use pumps to fill tanker trucks that deliver water to the frac tank site from sites across the state. Frac tank sites are established in a common area that is typically the center of a group of well sites. From this common area, water is transported by pump through high density polyethylene pipe (HDPE) from the frac tanks to the well site.
At the well site, high pressure pumps inject the water, sand and lubricating agent mixture into the well. In some cases, the well site might be two to four miles away from the common tank area. This distance may include a pathway through temporary runs HDPE pipe over hills and through valleys, so it is important for the pumps along the pipe run to maintain pressure in the line. Most drilling companies rely on a water engineer to determine where to install pumps intended to maintain pressure in the HDPE lines, based on the elevations of the land from the frac tank pad to the well site.
Once the water has been injected, the spent water from the well (backwash water) is then pumped back to the center pad with the tanks and pumped back out again at the next site. The well drilling equipment requires million of gallons of water during the drilling process. When drilling begins, flow must be maintained or production will stop-at great cost to the drilling company.
"We have sent several pumps in our high-lift range to the multi-elevation sites in Pennsylvania, including 4 in by 3 in, 8 in by 6 in and our bigger 10 in by 8 in and 12 in by 10 in pumps," said Godwin Pumps Engineer Lisa Wurtz. "We sent our high volume 12 in pumps to the flatter frac sites in West Virginia, Ohio and around Pittsburgh (Penn.). Whether it is maintaining the volume of the flow or the pressure of the flow, we have been able to satisfy the broad ranging requirements for the drilling companies with our pumps. In addition, in instances where our pumps are near landowners' homes, we have also provided our critically silenced units to minimize noise."
"We have provided steel manifolds, HDPE manifolds, miles of HDPE pipe, flowmeters, high pressure road ramps rated to 100 psi, gaskets, flange adapters and back-up rings for HDPE, HDPE bends and HDPE tees," said Godwin Pumps Regional Manager Herb Schroeder. "We use suction hoses (4 in by 10 ft suction hoses with flanges) to connect to the frac tanks, and composite hoses with floating flanges at both ends to connect the pumps to the manifolds. We manufacture our components from steel to help improve equipment longevity for pumping the abrasive product found in these applications."
Technological improvements have undoubtedly made the shale sweepstakes a reality, and signs indicate that this development is still in its infancy. When considering pumping equipment and services for use in these environments throughout the Northeast corridor, be sure to consider weather, noise, materials of construction, range and versatility of the pumps available, and 24-hour service.
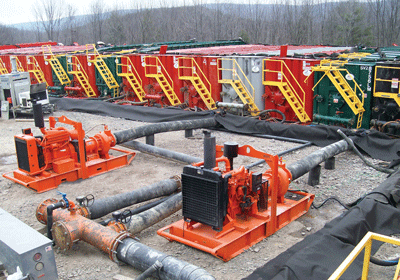
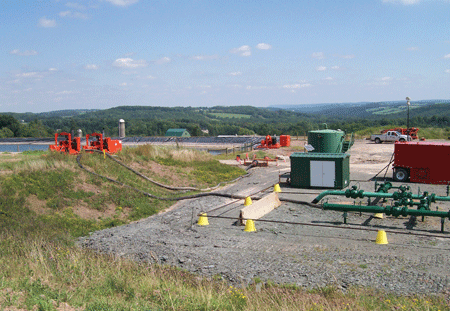
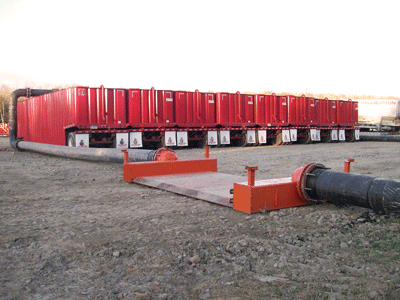