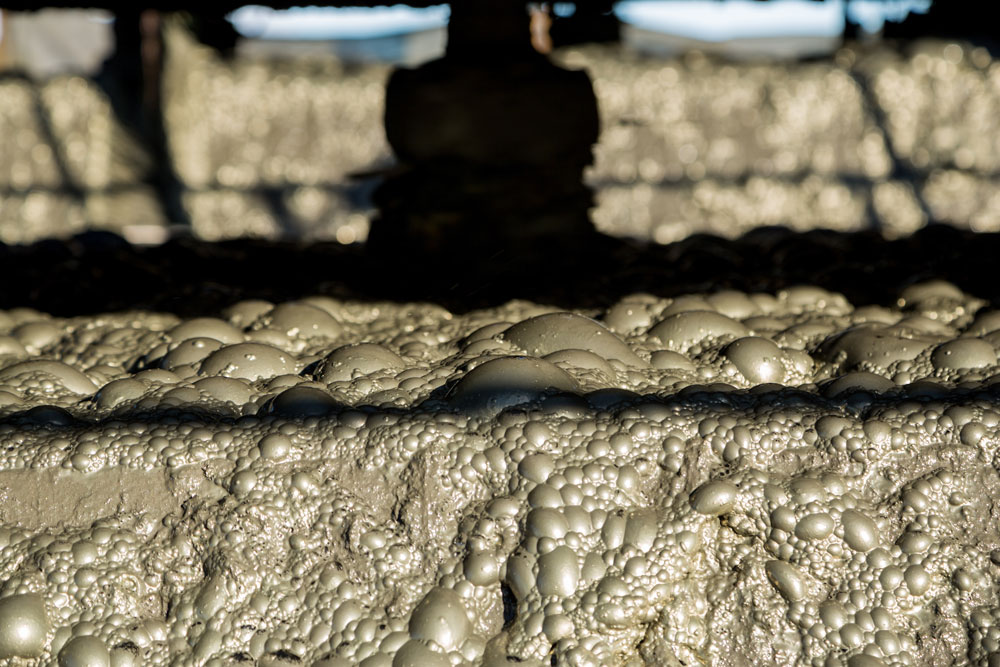
Slurry pumps have been used in many applications such as mining, mineral processing and wastewater services, but they are often overlooked. Some slurry pumps have been wrongly selected or badly operated, and as a result, their performance, reliability and availability have been poor in many plants and facilities.
Performance reduction of the pump and the erosion damage of the wetted components are two important and frequent problems for pumps in slurries (solid-liquid mixtures) services. This article discusses slurry pumps in mining, mineral and wastewater services, focusing on operation, performance, reliability, erosion and wear.
Pump Performance for Slurries
Slurries have been used in many plants, units and processes such as different mining applications, mineral processing, wastewater and others. Centrifugal pumps have long been used in slurry services. The characteristics of a centrifugal pump in a slurry service differ from a centrifugal pump pumping clear water or a clear liquid. When a centrifugal pump is working in a slurry service, the head and efficiency of the pump decrease while the power input to the pump increases. As a rough indication, a slurry pump for commonly used water-based slurries should be assumed to produce a head 10% to 25% lower than one pumping clear water. However, this is just a rough estimate. Indeed, the performance of a centrifugal pump in a slurry service relates to many parameters and factors of the slurry and service such as particle sizes, particle density, concentration of solids and others. It is necessary to know how pump performance will change with each parameter of the slurry to correctly match the pump to the system and manage the operation of the combined system.
Pumps have been heavily affected by solid particles and the nature of slurries. However, piping systems are less affected. The influence of solid particles on the friction head loss of piping and fitting might not be significant. For instance, in turbulent flow in a vertical pipe, the friction head loss is just slightly affected by the presence of solid particles.
Battling Erosion
Erosion and associated wear are major issues in slurry pumps. The important pump wetted components that undergo severe erosive effects are the impeller and casing. Proper studies, parametric analyses and provisions are needed to lower the wear rates. If wear cannot be prevented, the wear pattern along the pump casing wall, impeller and other pump components should be as uniform as possible to avoid localized wear and failure. With increased casing width, wear rates are found to decrease. Many slurry pumps have used internal liners for casing to reduce the wear and damages due to erosion. Some other slurry pumps have been fabricated from hard, anti-erosion materials to battle the erosion and associated wear.
Erosion-Resistance Alloys
There have been many hard and erosion-resistance alloys introduced and applied for slurry pumps (particularly wetted parts). For instance, in abrasive slurry applications, hard cast-iron alloys, usually chromium-nickel alloys, have been used for the wetted components. Due to the difficulty in repairing such hard alloy materials, a local damaged area could render an otherwise serviceable component to be rejected. This leads to frequent replacement of spare parts. Each time a part is to be replaced, there must be a complete shutdown of the slurry pump, which can cause operational losses. If you are considering the useful life of pump components, the cost of repairing and replacing worn-out parts and the associated unscheduled downtime, erosive wear is an extremely important topic.
The pump casing is a heavy and expensive component, and its fabrication is also complex. It is usually the costliest wearing component of the pump. The second key component is the impeller, and an impeller can be more affected by erosion than the casing. However, it can be replaced relatively easily.
Two Mechanisms: Particle Impact & Sliding
Erosion in slurry pumps mainly occurs due to two mechanisms: particle impact and sliding (scouring) action. In dilute slurries, erosion is likely due to particle impact. Dilute slurries have been used in many applications and services, and erosion has been commonly reported. In these situations, the absence of a protective sliding bed combined with appreciable deviations in the trajectories of the particles from the streamlines facilitates wear by particle impact. This is often known as impact wear. Particle impact could also be directional or random due to turbulence of the slurry flow.
Erosion vs. Operation
The operation of slurry pumps needs great care, or it will likely have erosive wear. This wear generally occurs when the pump is not operated at the best efficiency point (BEP). The wear increases with operation at the left or right side of BEP. In other words, wear rates and damages are higher for slurry pumps when they are operated far from BEP.
More intensive wear has been reported in centrifugal pumps. Particle trajectories can be used to obtain the areas of particle impact on a pump impeller, pump casing and other pump components. This data can be used to predict wear rates. The particle concentration at the pump inlet provided a weighting that could be used to approximate the number of particles attributed to each trajectory. The erosion can then be estimated based on the velocity and impact angle of the particles. For instance, for many centrifugal pumps, maximum wear has been near the leading edge on the pressure side and the back shroud in the eye of the impeller.