The most obvious positive manifestation of the ongoing oil and natural gas production boom in the U.S. can be seen at gas stations across the nation. At the end of January 2014, the average price nationwide for a gallon of gasoline was $3.28. One year later, the price for a gallon of gas had dropped to $2.04. While the American consumer is the most obvious beneficiary of the nation’s historically high crude oil production, companies that provide equipment for use in oilfield exploration, production, transport and storage operations are also reaping the benefits. Specifically, increased production in prominent shale fields—including the Bakken in North Dakota, Eagle Ford in Texas, Niobrara in Colorado, and Marcellus and Utica in New York, Ohio, West Virginia and Pennsylvania—has increased the demand for gathering, transport and terminal systems that can store raw crude oil and natural gas until it can be shipped via truck, train or pipeline for refinement and consumption.
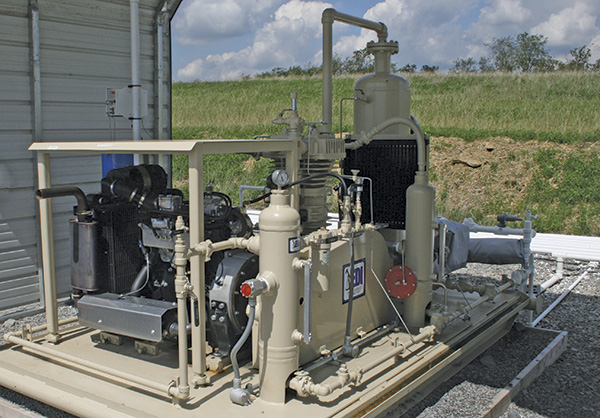
The Challenge
The amount of vapors that are a byproduct of oilfield production activities will continue to increase. Additionally, regulatory agencies will monitor the levels of vapors emitted into the atmosphere and whether or not they can be harmful. Many oilfield vapors—compounds such as benzene, toluene, ethyl-benzene and xylene—have been classified as hazardous air pollutants (HAPs) or volatile organic compounds (VOCs) by the U.S. Environmental Protection Agency (EPA). As a result, operators of oilfield storage facilities must closely monitor the amount of vapors emitted at their sites (if any) and meet the emission thresholds of the Title V Operating Permit Program of the Clean Air Act, enacted in 1990. According to Title V, regulated pollutant thresholds for stationary sources include 100 tons per year (tpy) for criteria pollutants, and from 10 tpy per year for one HAP or 25 tpy for multiple HAPs.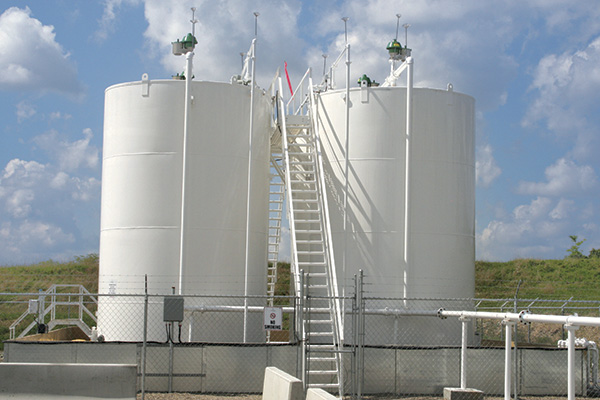
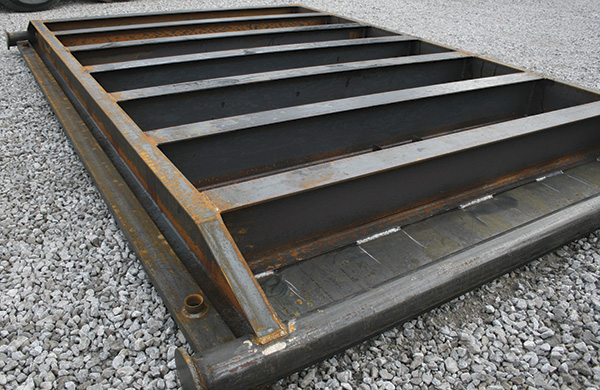
The Solution
To optimize operational performance and production while reducing costly downtime and maintenance, the VRU base and skid assembly must be installed correctly.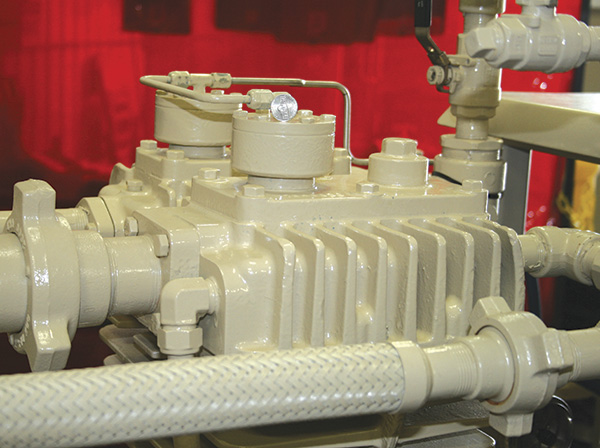
- The compressor should be anchored to a baseplate (or skid) that is at least four times the compressor’s weight.
- The baseplate with the compressor and other VRU components should be bolted to a concrete slab or pad.
- The concrete slab or pad should be placed on a level surface.
- The pad should be prepared and graded, if necessary.
- The baseplate skid should never be installed on non-compacted soil.
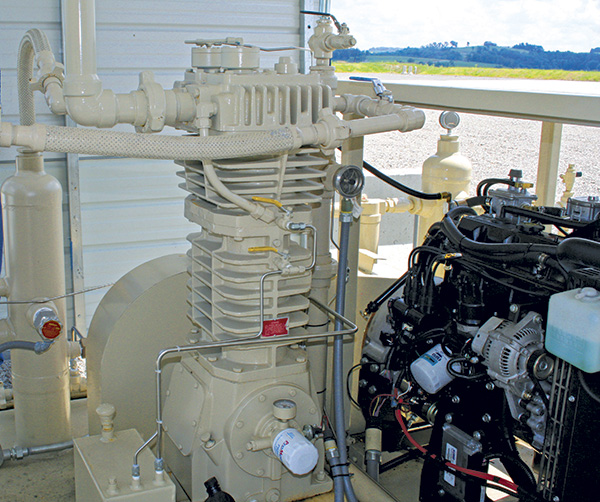