These systems prevent a variety of possible expenses and health dangers.
ARO
09/01/2016
Today’s process industries use powders in a myriad of applications. While many processes employ similar operations to convert raw materials into finished products, the complexities of handling and transferring powders have earned this material category a unique reputation among process engineers and others involved in designing and operating material-transfer systems. From challenging dry bulk materials used in plastics manufacturing processes to fragile tablet granulations and active pharmaceutical ingredients (APIs), each application presents its own distinct set of requirements that make powder handling a critical aspect of process manufacturing. Efficiently containing fine powders, particles, tablets and granules is critical.
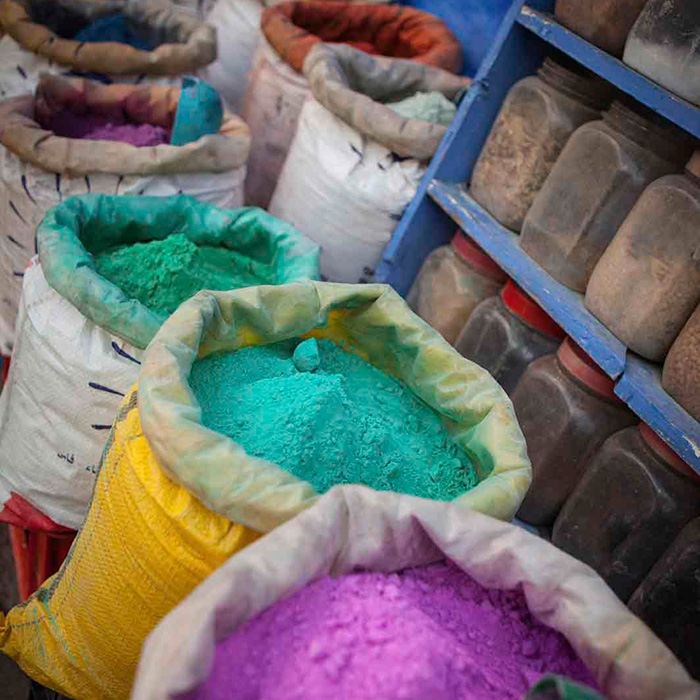
Proactive Approach to Safety
In today’s competitive and highly regulated market, operator ergonomics and worker safety are a priority. Processes involving the handling and transfer of potentially hazardous materials inherently introduce increased safety risks. Transferring powder from one container to another, whether by pouring or scooping, can release plumes of airborne dust that pose significant hazards when transporting some materials, such as starch or activated carbon. Even inert powders, when inhaled over time, can cause lung damage. Active ingredients can cause lung, skin and eye irritation or damage, or trigger allergic reactions. Whether regulated or not, companies that transfer bulk powders from drums or containers should ensure that their processes meet basic environmental and worker safety requirements. Pharmaceutical companies and other regulated manufacturers are obliged to meet additional protocol requirements as part of Current Good Manufacturing Practice (CGMP). Environmental safety hazards should not be overlooked. Any airborne flammable dust in sufficient concentrations can explode. Combustible dust on the ground can become airborne and propagate an explosion. Such an event can occur with vegetable and organic materials as well as with metal and other oxidizable dusts.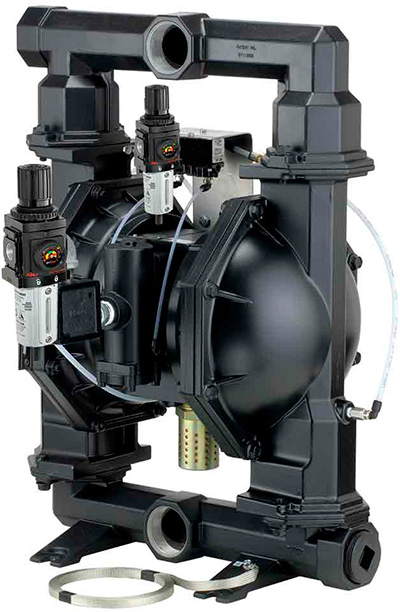
Transfer Performance
Variables such as fluidization, transfer capacity and pump reliability can either positively or negatively affect batch and overall production times. To address these issues, one powder-transfer system features regulated aeration ports for optimum powder aeration and diffusion, as well as an integrated delay timer to increase system efficiency, making this pump a good choice for dusty or sticky powders. The system is also outfitted with a stall-free major air valve and a patented four-way air induction system that controls the amount of air or other inert gases required for operating, resulting in substantial cost and energy savings while eliminating powder pack-out at startup. Additionally, air-operated transfer systems require less manpower compared with manual transfer processes, allowing workers to focus on higher-value activities. Today’s powder-handling facilities must be able to quickly adapt to market demands, with lean production units that can accommodate fast process changes based on mobile or modular technologies. This particular system offers flexible installation options and can be trolley-mounted or installed on existing process equipment while being easy to service.Pump Design & Equipment Life
The ability to keep a vessel closed while introducing powder into the process is considered a best practice for almost all applications. Pneumatic powder-transfer systems virtually eliminate the need to constantly open storage or processing tank manways, greatly reducing the risk of damage and deterioration. Air-operated diaphragm pumps are also optimized for serviceability because they are easier to clean and maintain. This system offers a closed system design that eliminates exterior contaminants and substantially reduces equipment and facility cleanup, which keeps operations moving. Available in stainless steel and aluminum construction, these pumps are self-priming and can run dry or against a closed discharge without the risk of damage or heat buildup. With few moving parts and the ability to run without electrical power, the system’s pump can be ideal for various powder-transfer applications including carbon black, expanded mica, silicones, acrylic resins and pharmaceuticals.Other Factors
For many manufacturers, staying competitive in today’s global market is not possible without the safe, efficient and hygienic transportation of bulk powder ingredients. Numerous quality advantages across multiple phases of production can be realized with contained powder-transfer technologies and processes—a topic that becomes even more important in applications where product integrity is critical. Closed transfer systems minimize the potential for environmental and material contamination that could otherwise jeopardize the purity of an entire batch, resulting in lost production time, product losses, wasted raw materials and significant cost. Additional benefits include increased process repeatability by minimizing opportunities for human error and associated rework. Flow characteristics and pump construction factor into product quality. Features such as a smooth flow path and integrated fluidization capabilities minimize the shear rate and any potential for product damage during pumping. This examined system is constructed using non-reactive, additive or absorptive components to ensure safety, integrity or quality of the end user’s product while maintaining the pump’s reliability. These systems are also designed with removable fluid caps to offer easy access to the fluid chamber for servicing, cleaning or diaphragm replacement without the need for tools. As manufacturers continue to implement new methods and processes to meet production goals while spending less, process engineers must make intelligent decisions concerning powder handling. A lower initial investment does not always mean improved operating costs. Poorly constructed or unreliable pumps can increase downtime and power consumption, impact revenue and significantly add to maintenance costs, while overinvesting in large complex systems may be unnecessary for many applications. When considering alternatives, engineers and others must ultimately make decisions based on the required needs of the application, operational requirements and total cost of ownership. Compact and portable, some pumps can be easily introduced to existing equipment configurations without the need for modification. Certain powder pumps offer additional benefits including material recovery. Transfer efficiency metrics involving the use of mechanical systems can run as low as 40 percent. For example, some systems handling a load of 200 pounds of bulk powder may transfer 80 to 90 pounds before encountering dust-over incidents that result in frequent shutdowns and time-consuming cleanup. Closed powder transfer systems offer safe, effective and clean transfer with virtually no scrap, resulting in less cleanup and less manpower for system maintenance. In some cases, moving to a closed powder-handling system can also lower the costs associated with the use of personal protective equipment required with open systems.Benefits of Air-Operated Powder Transfer Systems
- Self-priming from any start
- Runs dry without damage
- Oil-free design
- No electrical hazards
- Safe for use in hazardous and explosive environments (ATEX certified)
- Quiet, steady discharge
- Pumps at high temperatures
- Easy to operate
- Quick assembly/disassembly
- Low maintenance – easier to clean than mechanical systems
- Pumps a wide variety of powders and other materials (1,000-plus materials tested)
- Safely transfers carcinogens, oxygen, or skin-sensitive and explosive powders
- Suitable for transfer of raw, intermediate or finished products
- Considerable reduction or elimination of operator exposure
- Considerable reduction in transfer times and manpower
- Compact and portable for maximum flexibility
- Optimized aeration and reduced batch time through integrated fluidization
- No additional handling equipment