These devices can detect problems and provide information needed to improve efficiency and save money.
Endress+Hauser
08/07/2017
Companies incur thousands, if not millions, of dollars in maintenance costs to keep their pumping systems in good health. Predictive maintenance is one of the best ways to cut pump operating costs. One effective predictive maintenance technique uses an electronic differential pressure transmitter to not only monitor instantaneous pump performance, but also to identify issues related to pump health and efficiency.
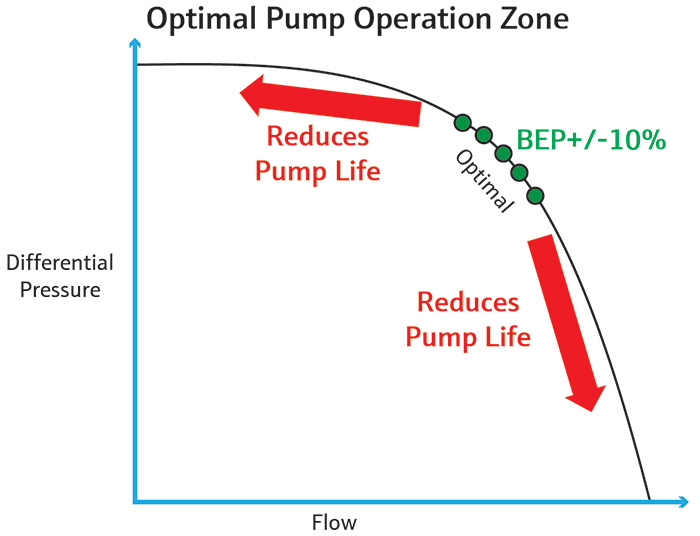
Monitoring Differential Pressure
All pumps perform best when they are at, or very close to, their best efficiency point (BEP) (see Figure 1). The BEP is defined by the manufacturer on its pump curve and is typically 70 to 85 percent of the shut-off head or maximum differential pressure between the suction and discharge. Operating at the BEP is the single most important aspect for prolonging pump life and cutting maintenance time and costs. An electronic differential pressure (EdP) transmitter is well suited for monitoring the performance of a pump in applications where continuous operation is critical, such as cooling tower systems or aeration pumps in wastewater treatment.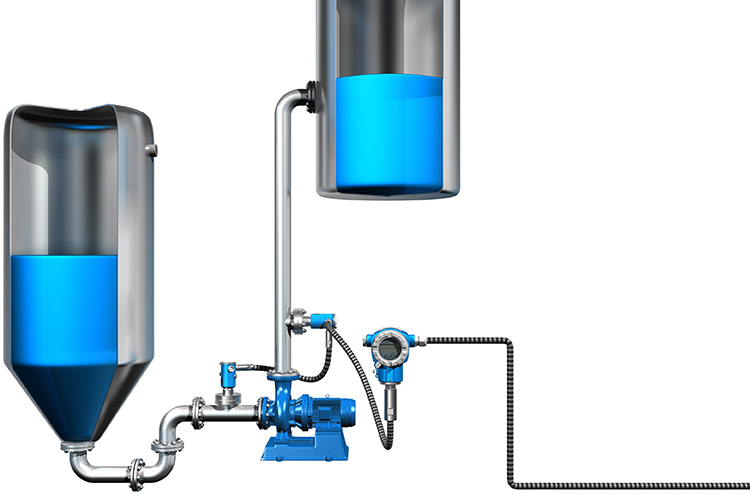
Setting the Right Flow Rate
Incorrect flow rate settings are one of the typical causes of inefficient pump operation. Following is an example of how to use the EdP to set the right flow rate. For a given pump curve, first note: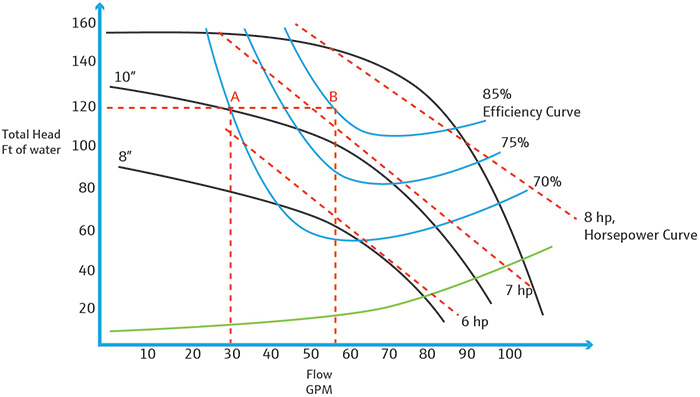
- impeller size
- rated horsepower
- impeller speed
- expected flow at BEP
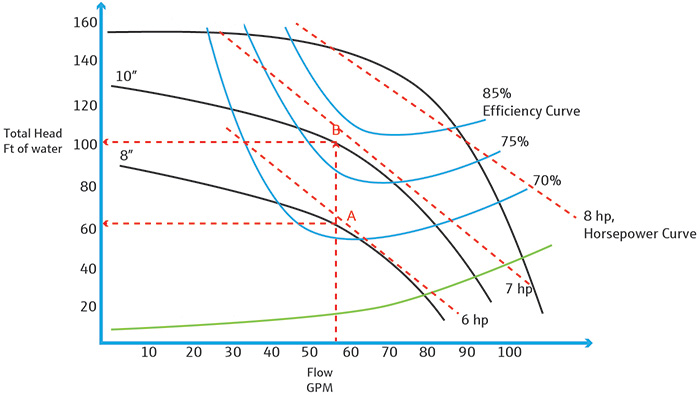
Monitoring Total Head
Assume 55 gpm is the operating flow rate for a 6 HP pump with an 8-inch impeller. The expected intersection on the performance curve for this pump would be point A (see Figure 3). The corresponding expected total head on the Y-axis would be 65 feet.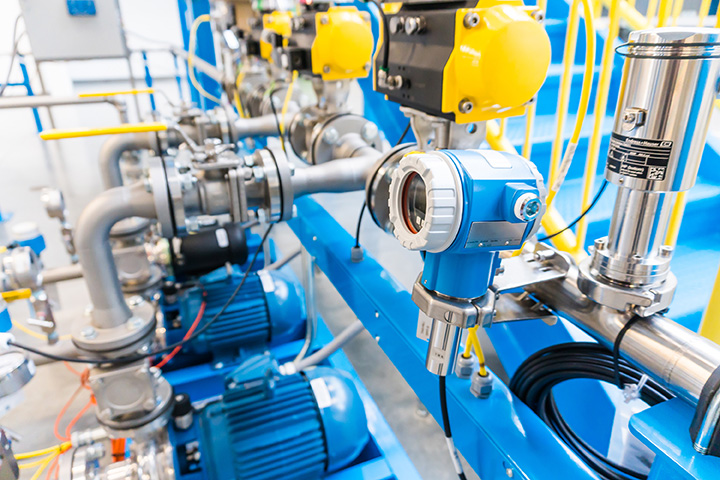
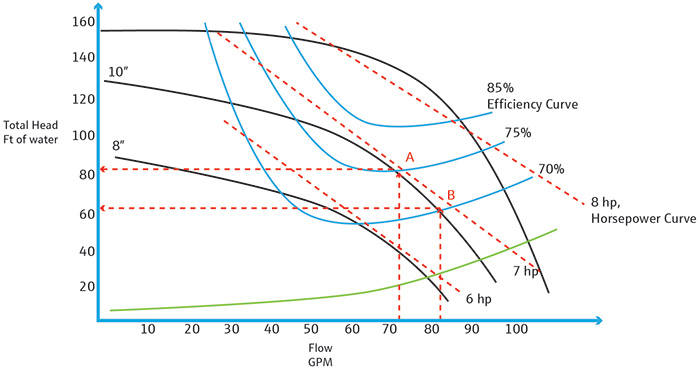