This discussion topic is primarily directed at the end user/owner-operator. However, engineering, procurement and consulting firms may find the topic of interest. Let me begin by asking a question that I believe most everyone can relate to in purchasing a car. Have you walked into a car dealership and announced to the salesperson that you want to purchase a new car and to please select one for me? I think not. We all have our preferences. So why would we look at pump system specifications any different? For as long as I have been in the industry, project specifications have been left to the engineering/consulting firms. I say this with some degree of confidence having worked for various mechanical seal, pump and motor original equipment manufacturers (OEM) as well as a large end user. Yes, some end users prepare a “general specification” as a guideline for the engineering firms. However, this does not provide the critical information necessary to meet today’s needs. In the last 15-plus years, there has been an increasing focus on energy efficiency/reduction and sustainable growth. I suspect you are all familiar with the Energy Independence Security Act specific to induction motors as well as the pending Department of Energy (DOE) ruling for clean water rotodynamic pumps (compliance required on January 27, 2020). The ruling states that certain types of clean water pumps sold in the U.S. market will need to meet minimum efficiency standards. This ruling will include:
- clean water pumps
- BEP pump power input: 1 to 200 horsepower (hp)
- BEP rate of flow: 25 gallons per minute (gpm) or greater
- BEP head: 459 feet (ft) or less
- temperature: 14 to 248 F
- nominal speeds (RPM): 1,800 and 3,600 rpm
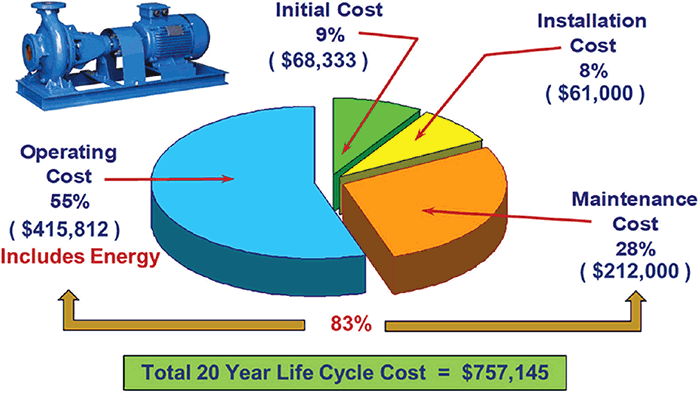
No System Standards
We have another interesting dilemma. With few exceptions, there are no standards to guide pump system design. Engineering contractors and owner/operators can choose (or ignore) how to calculate system hydraulics. Specified pump operating points are not subject to standards. We have many pump standards, American Petroleum Institute (API) and Hydraulic Institute (HI) for example as well as legislation from the federal government (motors and pumps). HI/Pump Systems Matter has developed numerous webinars and workshops directed at the end user/owner-operator to assist in “optimizing” their existing pumping systems. Why? Lack of a system standard resulting in excess energy consumption and costly downtime due—in most cases—to oversized or incorrectly specified pumps. To summarize the current situation:- DOE is regulating motor efficiency with pump efficiency legislation pending.
- 83 percent of the life cycle cost of a pumping is operating (includes energy) and maintenance cost.
- We have no pumping system standards, and oversized or incorrectly specified pumps.
- A third party is specifying systems.
- Projects are typically first cost driven.