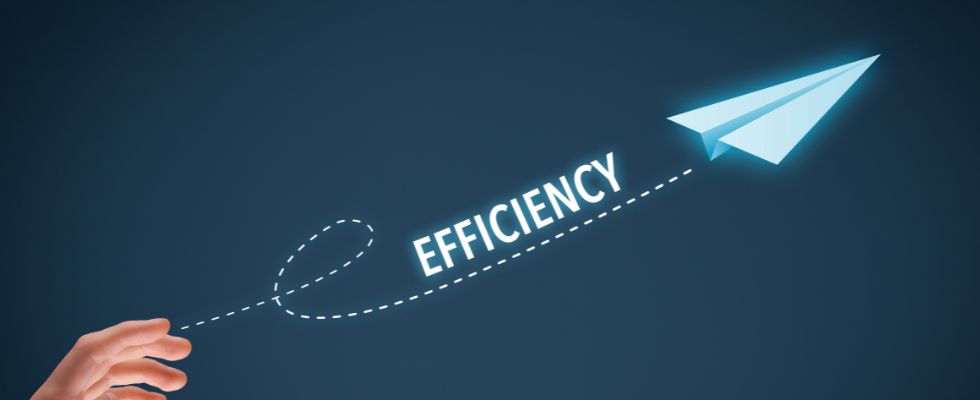
Cavitation in pumps is an all too common, detrimental condition often found in centrifugal pump installations. Cavitation can reduce pump efficiency, cause vibration and noise and lead to significant damage to a pump’s impeller, casing, shaft and other internal components. The cavitation phenomenon occurs when the pressure of the fluid in the pump falls below the vapor pressure, causing vapor bubbles to form at low-pressure pockets. These vapor bubbles violently collapse or “implode” as they enter higher pressure areas. This can lead to mechanical damage to pump internals, provide weak points susceptible to erosion and corrosion and impair pump performance.
Understanding and implementing strategies to mitigate cavitation is crucial for maintaining the operational integrity and longevity of centrifugal pumps.
Types of Cavitation in Centrifugal Pumps
To reduce or prevent cavitation in a centrifugal pump, it is important to understand the different types of cavitation that may occur. These include:
Vaporization: Also known as “classic cavitation” or “inadequate net positive suction head available (NPSHa) cavitation,” this is the most common type of cavitation. It occurs when a centrifugal pump increases the velocity of a fluid as it passes through the eye of the impeller. The increased velocity corresponds to a pressure reduction of the fluid. This pressure reduction may cause some of the fluid to boil (vaporize) and create tiny shock waves as the vapor bubbles collapse.
Turbulence: Parts of a piping system such as elbows, valves, filters or strainers may not be suitable for the amount or nature of liquid being pumped. This can create vortices, turbulent flow and pressure differences throughout the liquid. When present at a pump inlet, these phenomena can erode pump internals directly or result in vaporization of the fluid.
Vane syndrome: Also known as “vane passing syndrome,” this type of cavitation occurs when an impeller is too large in diameter or the housing internal coating is too thick. Either one or both of these scenarios may reduce the space within the housing to below an acceptable level. The reduced clearance in the housing results in increased fluid velocity, leading to lower pressure. The lower pressure may cause the fluid to vaporize, creating cavitation bubbles.
Internal recirculation: This occurs when a pump cannot discharge fluid at the required rate, causing some or all of the fluid to recirculate around the impeller. The recirculating fluid passes through low and high pressure zones, resulting in heat generation, high velocity and the formation of vaporization bubbles. A common cause of internal recirculation is running the pump while a discharge valve is closed.
Air aspiration cavitation: Air may be sucked into a pump through failing valves or loose joints. Once inside, the air flows along with the fluid. The movement of the fluid and air may result in the formation of air bubbles, which “explode” when exposed to increased pressure by the pump impeller.
Factors Contributing to Cavitation
NPSH, NPSHa and NPSHr
NPSH is a critical factor in preventing cavitation in centrifugal pumps. NPSH is the difference between the actual suction pressure and a fluid’s vapor pressure and is measured at the pump inlet. The NPSH value needs to be high to prevent fluid from vaporizing within a pump.
NPSHa is the actual NPSH at the pump operating conditions. Net positive suction head required (NPSHr) is the minimum NPSH as specified by the pump manufacturer to avoid cavitation. NPSHa is a function of the suction pipework, pump installation and operating details. NPSHr is a function of the pump design and is established from pump testing. NPSHr represents the head available under test conditions, when the pump head is decreased by 3% as a result of cavitation, caused by decreasing the available suction head. NPSHa should always exceed the NPSHr to avoid cavitation.
Air entrainment and its role in cavitation
Air entrainment occurs when air is introduced into a pump’s suction line, leading to an increased risk of cavitation. This can happen due to improper pump priming, leaks in the suction line, formation of vortices or turbulent flow in the suction pipework. Air in the liquid forms small bubbles which, under the prevailing pressure conditions inside the pump, can contribute to or exacerbate the cavitation process. Reducing air entrainment is crucial in minimizing cavitation risks. This can be achieved by adhering to minimum submergence requirements, ensuring proper sealing of pipe connections, maintaining a positive suction head and avoiding turbulent flow at the pump intake.
Pump and system curve analysis in relation to cavitation risk
Pump and system curve analysis is an essential tool in understanding and mitigating cavitation risks. Intersection between pump and system curves illustrates how the pump will perform in terms of flow rate, head and efficiency at varying system conditions. By analyzing pump and system curves, operators can determine the optimal operating range of the pump, avoiding regions known to provoke cavitation. These include scenarios with very high flow rates or very low suction heads. Special attention should be given to the minimum flow point, as operating below this flow can significantly increase cavitation risks. Proper use of pump curves helps in making decisions about pump selection, operating speeds and the necessary precautions to be taken to minimize cavitation in centrifugal pumps.
Strategies to Reduce Cavitation
Increasing NPSHa to prevent cavitation
Ensuring that NPSHa is greater than NPSHr is essential to avoid cavitation. This can be managed by:
Reducing the pump’s elevation relative to the suction reservoir. The water level in the suction reservoir may be increased, or the pump may be lowered. This serves to increase the NPSH at the pump inlet.
Increasing the diameter of the suction pipework. This results in reduced fluid velocity for a constant flow rate, corresponding to lower suction head loss from pipework and fittings.
Reducing head loss from fittings. Reduce the number of fittings on pump suction lines. Use fittings such as long radius bends, full bore valves and tapered reducers to help lower the suction head loss due to pipe fittings.
Avoiding screens and filters on pump suction lines if at all possible, as they often contribute to cavitation in centrifugal pumps. If this is not possible, ensure screens and filters on pump suction lines are regularly inspected and cleaned.
Cooling the pumped fluid to lower its vapor pressure.
Understanding the NPSH margin for cavitation prevention
The NPSH margin refers to the difference between the NPSHa and the NPSHr. A larger NPSH margin reduces the risk of cavitation, as it provides a safety factor against fluctuations in operational conditions that might reduce the NPSHa below normal operating levels. Factors affecting the NPSH margin include fluid characteristics, pump speed and suction conditions. Engineers must calculate and maximize this margin during the design and operational planning stages to ensure reliable pump performance and minimize the risk of cavitation. Regular monitoring and adjustments based on real-time operating data can help maintain an effective NPSH margin.
Maintaining pump minimum flow rates
Ensuring that centrifugal pumps operate at or above a specified minimum flow rate is essential in mitigating cavitation. Operating a centrifugal pump below its optimum flow range increases the likelihood of creating low-pressure zones that can induce cavitation. Each pump has a pump characteristic curve indicating the minimum flow required to prevent operational issues, including cavitation. Flow control methods such as bypass lines, control valves or variable speed pumping may be used to maintain this minimum flow. This is especially important during startup or shutdown phases, when demand on the pump varies.
Impeller design considerations for minimizing cavitation
The design of the impeller plays a major role in a centrifugal pump’s susceptibility to cavitation. Impellers with fewer, larger blades tend to cause less fluid acceleration, which can decrease cavitation risk. Additionally, impellers designed with a larger inlet diameter or tapered blades can help manage the flow more smoothly, minimizing turbulence and the formation of vapor bubbles. The use of materials resistant to cavitation damage can enhance the longevity of the impeller and pump.
Utilizing anti-cavitation devices
Anti-cavitation devices, such as flow modification attachments or cavitation suppression liners, can be effective in mitigating cavitation. These devices work by controlling the flow dynamics around the impeller, providing a more stable flow and reducing turbulence and low-pressure zones that lead to cavitation. Flow straighteners may be used to reduce the swirl components in a fluid, improving inlet conditions at the pump. Cavitation suppression liners attempt to break apart vapor bubbles before they implode, thereby safeguarding the impeller and the pump casing from damage.
Importance of proper pump sizing in cavitation prevention
Choosing the correct pump type and specifying the correct size for a particular application is crucial in preventing cavitation. An oversized pump may operate inefficiently at lower flows, leading to increased cavitation risk, whereas an undersized pump might need to work harder to meet flow requirements, also increasing the likelihood of cavitation. Correct pump sizing involves detailed analysis of the maximum, normal and minimum flow requirements, fluid properties and system layout, ensuring the pump operates within its designated operating range. Accurate sizing prevents cavitation and enhances the efficiency and reliability of the pump over its life cycle.
Cavitation in centrifugal pumps compromises efficiency and diminishes its life span through damage to vital components. Implementing the strategies discussed, such as optimizing the pump design and selection, maintaining appropriate flow rates and ensuring adequate NPSH will lead to a significant reduction in cavitation risks. Regular monitoring and maintenance ensures pumps will operate under optimal conditions, thus fostering longevity and reliability in various applications. By taking proactive steps, facilities can enhance performance and avoid costly damage and pitfalls associated with cavitation.