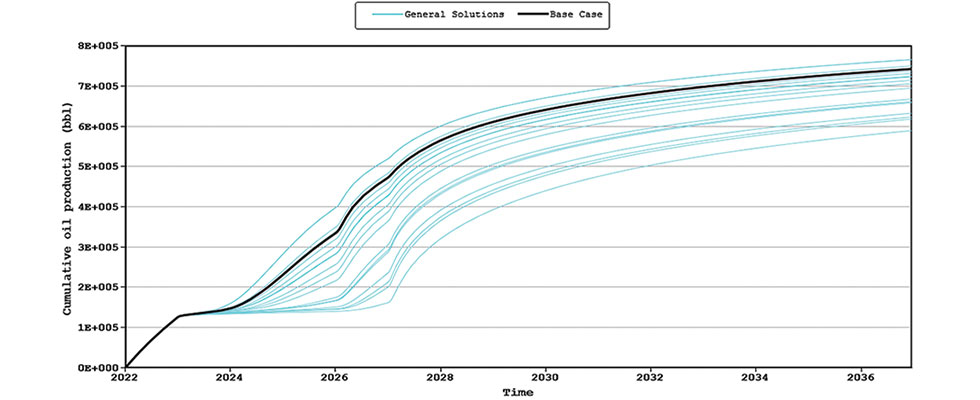
Enhanced oil recovery (EOR) is a tertiary method of extracting oil from a well after primary production declines due to a drop in natural reservoir pressure and secondary processes, such as waterflooding or gas injection, becoming unsustainable. Since there can be at least 50% of the original oil in place (OOIP) after primary and secondary processes, EOR takes on added importance. Three types of EOR include gas injection, steam injection and chemical injection.
Polymer flooding is a mature technology and the dominant form of chemical EOR, but many industry insiders know the intended viscosity of a polymer solution and the actual viscosity injected in the reservoir can vary. This is primarily due to shear effects (polymer degradation) in equipment and piping systems, typically 10% to 15% degradation in oilfield projects.1
Mechanical degradation can result in viscosity loss due to the irreversible scission of polymer macromolecules. It can occur in the injection facilities (turbulent flow) before the polymer solution reaches the formation, or in the near-wellbore area (laminar flow).2 Scissoring occurs when a polymer solution is exposed to high-shear conditions, such as when mixing the polymer solutions or during the conveyance of polymer solution in pumps and chokes.3 This can impact capital and operating expenses. For every 3% shear in the polymer mother solution, approximately 10% extra polymer is used. As the pump is one of the first pieces of equipment the polymer slug encounters, it is one of the first points of shear degradation of the polymer solution.
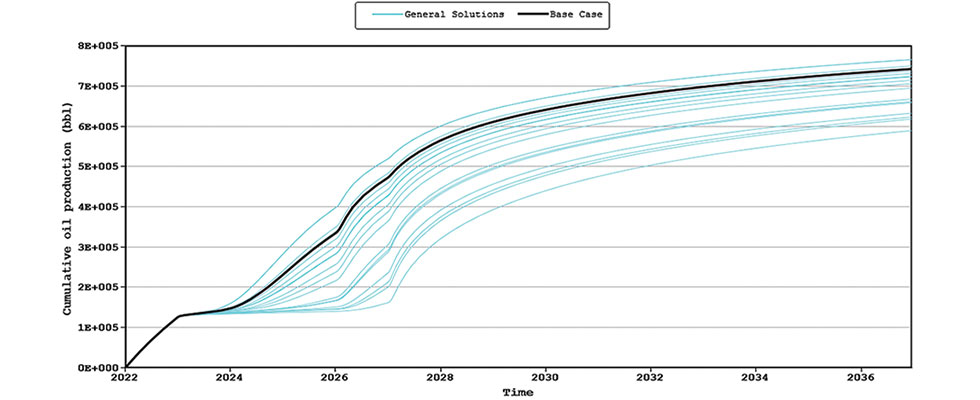
Progressive cavity and triplex plunger pumps are often used for polymer flooding to mitigate degradation. Progressive cavity pumps have seen some use as deliverers of mother solution (viscous, high-concentration polymer solution). However, they have lacked use for pumping downhole due to the operational costs, complexity and rigorous maintenance that requires long periods of downtime.
Triplex plunger pumps are a frequent choice for operators of polymer floods. These pumps see shear degradation values of up to 15% of the solution viscosity.4
An attempted remedy is oversizing the plunger pump and slowing the rotations per minute (rpm), creating a nonoptimized and more expensive solution while still causing turbulent flow and degradation of the polymer solution. Independent testing at the University of Wyoming showed that a positive displacement, hydraulically actuated diaphragm pump with a sealless design reduced polymer degradation to only 1% to 5%, according to Vladimir Alvarado, Ph. D., professor of chemical and biomedical engineering and energy and petroleum engineering at the University of Wyoming.5 Experimental measurements included rheometer measurements, nuclear magnetic resonance (NMR) measurements and dynamic light scattering (quality control checks).
The experimental system and piping did have a nonnegligible impact on polymer solution viscosity reduction, suggesting that polymer degradation through the diaphragm pump is most likely even less than the measured 1% to 5% viscosity reduction.6 Sensitivity analyses were run on a simulation software to see the effects that polymer molecular weight, assigned polymer viscosity and polymer mixing function (polymer viscosity vs. concentration) had on the cumulative oil production on a selected simulation study.
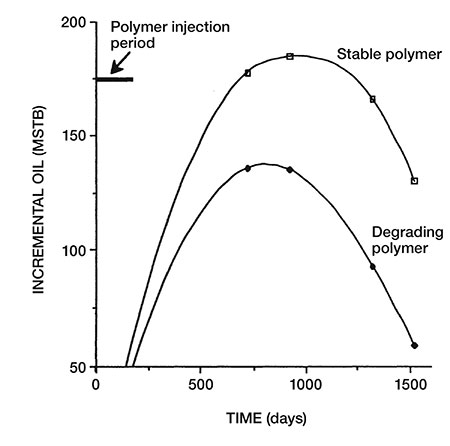
Results showed a decrease of up to 30% in cumulative oil production through varying the three parameters (Image 1), which confirmed the results in Sorbie’s monograph on degrading polymer solutions and their negative effect on cumulative oil production (Image 2).7 This decrease can ultimately determine whether a project is profitable, exemplifying the need for low-shear pumps.
The hydraulically actuated diaphragm pump has a sealless design that separates the hydraulic (power) end from the fluid (process) end. As the drive shaft turns, it actuates connecting rods and converts the rotational motion into linear pumping motion of the plungers.
Each plunger displaces a controlled volume of oil synchronized to the diaphragm by the hydraulic system, retaining the precise balance of oil behind the diaphragm regardless of the pump’s operating conditions. This balances the diaphragm against the fluid being pumped and maintains no more than a 5 pounds per square inch (psi) pressure differential irrespective of the system pressure at which the fluid is being delivered (up to 3,000 psi in the model tested).
Each of the three diaphragms has its own pumping chamber that contains a suction and discharge valve assembly. As the diaphragms move back, fluid enters the pump through a common inlet and passes through the suction valves. On the forward stroke, the diaphragms push the fluid out of the discharge valves and through the manifold’s outlet port. Equally spaced from one another, the diaphragms operate sequentially to provide consistent, low-pulse flow resulting in the minimization of shear.
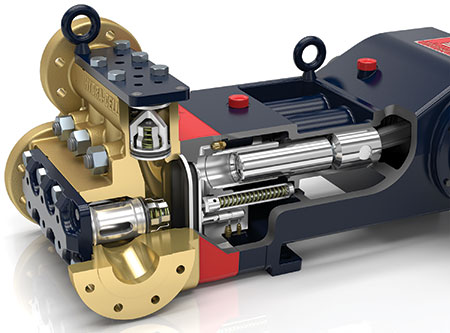
With the typical lifetime from reservoir screening to pilot EOR projects being two to four years, operators cannot afford operational inefficiencies and increased capital expenditure (capex) operating expenditure (opex) in their projects and must reliably inject what was designed. A primary cost driver for larger-scale projects is the price of polymer, and degraded polymer affects overall recovery and reserves.
With chemical EOR costs typically being reported at an inclusive cost per incremental barrel of oil basis, long-term consequences of capex decisions are unknowingly funneled into rising opex costs. For example, if a high-shear triplex pump were purchased due to lower upfront costs, capex would show up favorably on the balance sheet; however, over time, the opex costs would rise as more polymer is purchased to overcome the additional degradation and reduced mobility control of the polymer solution. Low shear hydraulically actuated positive displacement diaphragm pumps can result in monetary savings through lower polymer utilization and higher cumulative production.8
References
Vladimir Alvarado. Hydra-Cell Diaphragm Pump Technology for Minimizing Shear Effects in EOR Polymer Solutions, Phase I. Wanner Engineering, Inc., Page 5, 2022.
D. Rousseau, I. Henaut, A. Dupas, P. Poulain, R. Tabary, J.F. Argillier, and T. Aubry. Impact of Polymer Mechanical Degradation on Shear and Extensional Viscosities. Saint Petersburg, Russia, April 2013.
W. Littmann. Polymer flooding. Number 24 in Developments in petroleum science. Elsevier; Distributors for the US and Canada, Elsevier Science Pub. Co, Amsterdam; New York: New York, NY, USA, 1988.
Wang Demin, Jiang Youlin, Wang Yan, Gong Xiaohong, and Wang Gang. Viscous-Elastic Polymer Fluids Rheology and Its Effect Upon Production Equipment. Page 8, 2004.
Op. cit., Alvarado.
Op. cit., Alvarado.
K. S. Sorbie. Polymer-Improved Oil Recovery. Springer Netherlands, Dordrecht, 1991.
E.P. Egenolf. Hydra-Cell Diaphragm Pump Technology for Minimizing Shear Effects in EOR Polymer Solutions, Phase II. Wanner Engineering, Inc., Page 5, 2022.