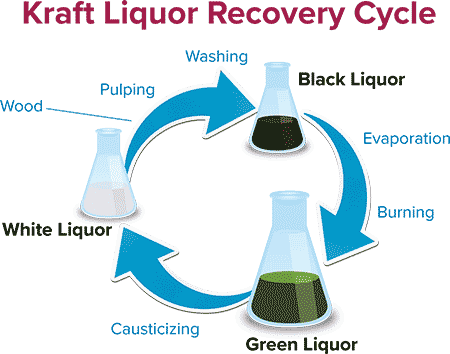
Kraft papermaking involves a complex cycle of transforming wood chips into pulp and paper. Central to this process are three critical chemical stages: green liquor, white liquor and black liquor. Each stage plays a pivotal role in the efficiency and quality of the final product, making it essential to optimize every step.
The Green Liquor Process
The process begins with green liquor, produced from smelt mixed with water and sent to the slaker. Smelt, a molten inorganic chemical resulting from burning black liquor, is drained from the recovery boiler through smelt spouts into the dissolving tank, where it mixes with water to form green liquor. This slurry undergoes causticizing, resulting in sodium hydroxide (NaOH), or white liquor, and calcium carbonate (CaCO3), also known as lime mud. The white liquor is then used to pulp wood chips, which are processed into paper. The waste from this step, black liquor, is sent to the recovery boiler. Here, it generates heat from the combustion of organic chemicals (lignin) for steam and releases inorganic chemicals, forming a smelt that, when mixed with water, becomes green liquor again, completing the cycle.
Why Temperature Control Matters
The efficiency of green liquor feeding into the slaker depends on precise temperature management. Ideally, feed temperatures should range between 180 F and 200 F (82 C to 93 C). Maintaining this range is critical for several reasons:
- Sodium hydroxide conversion: Efficient conversion reduces the need for additional make-up sodium hydroxide, cutting costs.
- Chemical cycle heat: Adequate temperatures ensure optimal white liquor temperatures, affecting the wood chip cooking process. Inefficient cooking demands more steam, increasing energy costs.
- Temperature drops: If green liquor temperatures fall to 160-165 F (71-74 C), the mill must rely solely on the exothermic reaction in the slaker, which is less efficient.
- Fresh lime requirement: Cold green liquor necessitates more fresh lime in the slaker, raising costs due to the high price of fresh lime. Inefficient conversion to caustic soda results in increased sodium hydroxide makeup.
Interruptions in the green liquor conversion process can increase chemical usage and costs, making precise heating crucial for efficiency and cost control.
DSI Heaters
Energy transfer
DSI heaters achieve high energy transfer efficiency by directly injecting steam into the green liquor, ensuring that all the thermal energy from the steam is utilized in heating the liquor. This direct contact method avoids the inefficiencies associated with indirect heat exchangers, where heat transfer occurs across surfaces that can become fouled or corroded over time.
Maintenance and downtime
Traditional heat exchangers and spargers are prone to scaling, fouling and corrosion, necessitating frequent maintenance and leading to downtime. DSI heaters eliminate these issues by injecting steam directly into the process stream, preventing scale buildup and fouling on heat transfer surfaces. This leads to lower maintenance costs and increased operational uptime.
Temperature control
DSI heaters, particularly those with internal modulation, provide precise and reliable temperature control by managing steam flow directly within the heater, thereby eliminating the need for external steam control valves. This internal modulation maintains a high-pressure differential that promotes efficient mixing and heating, reducing fouling and ensuring consistent performance. By controlling steam flow through a stem-plug and nozzle assembly inside the heater, these devices can vary steam mass flow by adjusting the nozzle’s steam discharge area. This approach maintains a linear relationship between nozzle open area and steam mass flow without altering steam pressure, requiring a significant pressure differential to achieve choked steam flow through the nozzle at velocities up to 1,500 feet/second (460 meters/second).
Response and stability
The high steam velocity facilitates turbulent mixing with the process stream (green liquor), ensuring uniform heating and preventing fouling buildup in the heater. An inline, internally modulated DSI heater stands out due to its rapid response and effective temperature control capabilities for maintaining precise green liquor feed temperatures without risk of boil-over. This fast response to temperature changes enhances the stability and reliability of the heating process, which is critical for maintaining consistent production quality.
Cost efficiency
DSI heaters contribute to cost efficiency in several ways. They lower operational expenses by reducing maintenance needs and downtime. Additionally, their high energy transfer efficiency means less steam is required to achieve the desired heating, reducing energy costs. Over time, these savings can be substantial, making DSI heaters a financially prudent choice for kraft paper mills.
Environmental benefits
DSI heaters also offer environmental benefits by optimizing the heating process and reducing energy consumption. Lower energy use translates to reduced greenhouse gas emissions, supporting sustainability goals. Additionally, the reduced need for chemical cleaning agents to address fouling and scaling in traditional systems minimizes the environmental impact of maintenance activities.
For paper mills, optimizing the green liquor process is essential to improving efficiency and reducing costs. Precise temperature control is at the heart of this optimization. By considering the implementation of an inline, internally modulated direct steam injection heater, users may achieve more precise control, enhance conversion efficiency and ultimately boost their mill’s overall productivity and cost-effectiveness.