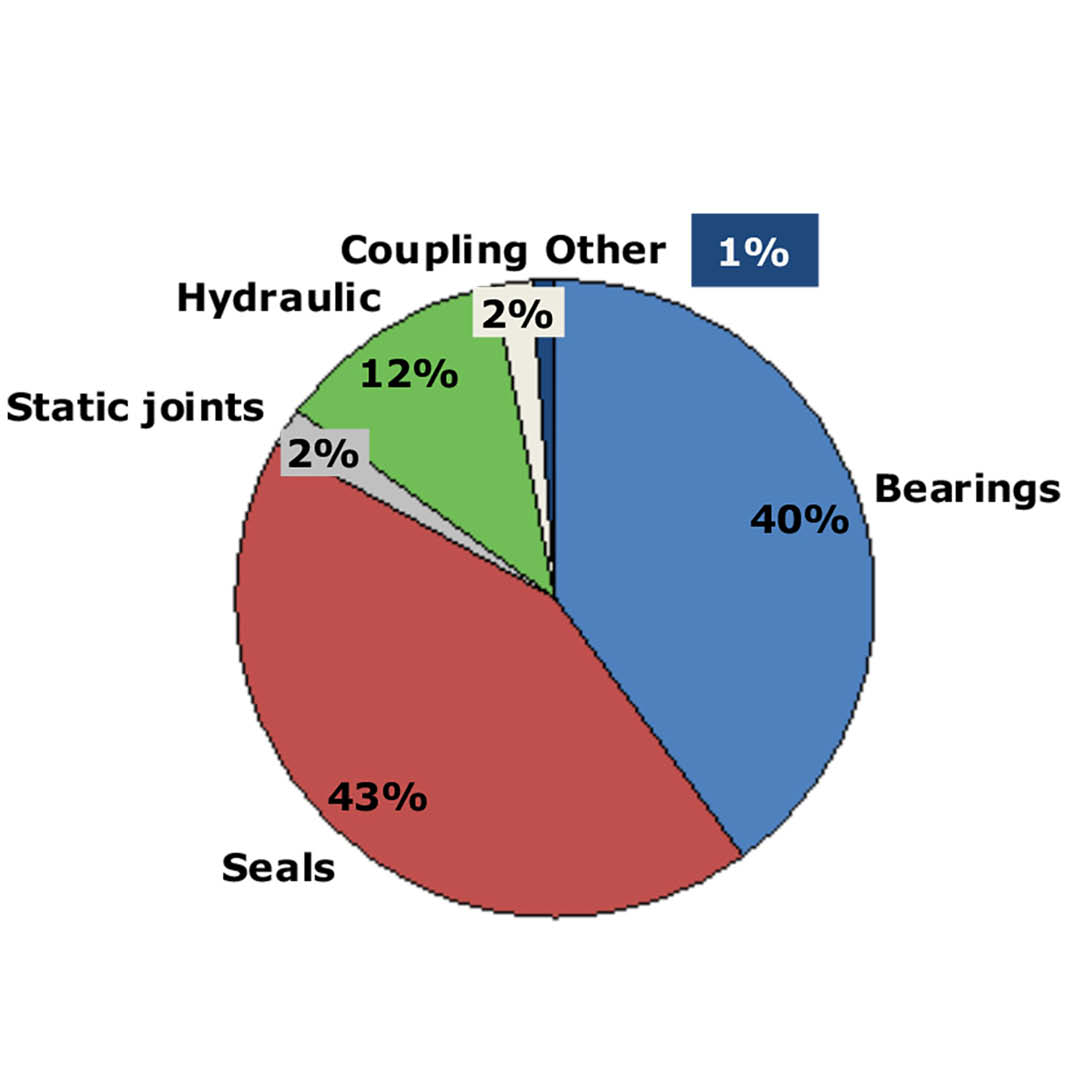
Pie charts (Image 1) are popular because they convey much information at a single glance. The relative failure cause distribution of important machine components can be gleaned from such charts. As just one example, valve replacements topped the list of components in reciprocating compressors for decades, but today’s more efficient and highly reliable reed valves were not reflected in these charts. Valve issues have an environmental impact and, like mechanical seals, are among the many examples where component unreliability causes safety, profitability and serious environmental concerns. The work described in this article offers important quantitative data to that effect.
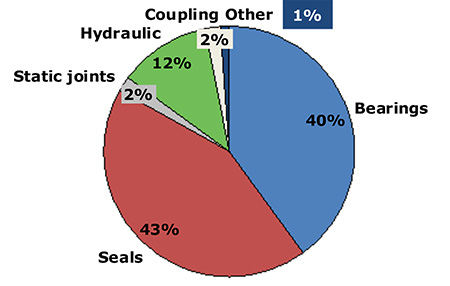
Looking at older pie charts for process pumps, we usually find that mechanical seals fail more often than rolling element bearings. Yet, seal failures topping bearing distress events might only be valid at
Plant A. Plant B might have had the opposite experience because its mechanical seals were matched with carefully selected flush plans that kept seal face temperatures in check. Chances are the seal supplier at Plant B receives bonus payments for achieving long seal life, while Plant A teamed up with a vendor who supplied lots of inexpensive mechanical seals and paid little attention to the best available flush systems. Consequently, Plant B’s pie chart would be made up of slices that differed from the ones at Plant A.
Best-in-class facilities excel by skillfully using reliability engineering (RE), an experience-based applied science that extends equipment safety and operating time before downtime becomes necessary for maintenance or repair. At RE facilities, engineers investigate opportunities to upgrade vulnerable components, even in modern machines. This article briefly touches on the topic and delves into weighty reasons why industry leaders now see fit to link increased equipment reliability and successful efforts to slow down—and hopefully even stop—global warming.
Two guiding principles of industry leaders make sense:
- A severely compromised environment kills people and economies.
- Clean air and healthy equipment have no disadvantages.
Accordingly, competent professionals take pleasure in reflecting on the significant progress that has recently been made in Europe and find it helpful to review well-quantified data released by a U.K.-based industry-leading seal manufacturer in 2021. I firmly believe that its actions are worth imitating, and here is why.
Using low-cost commodity products instead of better engineered mechanical seals has been estimated to increase leakage from individual seals by factors as high as 21. It has been said that failure-prone products benefit a few, whereas engineered products benefit many more people. Prevailing regulatory mandates differ by location and site, and even relatively high emissions are permitted in some jurisdictions. However, common sense tells us that air quality deficiencies cause health issues. Cases of asthma and emphysema will increase and a visit to the pulmonary wing of a large children’s hospital may help overcome indifference.
Why Component Upgrading Is Needed
Experience shows that most of the industry’s process pumps are bought for projects that entrust pump selection to engineering, procurement and construction (EPC) contractors. EPC contracts spell out private sector tasks on large-scale and complex infrastructure projects. Many such projects are funded by narrowly defined budgets, and EPCs take note of perceived savings when two pumps per service are installed. Because one of the two pumps runs, and the second one is a standby or spare, it is reasoned that one of the two will always be available. Reliability is not given much attention unless the owner’s professionals have identified, cost-justified and specified certain mandatory upgraded components.
For example, bearing housing protector seals with axially or diagonally moving O-rings (Image 2) are among several highly recommended upgrades for process pumps. Greatly extended pump life is obtained with lubricant application methods such as pure oil mist. At little incremental cost, oil mist branch lines would feed atomized oil to electric motor bearings, relegating both periodic regreasing and moisture intrusion into standby equipment to the past. United States dollar comparisons showed grease lubrication costing 10 times more than oil mist supplied by a closed system once factors such as bearing replacement, labor for regreasing tasks and expenditures for premium greases were being considered.
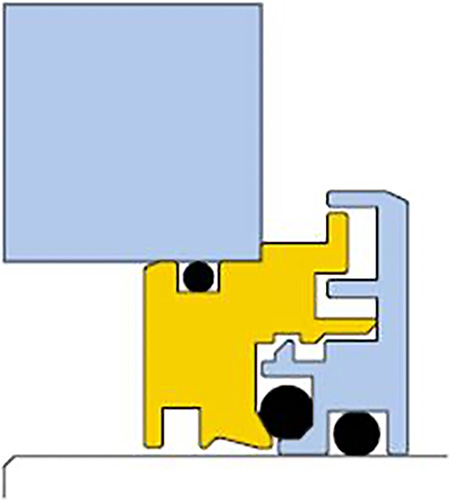
Additionally, fewer pump failures cause fewer fire incidents, thus protecting both physical and environmental assets. These protective measures are now of equal interest to responsibly managed facilities. Verified cost data are both available and compelling.
Examining Global Warming
Global warming is a scientific reality governed by facts that the well-informed will never dispute. Adversely trending warming effects and shifting weather patterns have contributed to catastrophic famines, destruction of forests, huge stresses on sea life, disastrous floods and the loss of human and physical assets. All have been widely observed and reported on by unbiased researchers. Fortunately, the curtailment of carbon dioxide (CO2) emissions by modern industry is possible today, and capitalizing on the opportunity will go a long way toward reducing the destructive action resulting from CO2 freely escaping into the envelope of protective gases surrounding the livable globe. There are numbers to prove it.
The earth was designed with leafy vegetation and oceans that take up CO2 from the atmosphere and absorb around one-third of the CO2 created by fossil fuel burning and deforestation. However, as the concentration increases, acidity also increases, and marine life suffers.
Net zero carbon emissions are feasible but require the cooperation of industry leaders. In this regard, U.K.-based AES Engineering Ltd. stood out when, in 2021, it went beyond net zero. In 2021, its global business activities delivering CO2e (“e” denoting equivalent savings) matched the CO2 absorption of more than 18 million mature trees, according to figures obtained by the British Standards Institution (BSI), one of the world’s leading standards organizations.
Emission Scopes Defined
The industry’s carbon footprint from direct, indirect and supply and value chain emissions can be defined. The relevant coverage is divided into emission scopes. The three scopes are:
- Scope 1: Direct emissions from owned or controlled sources.
- Scope 2: Indirect emissions from the generation of purchased energy.
- Scope 3: Indirect emissions (not included in Scope 2) that occur in the value chain of the reporting company, including both upstream and downstream emissions.
Solid Achievements Verified & Quantified
In what may be a first for a major engineering company, BSI verified that the activities of AES Engineering Ltd. generated CO2e savings of 464,000 tons (of 1,000 kg/2,204 lbs each), resulting in a net benefit of 375,000 tons of CO2e. BSI favorably noted that the Scope 3 emissions in the supply and value chain were just under 90,000 tons of CO2e.
The group’s CO2e saving record is equivalent to offsetting the CO2e emissions resulting from the production of 416,000 tons of cement or 97,000 tons of steel, which is equivalent to preventing the burning of 150,000 tons of coal. To put these figures in perspective, a recently reported carbon capture scheme at an advanced waste incinerator in Oslo/Norway costing (all in equivalent U.S. dollar currency) $1,070 million is expected to save around 400,000 tons of CO2e annually. The U.K. government is currently investing just under $250 million to fund 4,000 zero emission buses that are expected to result in a net reduction of 57,000 tons of CO2e annually. This number equates to only about 15% of the savings resulting from the AES group’s global business activities.
Achieving Scopes 1, 2 and 3 last year was calculated at 94,000 tons of CO2 equivalent (CO2e). In addition to buying green energy, installing solar panels and other environmental investments, the group purchased 5,000 tons of CO2 offsets from “gold standard” schemes, which completely neutralized the impact of the Scope 1 and Scope 2 emissions.
Maintaining a Positive Carbon Balance Sheet
Since the group offers reliability products and services that save energy, water and cut pollution, the impact of its “carbon balance sheet” is strongly positive at 375,000 tons of CO2 saved. In the as-stated case of AES Engineering, BSI’s verified numbers showed that Scope 3 (bad) emissions originating from suppliers of metal, raw materials, equipment bought, etc., were only a fraction of the Scope 3 emissions avoided by the user’s activities.
AES helped its end users reduce their CO2e emissions, and Scopes 1 and 2 were neutralized by buying offsets. The group’s (good) Scope 3 emissions were self-neutralized since the group’s professionals helped avoid more user-generated CO2 than was emitted by the users’ suppliers. Accordingly, the results have gone beyond net zero.
An Important Summary
Seasoned reliability professionals at AES Engineering initially supported the target of getting beyond net zero by 2029. However, they reached this target eight years ahead of schedule thanks to a group-wide effort and its “29by29” pledge to invest $36 million by 2029 in environmentally friendly projects. More than $8,600,000 has been committed already, but AES Engineering intends to keep on going and will continue to support another highly significant initiative. This new initiative encourages global industry to prioritize environmentally friendly investments.
The journey to prove that the results had gone beyond net zero was not an easy one. BSI worked with AES to find a solution to calculating the net impact of the group when Scopes 1, 2 and 3 are considered. This is vital since controlling supply chain emissions in industry (Scope 3) is essential if the earth is to reach the net zero target.
Accepting the Challenges
The global industry must show it has a conscience about our living space. In the 1950s and 1960s, businesses were all about unbridled capitalism and profits. AES’s “29by29” investment makes the statement that its most important stakeholder is the planet. Accordingly, it took tangible steps to avoid or at least limit moving ever closer to the looming cataclysmic events. Imitate AES and raise the alarm.
Competent reliability professionals must firmly believe in leadership, and they must now exercise it. The time has come for them, as principled and ethical professionals, to become the stewards of responsible and actionable countermeasures. Accepting this stewardship obligation without further delay must be the profession’s most valued endeavor. Consider it vanity and utterly futile to expect a tortured planet to magically self-heal and miraculously overcome the existing calamity. Many parts of the earth are experiencing disasters even as we speak, and neither waiting nor endlessly debating the issue represent sensible abatement strategies.