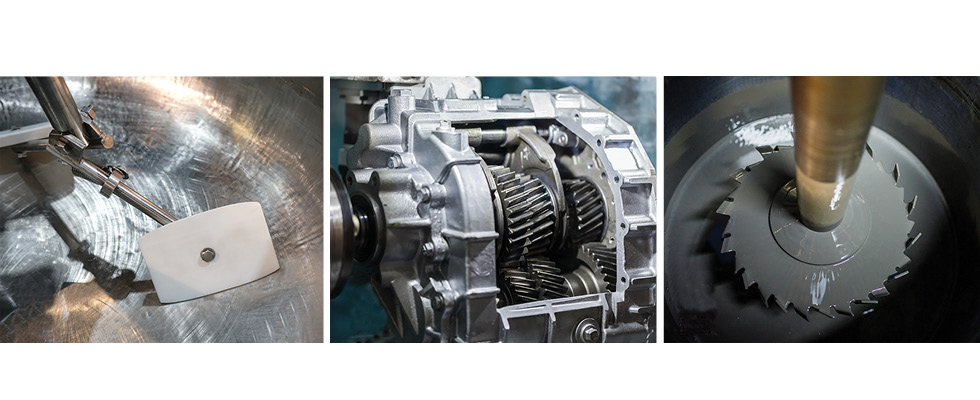
In the contemporary industrial landscape, the importance of predictive maintenance cannot be overstated. Companies are increasingly turning to advanced technologies to monitor the health of their machinery and prevent costly downtimes. Among these technologies, remote monitoring of mixer gearboxes and motors via accelerometers stands out as a particularly effective strategy. This article delves into the specifics of how accelerometer-based remote monitoring is transforming maintenance practices in industrial settings.
The Critical Role of Mixers in Industry
Mixers are indispensable in various industries, including pharmaceuticals, food processing, chemicals and construction. These machines, responsible for blending materials to precise specifications, depend heavily on the flawless operation of their gearboxes and motors. Traditionally, maintaining these components involved scheduled inspections and reactive maintenance, a practice that often leads to unexpected breakdowns and financial losses. However, with the advent of remote monitoring, industries now have the tools to preemptively address potential issues, thereby enhancing operational efficiency and reliability.
How Accelerometer-Based Remote Monitoring Works
Accelerometers are sensors that measure the acceleration forces acting on an object. When installed on mixer gearboxes and motors, they can detect vibrations and movements, providing valuable data about the machine’s condition. Here is a step-by-step breakdown of how this technology works in an industrial setting.
- Sensor installation: Accelerometers are strategically mounted on critical points of the mixer’s gearboxes and motors, such as bearing housings and motor casings. Proper placement is crucial to ensure accurate data capture.
- Data collection: These sensors continuously collect vibration data, capturing changes in frequency, amplitude and velocity. This data reflects the operational state of the machinery, including normal functioning and potential issues.
- Data transmission: The collected data is transmitted to a central monitoring system. This can be done via wired connections or, increasingly, through wireless networks, which offer greater flexibility and ease of installation.
- Data analysis: Advanced software tools analyze the incoming data in real-time. By applying sophisticated
algorithms, these tools can identify patterns and anomalies indicative
of specific problems, such as
imbalance, misalignment, bearing wear or gear defects. - Alerts and reporting: When the system detects an anomaly, it triggers alerts to notify maintenance personnel. Detailed reports can also be generated, providing insights into the machine’s condition and recommendations for maintenance actions.
Advantages of Remote Monitoring
- Early fault detection and prevention: One of the advantages of remote monitoring is the ability to detect faults early. By analyzing vibration data, the system can identify issues before they escalate into serious problems. For instance, a slight increase in vibration amplitude might indicate a developing bearing issue, allowing maintenance teams to address it promptly and avoid a complete gearbox failure.
- Enhanced equipment life span:
Regular monitoring and timely maintenance interventions help extend the life span of gearboxes and motors. By addressing minor issues before they lead to major breakdowns, companies can avoid the accelerated wear and tear associated with neglected maintenance. This not only improves equipment longevity but also enhances overall operational reliability. - Cost savings: While the initial investment in remote monitoring technology might be significant, the long-term cost savings are substantial. Preventive maintenance reduces the need for emergency repairs and unscheduled downtimes, both of which can be extremely costly. Moreover, optimizing maintenance schedules based on actual equipment condition rather than arbitrary time intervals can further reduce maintenance expenses.
- Improved safety: Operating faulty equipment poses serious safety risks to personnel. Remote monitoring enhances workplace safety by ensuring machines are in optimal condition. Early fault detection prevents hazardous situations, protecting both workers and the facility.
Implementing Remote Monitoring: Practical Considerations
- Selecting the right accelerometers: Choosing the appropriate accelerometers is crucial for effective monitoring. Factors to consider include the sensitivity range, frequency response and environmental durability of the sensors. Industrial environments can be harsh, so sensors must be robust enough to withstand extreme conditions.
- Integration with existing systems: To maximize the benefits of remote monitoring, it is important to integrate the monitoring system with the facility’s existing maintenance management software. This enables seamless scheduling of maintenance activities, tracking of equipment history and comprehensive reporting. Ensuring compatibility and interoperability between systems is key to a smooth implementation.
- Training and change management: Adopting new technology requires a cultural shift within the organization. Maintenance personnel need training to understand how to interpret vibration data and respond to alerts effectively. Additionally, fostering a proactive maintenance culture, where potential issues are addressed promptly, is essential for the success of remote monitoring initiatives.
The Future of Remote Monitoring
The integration of remote monitoring technologies is set to become the norm in industrial maintenance. As technology advances, it can be expected that even more sophisticated sensors, enhanced data analytics and greater connectivity will become available. AI and the Internet of Things (IoT) will further change remote monitoring, providing even deeper insights and more predictive capabilities.
Remote monitoring of mixer gearboxes and motors via accelerometers represents a leap forward in industrial maintenance. By enabling early fault detection, extending equipment life span, reducing maintenance costs and enhancing safety, this technology offers compelling benefits.
Industries that embrace these advancements will not only improve their operational efficiency but also gain a competitive edge in an increasingly demanding market. The continued evolution of remote monitoring promises even greater possibilities for the industrial sector in the future.