A retrofit brought reliability to the island’s wastewater system.
Zoeller Engineered Products
03/13/2018
Randall’s Island in New York City encompasses 433 acres on the Harlem and East Rivers, between Manhattan and Queens. It is a well known location, having been used for a variety of purposes over the past 350 years. In 1992, an alliance of dedicated New Yorkers saw its potential as a great recreational resource for the city’s residents. Since then, it has become the premier destination for sports and recreation, including 60 athletic fields, a golf and tennis center and Icahn Stadium, a world-class track and field facility. It has also become a popular event site for hosting concerts, art fairs and cultural festivals.
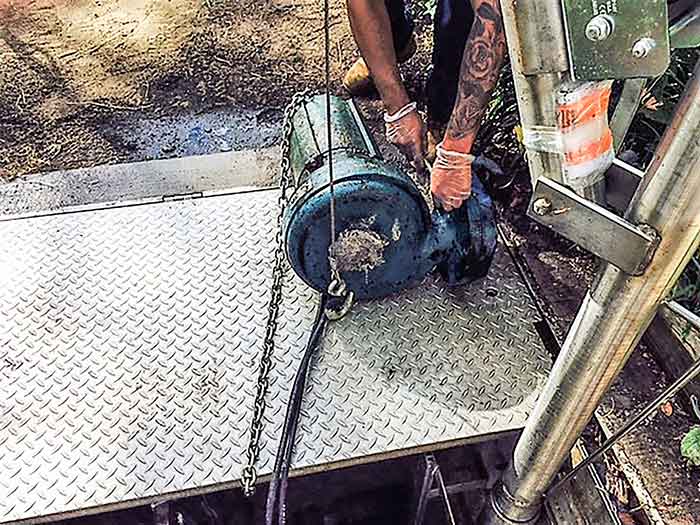
The Problem
The island is also home to the New York Department of Environmental Protection’s Wards Island Wastewater Treatment Plant. The island is serviced by a collection system, which includes numerous small pump stations. Being a year-round attraction, its 3 million annual visitors depend on its wastewater collection system and associated facilities. A few years ago, some submersible pump stations began to experience regular clogging problems requiring emergency repairs. The operators and service providers were looking for a solution when Gary Smith of G.T. Smith & Associates of Laurel Springs, New Jersey, became aware of the problem. He suggested that a unique product might be able to alleviate the problem and be retrofitted into the existing system. The ability to use the existing system while updating to a more modern product was intriguing, and they wanted to know more.The Solution
Information was provided that detailed a specially-designed grinder pump. The pump manufacturer noted that grinders have successfully handled many problem applications that cause traditional solids handling and grinder pumps to struggle. The design of this particular product incorporates rotating blades that cut axially as the solids are being pulled through a stationary flat grinder plate, designed with a unique pattern of slots and orifices. The cutter and plate are each made of 440C stainless steel hardened to a Rockwell HRC 58 “cutlery” steel that is considered the strongest and most desirable knife making material.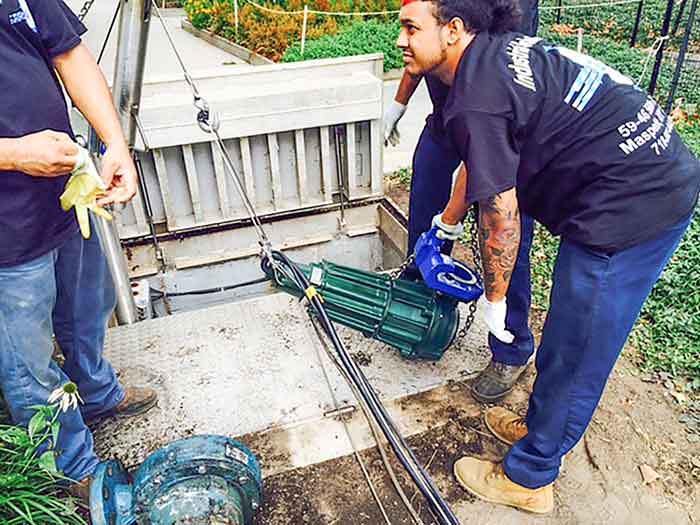