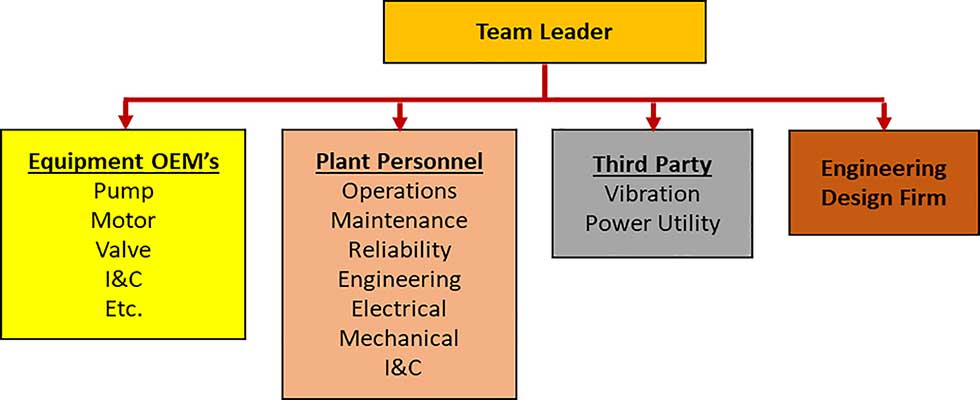
Last month, we addressed financial justification for performing a root cause failure analysis (RCFA). The case study used in last month’s article made a solid argument for why an RCFA should be performed on the system in question. An expenditure of $2 million over a three-year period is rather excessive when you consider the typical meantime between repair (MTBR) for a pump in this application is 15 years.
Let me repeat: meantime between repair not meantime between failure (MTBF); there is a distinct difference. MTBR means the pump is functioning but has degraded in performance, whereas MTBF means the pump has failed. The difference should be clearly identified when making the business case as well as in the history portion of the RCFA.
The next step in the RCFA process is compiling historical data. This process requires input from the entire team.
Asking the Right Questions
Locating and compiling the history of the system is a key step in the failure analysis process.
Locating drawings, engineering data, piping and instrumentation diagrams (P&ID), purchasing information as well as maintenance records require the full support of specific team members, as shown in Image 1.
The next step in compiling the history is collecting operational data, failure modes, downtime, maintenance issues and design commission issues.
This process requires the team members to ask the right questions of various parties that have some connection to the system during the design, installation, commissioning and operation but are not part of the RCFA team.
What Are the Right Questions?
The right questions can best be explained using a case study. This analysis involves a boiler feed pump in a large power plant. The pump failed during a high demand period resulting in a significant loss in production dollars.
Questions asked during the initial interview with key players and team members include:
- When was the boiler feed pump installed?
- Were there any problems during the installation and commissioning?
- What type of issues have you experienced since installation, and are any of these issues ongoing?
- When did each issue(s) start and how often did they occur?
- What have you done to address the issues as described?
Here were the team’s responses to the questions:
- System was installed in 1988 (RCFA performed in 2001)
- At the last minute, we went with a different brand boiler feedwater pump (BFWP)
- List of issues since startup includes: mechanical seal problems from initial startup; seals failed (replaced) every three to six months (both IB and OB/random); coupling (shim pack) failures; motor inboard bearing failures
- Plant would take a scheduled (short) outage to replace seals and coupling components
Note: Prior to disassembly, the pump and motor were always out of alignment.
The information supplied by the end user and key players provides some direction as to the potential root cause(s) of the failures and where to go for additional information to identify the multiple failure modes.
As we review the response to each question you see a pattern developing. It is apparent that the BFWP system has been an issue since installation. This raised a red flag: What are the costs associated with the ongoing failures for 13 years? At this point, additional data gathering is required, which is the next step in the RCFA process.
Analysis
We have met with key players and team members, developed some history on the system in question and, most importantly, were able to identify a strategy for the analysis process.
Next month, we will dig deeper into the analysis of the BFWP. You will be shocked at what we find.
Read more Pump System Standards by William Livoti here.