In the early hours of Dec. 3, 1984, water entered a tank containing 42 tons of methyl isocyanate (MIC). The resulting exothermic reaction increased the temperature inside the tank to more than 200 C (392 F) and dramatically raised the atmospheric pressure. As a result, about 30 metric tons of MIC escaped the tank into the atmosphere in less than one hour. The gases were blown by southeasterly winds over the Indian city of Bhopal, and the chaos that followed resulted in the greatest industrial disaster in history. The Bhopal gas tragedy, which originated at the Union Carbide India Limited (UCIL) plant in Bhopal, Madhya Pradesh, India, was reportedly responsible for 3,000 deaths within weeks of the leak. Another 8,000 people have since died from gas-related diseases. A 2006 government affidavit estimated that the toxic substance caused more than half a million injuries. Theories vary on how water originally entered the tank. Some believe a disgruntled worker introduced water directly into the tank as an act of sabotage. Others cite management negligence. One thing is undeniable—the Bhopal gas tragedy demonstrated the destructive power of isocyanates if they are not properly handled and contained.
Isocyanates
Isocyanates are a family of highly reactive, low molecular weight chemicals. Methyl isocyanate is a monofunctional isocyanate, while the most widely used compounds are diisocyanates and polyisocyanates. Diisocyanates contain two isocyanate groups while polyisocyanates are usually derived from diisocyanates and may contain several isocyanate groups. The most commonly used diisocyanates include methylenebis (phenyl isocyanate), known as MDI, and toluene diisocyanate (TDI).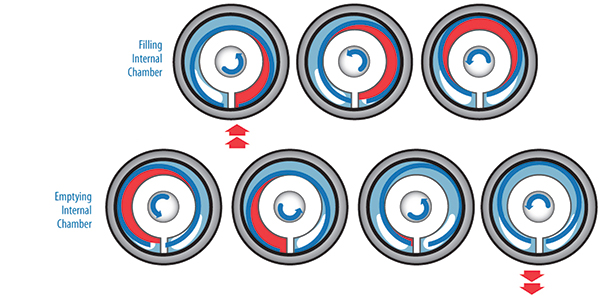