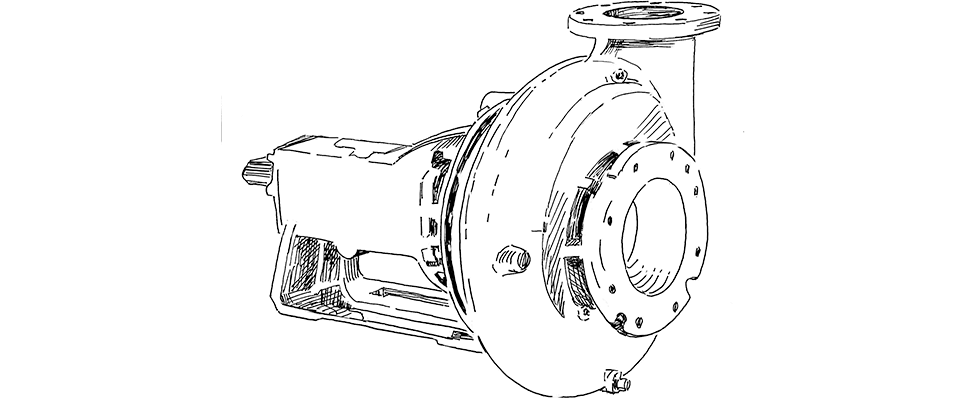
Wastewater pumps perform a behind the scenes, yet critical, job that most people do not think about. They are found in lift stations and wastewater treatment plants doing their job day in and day out.
Yet, if a user comes across an experienced wastewater operator and asks what they like or dislike about the pumps, the operator will have a must-have list of features that keep the station running.
Sizing a wastewater pump is like sizing a pump for a clean water application: Users need to know the application information such as flow and head, fluid type, and installation orientation or space constraints. With wastewater applications, however, there are a few other factors to consider—the biggest being solids. Fibrous materials such as flushable wipes and rags lead to ragging issues in lift stations and wastewater plants. Wastewater and sewage-type impellers are specifically designed to deal with this issue.
This article explains the types of solids-handling pumps and impeller types that will help users make a smart choice when selecting a pump for a wastewater lift station application.
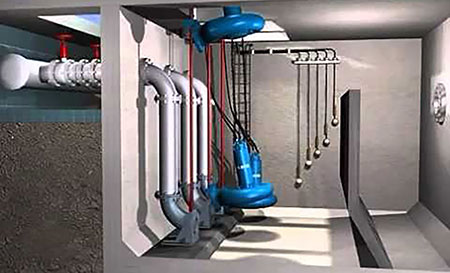
Types of Pumps
Submersible pumps
Submersible pumps are designed to operate in wastewater. A close-coupled sealed motor allows for complete submergence, eliminating the need for a separate dry-well, which can decrease installation costs.
Submersible pumps typically feature dual oil-lubricated mechanical seals with moisture sensing probes and an associated alarm relay. An alarm sounds when it detects water in the oil chamber. This sensor protects against moisture entering the motor and causing issues by alerting the operator to the seal failure.
Since submersible pumps are installed in wastewater wet wells, access to the pumps is limited. Operators must remove the pump via the guide rail system to inspect or service the equipment.
Dry-pit pumps
Dry-pit pumps are installed next to a wet well or sump. This allows for the use of a nonclog centrifugal pump and motor.
Solids-handling impellers will pass many types of solids. They can be mounted vertically or horizontally, allowing flexibility for space constraints within the dry-pit vault. Dry-pit pumps keep the pump out of the wastewater, allowing for personnel to easily diagnose a pump during operation. Working on a pump that is not covered in sewage minimizes safety risks.
A downside of the dry-pit pump is the possibility of flooding. Water in the dry-pit would destroy standard pump motors.
If the dry-pit is susceptible to flooding, a dry-pit submersible pump might be an option. These are similar, if not identical, to the submersible pumps discussed before. Traditional submersible pumps use wastewater to cool the motor. In a dry-pit application, there is no surrounding fluid to use for cooling. Therefore, submersible dry-pit pumps have oil-filled submersible motors and/or cooling jackets to provide adequate cooling and insurance against inadvertent dry-pit flooding.
Self-priming pumps
Self-priming pumps are an aboveground alternative to submersible or dry-pit pumps. Designed for suction lift applications (like lift stations), self-priming pumps prime by extracting air from the suction side and discharging it back into the wet well.
Once primed, this pump operates the same as standard solids-handling centrifugal pumps.
Self-priming, solids-handling pumps are designed to pass solids. Like dry-pit pumps, they usually have a longer anticipated life than submersible pumps due to the clean atmosphere above the wet well and access for preventative maintenance.
Types of Impellers
The aforementioned wastewater pumps are often fitted with one of the following impeller types. Each is designed specifically for a combination of solids-handling and efficiency, and there is always a trade-off between the two.
Semi-open impeller
Semi-open, nonclog impellers feature a back shroud with a limited number of vanes (one-vane or two-vane are typical) and can usually pass a 3-inch spherical solid with a 3- or 4-inch submersible sewage pump. The small number of vanes provides large impeller openings for the solids to pass through. Set clearances between the wear plate and the leading edge of the impeller allow for higher efficiency when compared to vortex impellers, but less than enclosed channel impellers. This impeller type is standard in submersible, dry-pit and self-priming pumps.
Vortex impeller
Vortex impellers are for applications with extreme ragging issues and are found in submersible and dry-pit applications.
These impellers are installed in the top of the volute and out of the flow path. Vortex impellers create a whirlpool effect in the volute, carrying water and solids through the pump and out the discharge without direct contact.
This reduces the risk of pump clogging and impeller wear. Pumps with vortex impellers have reduced efficiency due to the vortex and lack of tight clearances.
A decrease in efficiency of about 30 percent is possible from a semi-open impeller. Reduced maintenance costs may outweigh the loss in efficiency for some high ragging applications.
Enclosed channel impeller
This impeller design contains a front and back shroud, creating enclosed channels for wastewater and solids to pass through. Due to the enclosed channels and tight clearances between impeller and wear rings, this impeller is known to be efficient. Issues with this impeller arise with stringy fibrous materials like rags.
Conclusion
When selecting a wastewater pump, consider the application constraints and features needed in a pump system. If easy maintenance is of the essence, choose a self-priming or dry-pit installation. If cost is an obstacle, submersible pumps will allow for a more compact installation. In either case, weigh efficiency versus solids-handling capability for long-term operation and reliability of the lift station.