The future of desalination will require a combination of experienced-based design and environmentally friendly technologies.
IDE Technologies
02/27/2017
Today’s reverse osmosis (RO) plant design is based on diverse technological knowledge and, just as importantly, on operational experience, which can be a valuable asset for design teams. For desalination plants, it is important to explore a methodology for bridging between operation and maintenance (O&M) experience and design, while finding the process design of the future. O&M teams can gain operational experience through daily work of performance monitoring and overcoming challenges. Typical objectives of the operation team include improving plant performance, correcting malfunctions, boosting compliance with new regulations and reducing operational costs.
.jpg)
- periodic meetings focused on sharing knowledge between O&M companies and design engineers
- on-site piloting, which allows technical interaction between the O&M team and the design engineers
- monthly reports issued by the O&M managers
- providing technical and process support to the operation team as required
- inviting lead technologists and operation managers to participate in design review meetings
Optimization to Reduce O&M Cost
The design team should learn the RO plant’s behavior from the O&M personnel and optimize the design accordingly. For example, the chemical consumption can be reduced through improvements and optimizations performed during O&M. At the Ashkelon Desalination Plant in Israel, the second pass chemical consumption of caustic soda and sulfuric acid were optimized through day-to-day monitoring of the performance parameters such as actual boron rejection, membrane-feed pressure and normalized flow. Ferric chloride consumption was optimized through monitoring of pretreatment performances and by using improved control methods.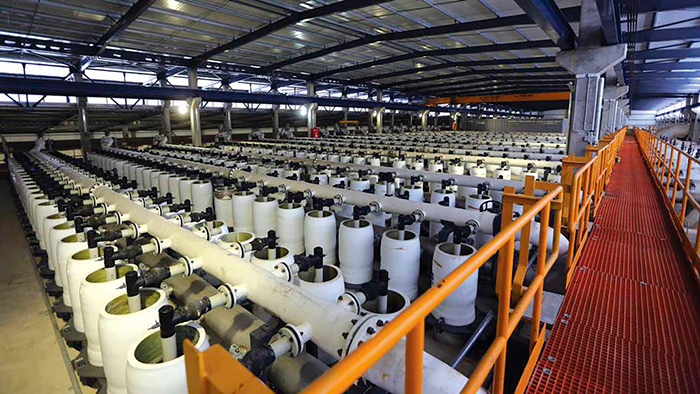