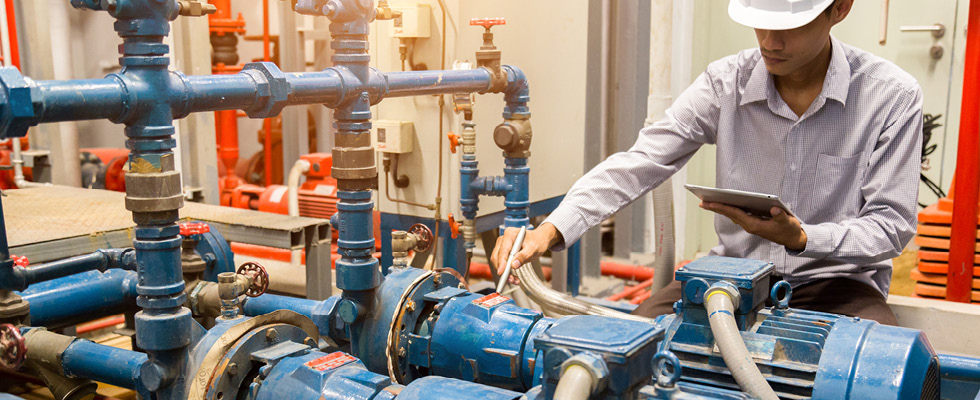
Electric motors are used in almost every industrial manufacturing process and have been the backbone of industry for over a century. There are over 52 million motor systems in industrial and commercial facilities across the United States. These motors account for 1,079 terawatt hours (TWh) of electricity per year—about 29% of total electric grid load.
Motors single-handedly account for nearly 1/3 of the total grid load, yet many motor companies are not focusing their sustainability efforts on motor energy efficiency. Geared motors require a high degree of maintenance, monitoring and replacement. Moreover, certain types of motors are prone to leakage (oil-lubricated systems), and others produce substantial noise during operation (spur gear motors). The cost associated with motor manufacturing is high due to high labor costs and increasing prices for raw materials. These costs are continuing to rise with no end in sight, partially due to geopolitical conflicts along the supply chain leading to long lead times for materials. Electric motors with improved energy efficiency are designed to provide the same output as existing motors by consuming lesser amounts of power, saving operational costs and carbon emissions for motor users.
Pressure from shareholders and net zero initiatives have resulted in an increased interest for sustainability in the motor industry. In 2021, the U.S. unveiled a comprehensive strategy aimed at achieving carbon neutrality by 2050. This plan places a strong emphasis on expanding electric vehicle infrastructure and transitioning the nation away from fossil fuels and toward renewable energy sources such as solar and wind power. In response, many major motor companies in the U.S. have implemented strategies to increase sustainability efforts. Many organizations are becoming more transparent about the number of emissions they produce and where they originate from.
Companies break down their carbon emissions into Scope 1, Scope 2 and Scope 3. Scope 1 emissions are direct greenhouse gas emissions that occur from sources directly controlled or owned by an organization. Scope 2 emissions are indirect emissions associated with the purchase of electricity, steam, heat or cooling. Scope 3 encompasses emissions that are not produced by the company itself but are a result of the supply chain and use/disposal of the product. Scope 3 emissions are created when a motor company buys a motor from an OEM, uses it until it no longer functions and then disposes of it. Scope 3 emissions account for more than 90% of a motor company’s annual carbon emissions in the motor industry. Scope 3 emissions are notoriously difficult to decrease due to their scale and ambiguity. There have been some efforts made to reduce these emissions through supply chain localization, preventative maintenance and decreasing the number of materials used for products.
Due to the challenges that reducing Scope 3 carbon emissions present, motor companies focus their efforts toward reducing Scope 1 and Scope 2 emissions. This involves reducing any emissions produced on-site (including emissions from fleet vehicles), emissions from generating electricity to power the facility and emissions from waste generated. Many sustainability efforts within industrial facilities include the installation of LED lighting and implementing renewable energy sources like wind, solar and geothermal. These efforts can significantly reduce Scope 1 and Scope 2 emissions, but over 90% of overall emissions are still part of Scope 3. One incentive for implementing sustainability efforts like LED lighting includes cost reductions from improved energy efficiency.
Currently, rising energy bills are making production substantially more expensive for many manufacturers. This is where energy-efficient motors can make a major impact. Energy-efficient motors not only reduce the electricity required for a facility’s operation but also contribute to lower Scope 3 emissions through improved machine design.
High-efficiency motors are often designed to be smaller and lighter compared to traditional motors. This is possible through using less critical materials, which enables a reduction in Scope 3 emissions while improving machine size and weight. Motors are often made of steel, copper and rare earth magnets. Since 2020, there have been long lead times for acquiring these materials, specifically from the Asia-Pacific region. This is often accompanied by a higher price tag, meaning motor manufacturers must pay more for these critical materials and increase product prices.
A small number of energy-efficient motors do not rely on the same volumes of these materials, and very few opt to not rely on materials like permanent magnets at all. Through improving machine design to use little or no critical materials, fewer carbon emissions can be produced in the making of the product, and the price of the product does not have to increase with supply chain concerns like geopolitical conflicts or other disruptions. When it comes time to discard the motor at the end of its life cycle, there are fewer materials being sent to a landfill or recycling facility.
Along with the reduction of materials, some energy-efficient motors require less maintenance. The average life span for a traditional motor is 10-20 years, but reaching a longer life span requires consistent repairs over the course of the machine’s use. Some companies are enabling motors to function in a wide range of applications without the need of a gearbox and/or a belt system. This technology has the potential to be immensely impactful for the manufacturing sector.
Industrial facilities experience approximately 8 million hours annually of unplanned motor system downtime due to failure. If the motor needs to be replaced, 74% of facilities replace the failed motor with one of the same size, and only 3% reevaluate system needs and select a motor based on the evaluation results. Motors are not only a major source of energy costs, but the ways they are repaired or replaced lead to a cycle of inefficiency and tremendous waste within industrial facilities. Tightening belt systems are involved in 28% of motor repairs, which requires skilled labor that can be costly and difficult to find. Energy-efficient motors allow industrial facilities to spend less money and downtime on repairs while creating less waste and promoting a circular economy.
Purchasing an energy-efficient motor may incur higher upfront costs compared to a traditional motor. However, the combination of reduced maintenance and significant electricity savings can result in substantial financial benefits, potentially saving manufacturers thousands of dollars per motor annually. With many facilities operating thousands of motors for 24 hours a day and 365 days a year, the overall savings can be immense.
Currently, when purchasing motors, 36% of facilities use the lowest cost first, and 8% use the lowest lifetime running costs to determine which product is the best fit for them. Upfront costs usually outweigh lifetime running costs. This results in more waste, higher energy bills and an increase in staff to maintain cheaper, less reliable motors. The motor industry is approaching a pivotal moment where the focus on long-term costs is becoming increasingly crucial. This shift is driven by the cost savings that can be achieved both in the long run and in the near future, particularly in terms of reduced repair and maintenance expenses.
With these factors at the forefront of the motor industry, the way consumers look at motors is at a critical juncture in a worldwide shift towards sustainability. Rising inflation and energy costs are highlighting the inefficiencies of traditional motor systems. While the focus has primarily been on reducing Scope 1 and Scope 2 emissions, the push toward net zero goals requires greater attention to Scope 3 emissions.
Motors are not often considered when improving energy efficiency. Most manufacturers repurchase what they know instead of trying to evolve their motor needs in conjunction with net zero initiatives. Energy-efficient motors offer companies reliable, resilient and energy-saving solutions, playing a vital role in a broader effort toward sustainability.