Despite well-documented pump system standards and basic requirements, omission of certain crucial design steps remains a problem in the industry, often causing disastrous outcomes for the end user. When suppliers, manufacturers and/or contractors take shortcuts, technical and commercial risk can present serious ramifications for a large project. Communication failures between the end user’s staff, suppliers and contractors can intensify problems, especially when pumps that may not be appropriate for a given job are commissioned and put into service. Without the end user’s knowledge, a facility may install pumps that have not been properly tested for the application, were fabricated to inferior standards or subject to other shortcuts that adversely affect performance. Sometimes the end user becomes aware of shortcut-derived flaws during the commissioning stage. Other times, problems in equipment or system design might not be evident immediately—they surface during subsequent plant and equipment maintenance that reveals potentially dangerous, hidden conditions. The ensuing problems can lead to tense project politics and expensive rectification, including hiring independent consultants. Suppliers, manufacturers and contractors take shortcuts for various reasons. These shortcuts can be attributed to a lack of experience with how a pump might be deployed in the field. There may be miscommunication of technical details from both the user and supplier or between the user and contractor. Budget constraints and concerns can also result in omissions; commercial reality can cause a manufacturer or supplier to make a project’s bottom line cheaper by reducing the cost of equipment and cutting corners.
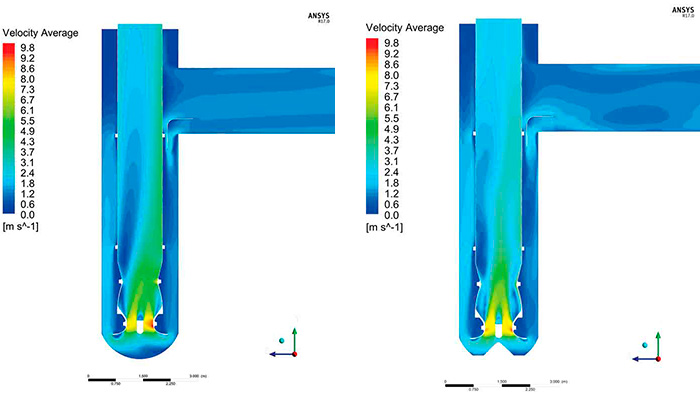
Severe Damage
One unfortunate case that occurred at a geothermal power station in New Zealand highlights the damage that can happen quickly when a plant takes shortcuts. Four relatively large, single-stage vertical pumps—characterized by a capacity of 45,000 gallons per minute (gpm) at 75 feet, 590 revolutions per minute (rpm) and 1,200-horsepower (hp) motors—were installed in canisters in a hotwell application (two per turbine). During commissioning, the pumps experienced unusual noise and vibration. The step change in the vibration level of one of the pumps prompted removal after seven weeks. Inspection of this pump and its partner revealed several failures including severe impeller-vane cavitation, a broken impeller vane, impeller/liner rub and line-bearings wear. A rough check on net positive suction head available (NPSHA) indicated marginal readings. However, this condition would not have caused the severe cavitation damage over such a brief period. The cavitation damage on both the suction and pressure faces of the blades, with no fixed pattern, indicated a recirculation issue; however, the pump flow was not low enough to suspect the classical problem of low-flow suction recirculation. The root-cause investigation turned to the intake design with particular focus on suction-flow velocity disturbance at the pump bell mouth causing asymmetrical flow. Pipe sizing and intake design were both in line with the general flow-velocity guidelines provided by the Hydraulic Institute standard ANSI/HI 9.8-1998. However, it became clear that one of the basic model test recommendations for pumps with flows higher than 40,000 gpm per pump had not been carried out.Finding Answers
Further investigation showed that the pump supplier had not previously used this pump in a canister application. Proper due diligence would have shown the need for a computational fluid dynamics (CFD) analysis of the sump-intake design. When this analysis was completed after the pumps were pulled, it revealed that the flow was biased toward the suction inlet pipe at the bell mouth entry.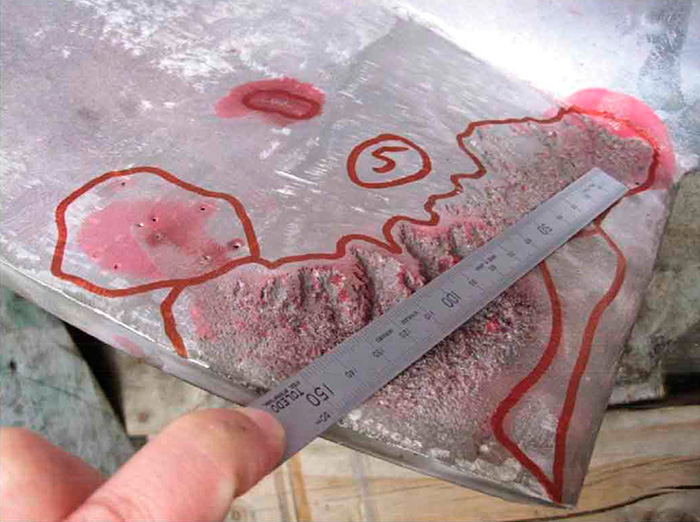
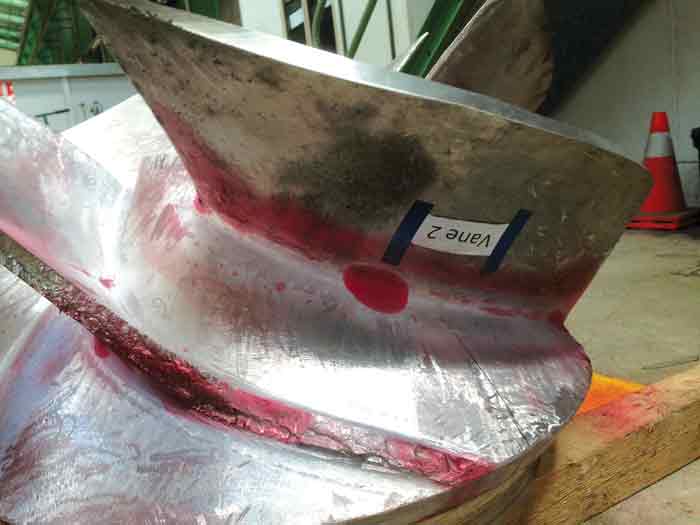
Success Through Modifications
After two engineering companies conducted parallel sets of CFD analysis to the intake and canister, a solution to the suction-flow velocity disturbance emerged. Trials of different geometry changes were analyzed using CFD analysis and confirmed by model tests. The concept of the installation of a hydraulic cone in each pump emerged to rectify the situation. The velocities and pressure distribution of the original and modified geometries were compared.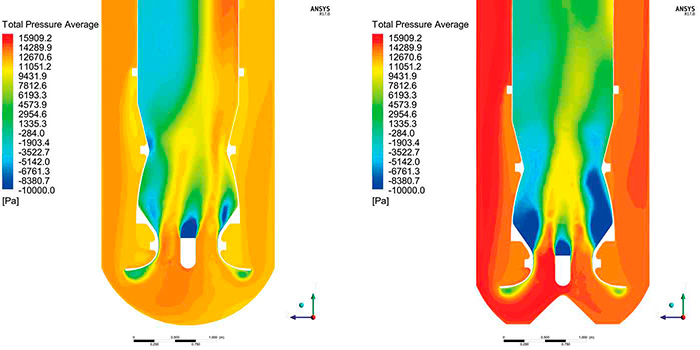