Determining the right size centrifugal pump for the job, whether a sewer bypass, industrial site or construction area, is no simple task. The job is riddled with enough friction loss calculations, net positive suction head (NPSH) formulas and total dynamic head figures to make anyone’s head spin. Fortunately, pump distributors and manufacturers are well-versed in sizing pumps and can be the best resource during the selection process. Even so, it’s a good idea to be familiar with what goes into the decision. First and foremost, the easiest part of selecting a centrifugal pump is determining the type of material the pump will need to move. If the pump is handling water laden with sticks, debris or waste, choose a wastewater pump. If it’s moving thick or sandy water, then a slurry pump is in order. Choosing one that is made to handle the type of material being pumped ensures two things: it can effectively move all material, and it can do so without damage to the pump components.
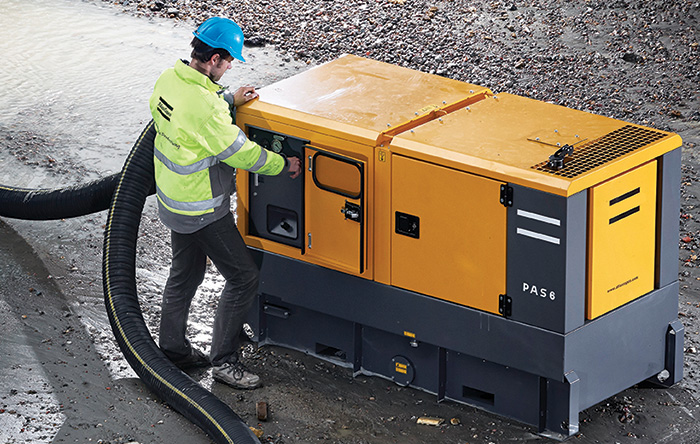
Suction Lift & Friction Losses
The next step is calculating the amount of suction that is required to move the fluid from the source up to the pump centerline, or eye of the impeller. This number is also called net positive suction head required, or NPSHr. But before determining the NPSHr to effectively move fluids, the amount of net positive suction head available, or NPSHa, must be calculated. This is basically the amount of pressure the system inherently has based on the elevation and system setup. Fluid moves from areas of high pressure to low pressure, and NPSHa indicates the amount of pressure the pump system has to work with to move the fluid. NPSHa includes atmospheric pressure as well as any friction losses that occur because of distance, elbows in the system or valves—basically everything that will create resistance.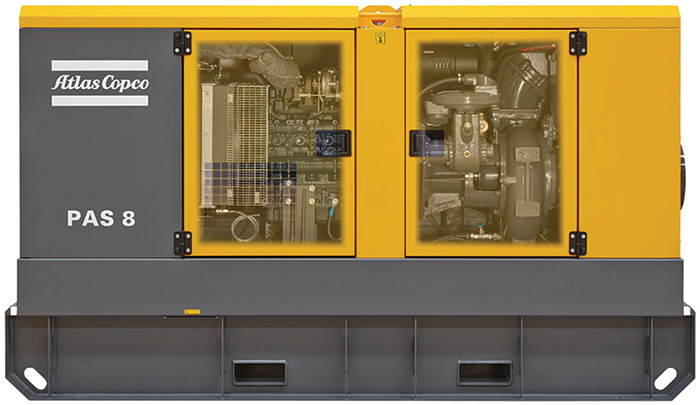