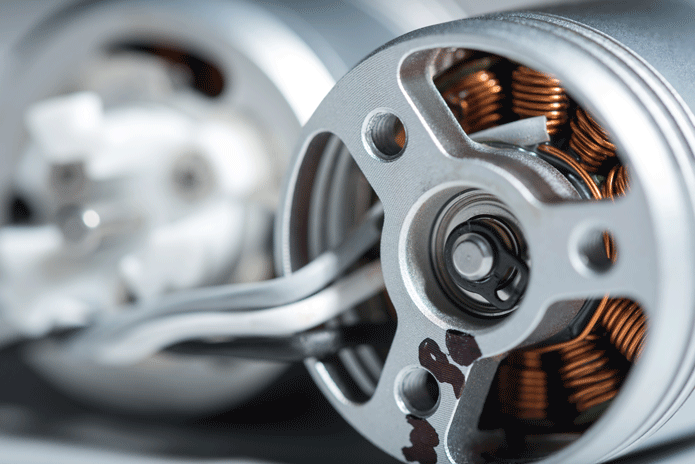
Thanks to new smart motor technology, wastewater treatment plant operators can now improve the accuracy of chemical dosing in their treatment processes.
Because they include a pump-intelligent variable frequency drive (VFD), these
smart motors can automatically control the small quantities of chemicals that variable speed meter pumps dispense into wastewater flow. The ability to adjust dosage automatically addresses an issue that has long-complicated wastewater treatment: the inconsistency in wastewater flow and composition.
Water flow through a treatment facility can vary over a day, with flow being the greatest in the morning and evening hours, before dropping late at night. Flows often surge during heavy rains and decrease during periods of drought. Water quality also varies over time, depending on the concentration of the contaminants and other waste matter it contains.
A variety of chemicals is commonly used to remove solid particles and sludge, adjust pH, control odor and provide disinfection. The dosage for each must be proportional to the flow rate and quality of the water being treated. There is also the question of cost. Plant operators must see that water is treated appropriately without wasting chemicals.
Automating the Process
Historically, wastewater treatment chemicals have been added manually, based on observations of flow rate and measurements of undesirable elements in the treated water. However, manual interventions can lead to under- or over-dosing chemicals.
By implementing a control system that regulates the flow of treatment chemicals dispensed through the metering pump automatically, operators can improve accuracy and minimize chemical costs.
That is what happens when a pump-intelligent VFD is integrated with an alternating current (AC) induction motor in a single package. The rates at which chemicals are dispensed can be based on any combination of control variables, from incoming flow rates to incoming and outgoing water quality.
Some smart motor solutions go a step further and include a programmable logic controller (PLC) capable of performing complex logic functions, such as slowing the pump during its suction phase to prevent cavitation of highly viscous fluids or dispensing preselected quantities in batch processing.
When delivered as part of a metering pump, a smart motor can also be preloaded with software that has been custom-tailored by the pump manufacturer for the metering pump operation. For example, a pump’s known characteristics can be modeled in the software, enabling the drive to determine certain aspects of system performance, such as flow rate, without relying on external sensors.
To make a pump easier to use, a pump OEM can, in some cases, program a smart motor to accept input parameters in terms that are relevant to metering pump operators. Multiple digital and analog inputs and outputs may be available to connect 4-20 milliamps (mA) control loops, system alarms and local controls. Depending on the model, some smart motors can also be integrated into a facility’s existing control infrastructure using the native Modbus support, available Ethernet and other built-in communications capabilities.
Understanding Your Motor Options
Depending on the situation, a control loop may require different levels of precision and response time to ensure the output water flow falls within a wastewater treatment facility’s target parameters for quality and volume. This can impact the motor technology chosen to power the metering pump. To understand how, look at the operation of a reciprocating metering pump, which is a positive displacement pump. Unlike the centrifugal pumps used to move wastewater through a facility, the loads placed on reciprocating metering pump motors change little as a function of pump speed.
These motors, therefore, operate under a constant-torque load. That means the motor will draw more current at low speeds than if operated under a variable torque load. When slowed down, the pump motor dissipates more heat when driving a metering pump than it might with a comparable variable torque load. It will have less air flow to dissipate as well.
General purpose, inverter-suitable AC induction motors can be a good option for driving variable speed metering pumps, provided any necessary speed reduction does not overheat the motor and the incoming power from the variable speed drive does not stress the motor’s windings.
For these applications, motor turndown ratio should be limited to 10:1 so that the required four-pole pump motor speed falls in the range of 180 to 1,800 rotations per minute (rpm). For maximum load requirements, heat-rise and additional cooling should be considered to ensure sufficient cooling at low speeds. To minimize the chance that harmful reflected waves resulting from the VFD’s pulse width modulation (PWM) waveform will reach levels that will damage the motor’s winding insulation, these motors should be located in proximity to the VFD.
Most motor manufacturers agree that a full inverter duty motor, in other words, a motor that meets National Electrical Manufacturers Association (NEMA) MG-1 Part 31, will deliver the longest life and best operation when run on a VFD.
If a wastewater treatment facility’s control loop requires more precise control of the metering pump’s motor, a motor that meets NEMA MG-1 Part 31 is not only preferred but required. For example, an inverter duty AC induction motor that complies with Part 31 requirements and can be used when up to 20:1 motor speed turndown would meet this standard. This would enable a four-pole motor to operate from 1,800 rpm down to 90 rpm for extended lengths of time.
Inverter duty motors also have higher resistance to voltage spikes generated by the reflected waves from the VFD. These motors include shaft grounding rings to steer harmful shaft currents away from the motor bearings, minimizing the electrical discharge machine (EMD)-induced etching that can lead to bearing failure. The winding thermostats on inverter duty motors can also be monitored by the control system, warning operators when safe motor operating temperatures are exceeded.
When even faster responses and tighter control over metering pump flow rates are necessary, vector duty motors can be employed. These motors offer as much as 5,000:1 turn down ratio, enabling a four-pole motor to drive a constant torque load from 1,800 rpm down to just 0.36 rpm. When equipped with encoders and driven by vector duty VFDs, the precision control they deliver is excellent.
Getting Smart About Dosing Control
Every wastewater treatment facility’s processing needs are different. System architecture and control scheme will dictate the response time and precision required to meet them. Motor manufacturers have developed multiple technologies, each with their own cost/performance benefits that are suitable for powering the variable speed metering pumps that are integral to the wastewater treatment process.
By choosing the right motor technology for the job, plant operators will be able to achieve the required level of performance while minimizing costs.