An industry with aging infrastructure and increasing demands needs better monitoring technology.
04/25/2016
Between 2009 and 2012, the U.S. faced more than 1,700 refinery shutdowns, an average of over 1.16 shutdowns per day, and almost "92 percent of the maintenance-related shutdowns were unplanned."1 So a proper maintenance strategy is critical. The goals for any maintenance strategy are to:
- boost revenue through increased uptime and asset maintenance optimization
- reduce costs by decreasing warranty repair expenses, extending mean time between failures, reducing the frequency of unscheduled downtime and optimizing the workforce
- manage risk and increase safety by minimizing worker contact with dangerous machines and environments and preventing catastrophic failures
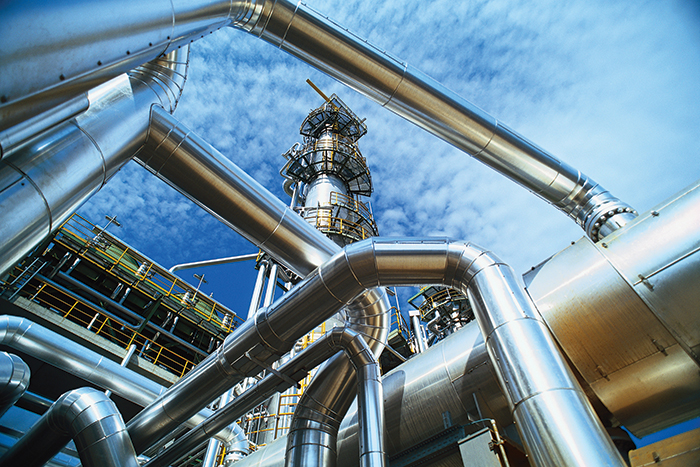
- built-in analytics and alarming capabilities and remote interactive visualization of waveform data
- scalability to hundreds of acquisition devices per server
- support for vibration and process measurements using integrated hardware options
- remote management of monitoring systems and users
- IT-friendly security features that include user and device authentication
- digitalrefining.com/article_1000773.pdf
- eia.gov/dnav/pet/pet_pnp_cap1_dcu_nus_a.htm
- eia.gov/tools/faqs/faq.cfm?id=29&t=6
- EMC Digital Universe with Research & Analysis by IDC—The Digital Universe of Opportunities: Rich Data and the Increasing Value of the Internet of Things
- The Electric Power Research Institute has calculated comparative maintenance costs in US dollars per horsepower (hp) for each maintenance strategy.
- mckinsey.com/insights/business_technology/big_data_whats_your_plan
4 Common Maintenance Approaches
- Reactive. Using this approach, facility employees wait until something breaks to fix it. Although the upfront costs for this approach are low, hidden costs such as safety, unplanned interruption and ripple effects to other machines in the critical path can be high.
- Scheduled/preventive. This has become the default strategy in many industries, and for good reason. Most professionals think this is the best approach because it is popular and recommended by many machine providers to ensure the integrity of the machine. The maintenance intervals are clear and defined, but facilities risk fixing a machine that is not broken and stopping production more often than necessary. This approach also runs the risk of excessive tinkering that could damage the machine being maintained while increasing operational costs.
- Preventive with manual/route-based measurements. This involves periodically measuring key performance indicators such as vibration, temperature, proximity and power. This technique is a good first step to achieving maintenance objectives, but it has its shortcomings. Human error, diagnosing skill, disparate systems and the inability to scale prevent this from being a great solution.
- Automated or online automated diagnostics. Smart equipment on machines can help predict issues before they wreak havoc on your budget, safety, efficiency or yield. In an ideal world, an automated solution would be the optimal maintenance strategy. But, as often is the case, it is too expensive and does not have the promise of return on investment for all but the most critical of assets. However, that notion has begun to change.