Industrial enclosures go by a lot of names. You may hear them called a pump house, valve house, hot box, utility shed, precast building, aluminum shelter…the list goes on. No matter what you call them, there's a commonality. Someone decided that the equipment inside needs protection.
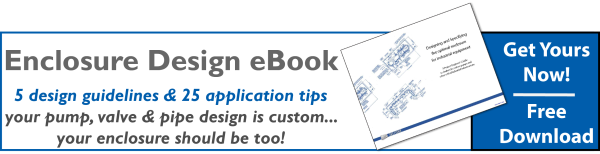
From Widely Ranging Risks
Maintaining and protecting pumps and process related equipment of any type in a fast-paced industrial manufacturing facility is instrumental to their success. These critical devices must function as expected - suddenly, in an emergency, and routinely - to keep everything clicking along without expensive downtime or production interruption.
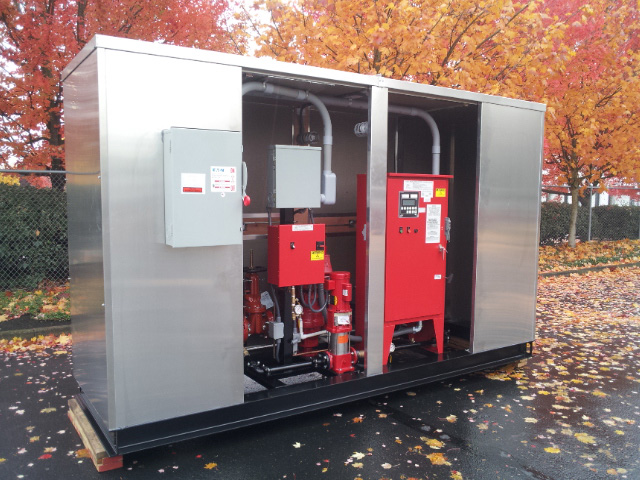
We've all met Murphy, and we know how his law impacts all of us. Typical risks to these critical pumps, valves, generators, pump skids and other devices include:
- cold – an insulated or heated enclosure will keep devices and pipes from freezing and bursting
- heat – sensitive electronics must be kept cool enough to function properly with air conditioning, louvers or fans
- accidents – when someone backs a forklift or truck into an aluminum enclosure, it doesn’t stop production but running over the equipment certainly would
- vandalism – a boring metal box keeps your equipment from being an interesting, attention grabbing installation
- theft – as metal prices recover, demand for scrap will increase, but a locked industrial enclosure keeps thieves away
- terrorism – a locked metal enclosure removes access to fresh water supplies, safety related devices like railroad switching motors and gate devices, and systems for processing industrial chemicals which are potential targets for those seeking to create mayhem
While Maintaining Flexibility and Access
It’s clear that this protection is necessary. However, all of these devices also need regular preventative maintenance, testing and tuning to keep them operating at peak efficiency. It's critical to ensure that your industrial enclosure solution not only protects your equipment from risks, but also allows you easy access at any time for routine maintenance or repairs. You may need multiple lockable doors, panels, and sometimes roof access so these important jobs can get done. Additionally, the crew will need room inside to work.
That really means that most industrial enclosure applications should be treated as a custom project. Many sales reps, engineers, project managers and facility managers hesitate to do that because they think the “c” word (custom) means high price, long lead-time, and a big hassle.
That's understandable, but it’s not necessarily true when it comes to equipment enclosures. It's actually completely economical to customize a wide range of features. Dimensions are fully customizable, along with aesthetic details like color. Custom penetrations can be easily incorporated for existing piping. Roof access and panels can be provided for direct access to critical components to address the realities of maintenance that often aren't designed in up front. If you make it easy to maintain, it's more likely that it will be.
The Five Design Considerations for Industrial Enclosures
When it comes to the requirements for both standard and custom enclosures, we’ve determined there are five main categories. Solutions for any and all the problems mentioned can be included in the design as long as you consider:
- size and strength
- climate control
- aesthetics and protection
- access and maintenance
- application flexibility
Evaluate protective enclosure manufacturers for these capabilities and you’ll have a much easier time getting what you want and what your equipment needs. Read in depth about each of the five considerations in our ebook here.