NSK is committed to helping companies increase their productivity, most of all by helping them reduce manufacturing costs, maintenance costs, and production losses. NSK's products and solutions can be found everywhere where machines are in motion—even under the toughest conditions.
NSK is known as an expert in our field. Recently we were consulted by a petrochemical refinery that was experiencing increased failures on centrifugal pump bearings. These failures were responsible for massive production costs and losses.
It’s important to understand the larger context of the industry to examine the impact of the plant’s bearing failures. In the petrochemical industry, if a process pump fails in a plant, it can lead to costly downtime. In these plants, centrifugal pumps are used to transport liquids at every stage of the process, and they are among the most sensitive components used in this industry. Because of this, it is of the utmost importance that all failures are minimized, if not completely eliminated.
Within the plants, pump applications place a great deal of strain on bearings. That’s why the materials used for bearings must withstand tough conditions. The bearings have to support axial, radial or combined loads. They also have to run equally reliably at low and high speeds (1,500 rpm to 3,000 rpm) and perform while handling different lubrication conditions with ease.
Minimizing downtime and maximizing productivity are crucial in the petrochemical industry. The machine components used – such as pumps, compressors, electric motors, blowers, and ventilators – are particularly susceptible to change. That’s why it’s even more crucial for bearings to work reliably and precisely. NSK specialists are in touch with the research and development teams at OEMs that produce components for petrochemical systems. This enables them to develop new bearing solutions at every level of a given project.
The petrochemical refinery requested our engineers to review their application and offer a potential solution. Before making our recommendations, we performed a Failed Bearing Analysis to investigate, which showed that the existing roller bearings were experiencing roller skidding due to an insufficient radial load and low roller traction, with failure as the end result. An application review also revealed that the plant had recently changed the motor drive from belt to direct drive. This resulted in the removal of the belt load and a consequential reduction of radial loading.
Taking into consideration these findings, our engineers proposed an alternative Deep Groove Ball Bearing assembly, which was to be tested in a trial. The trial revealed that bearing life was extended by three times. In fact, there were no breakdowns in a 12-month period, with the pump remaining functional. The Deep Groove Ball Bearings brought old bearing costs down. Breakdowns were reduced and accompanying labour costs were eliminated. The refinery’s loss production costs were also down with a total savings of $29,832 annually. As a result, the refinery saw a significant reduction in replacement part maintenance costs and productivity improvements.
The solution featured a steel cage, and an increased high load rating that was 7% to 19% higher in dynamic load ratings. It also has an optimized internal design, with large rolling elements offering a longer life, with a 6% to 22% increase in ISO L10 life. It is interchangeable with standard Deep Groove Ball Bearings, with the possibility of downsizing. These customizable features, when combined with the product’s great efficiency, makes it the perfect fit for an industry as demanding as petrochemical.
Deep Groove ball bearings, the most common form of rolling bearings, are used in many types of applications, particularly those where high speeds and low power loss are required. NSK deep groove ball bearings can handle not only radial forces, but also moderate axial loads in both directions. They are easy to install and can be deployed in a variety of configurations.
Our Deep Groove Ball Bearings have a number of different cage types to choose from. The most common type is a pressed steel cage. Our close coined cage pockets and tightly controlled clearances reduce friction and ensure even distribution of lubricant. These pressed steel cages also have the advantage of high temperature resistance. For high-speed applications, NSK offers cages made from advanced engineered plastics. These can help to extend the grease life and reduce noise and power loss in the bearing. In addition, plastic cages offer excellent resistance to shock or misalignment.
At NSK, we invest around 100 million USD a year in research and development of new bearing technologies, lubricants, materials, and surfaces. What’s more, new products are subjected to strenuous simulation tests on special test banks in order to ensure the highest quality and reliability, even under the harshest of conditions. NSK engineers have hands on experience of applications and their respective demands and can offer reliable solutions.
With our profitability program (AIP), onsite problem diagnosis, installation supervision and technical expertise, our commitment goes beyond just the delivery of the bearing. Through our network of distributors, we work closely with you to analyze your needs and possible problem areas to provide an efficient and reliable solution.
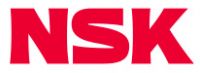