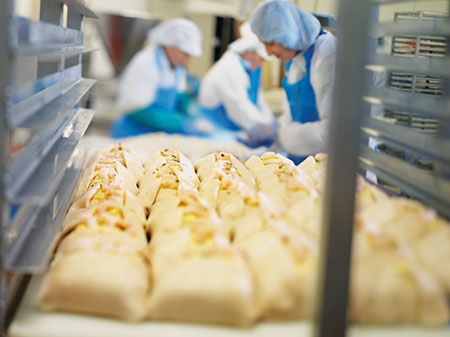
Producing and delivering safe food and beverage products is a complex process. Compliance and maintenance of all equipment, from inception to delivery, is critical to food safety. The Safe Quality Food Institute (SQFI), a division of The Food Industry Association, has introduced new safety standards in 2021.
SQFI aims to deliver consistent, globally recognized food safety and quality certification programs based on sound scientific principles, applied across all industry sectors and valued by all stakeholders. Understanding the new SQF Code and its impacts on machinery and maintenance within manufacturing plants is the first step to achieving this.
Companies using the SQF Code to achieve the highest level of food safety management practices are leaders in the industry and trusted partners of retailers and consumers.
SQFI Testing
Effective May 31, 2021, the 9th edition of the SQF Code requires food processors to test for factors including particulate, water, oil, microbiological and relevant gaseous testing in compressed air or other gases at least annually. Compressed air systems and systems used to store or dispense other gases that come into contact with food or food contact surfaces shall be maintained and regularly monitored for quality and applicable food safety hazards.
The latest SQF Code changes address 12 various areas of production, manufacturing, storage, packaging and distribution. The enhancements and improvements offer dedicated mandates to a more specific set of requirements and risk assessments. Obtaining the SQF certification adds value to a company and ensures a site’s food safety and quality.
Risks of Unkept Air Compressors
The presence of harmful microorganisms jeopardizes the health and safety of foods and beverages. This is true across aspects of food and beverage processing, including the use of compressed air.
Anything present in ambient air will be present in untreated compressed air. While much of the moisture, oil and aerosols come out of the solution under pressure, the air must be treated, typically through filtration and drying, to provide hygienic, high-quality compressed air.
Whether compressed air is part of a production process, such as food transfer and packaging, or part of a food or beverage product itself, companies must ensure that compressed air does not contribute to microorganisms’ growth.
Since microorganisms typically need a warm, humid environment to thrive, food and beverage companies should take steps to remove moisture from compressed air used in their processes. In the industry’s hygiene-critical applications, a compressed air pressure dew point (PDP) of -40 F/C is often specified. This is also referred to as ISO 8573-1 Class 2.
Air treatment components are available to remove a wide range of contaminants such as solid particles, liquid water, water vapor, oil vapor and odorants, and microorganisms such as bacteria and viruses. In most automation applications, including food and beverage processing, the focus is removing solid particles and water. For example, water separators remove condensation using either a coalescing principle or a centrifugal design.
A coalescing separator flows compressed air from the inside to the outside of a filter element. These filter cartridges must be replaced regularly. A centrifugal separator causes a rotary motion in the air, forcing particles to accelerate in a radial outward movement. Once they reach the outside, they drain into a bowl. No maintenance is required for this process.
Like the products that manufacturers make, it is essential that users start with the right ingredients. The same could be said of a compressed air system, and so selection of the right products for the right applications is essential—otherwise, it may be impossible to achieve the desired results.
Ongoing Maintenance
Compressed air systems and other systems used to store or dispense other gases that come into contact with food or food contact surfaces need to be maintained and regularly monitored for quality and applicable food safety hazards.
While the new SFQ Code requires annual testing of the air produced, many companies have leveraged smart monitoring systems to stay ahead of maintenance and keep compressors running at optimal performance. Monitoring equipment is adapted to the type of compressor. This involves an extensive range of equipment to suit all types of compressors. A large screw compressor can feature several cutouts/transducers for overloading, temperature, pressure, etc. On smaller machines, the control equipment switches off the compressor, and the machine is unable to restart when a cutout gives an alarm value. A warning lamp can, in some cases, indicate the alarm cause. Compressor operations can be followed on a control panel for more advanced compressors, for example, by directly reading the pressure, temperature and status. If a transducer value approaches an alarm limit, the monitoring equipment will issue a warning.
Measures can then be taken before the compressor is switched off. If the compressor is shut down by an alarm, compressor restart is blocked until the fault has been rectified or the compressor is reset manually. Troubleshooting is facilitated on compressors equipped with a memory where data on temperatures, pressure and operating status are logged. The capacity of the memory may cover the last 24 hours. This feature allows trends over the previous day to be analyzed and logical troubleshooting to quickly identify the reason for the downtime.
Monitoring & Control
With modern technology, there is no reason why users should not be able to connect to their compressor anytime and anywhere by using apps and connectivity platforms. Just like house alarms, users can outsource the monitoring of the compressed air system to third-party companies who will monitor it 24/7, 365 days a year. Monitoring provides a continuous overview of the system and provides access to individual machines to control details such as the intercooler pressure and oil temperature, and it is also usually possible to perform remote starting and stopping.
The monitoring system should also have a memory to produce a log of what has happened over the last 24 hours. The log is used to plot trend curves, which identify values that tend to deviate from the default easily. The curves can form the basis for continuing operations or planning a system stop. The system frequently presents compressor installation status reports at different levels, from a total overview to individual machines’ detailed status.
Air testing and compressor monitoring require a blend of using new technology, along with simple hands-on testing. A carefully designed and implemented compressed air monitoring program is needed to verify the effectiveness of a facility’s air filtration and air system maintenance to help users meet new quality testing standards. A good starting point is a professional audit of a user’s system for compressed air or other gases.