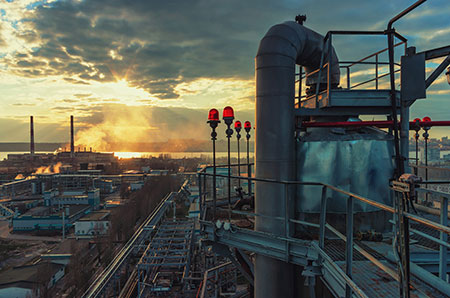
Industrial systems handle some of the harshest materials in the business. Whether chemical or industrial, products running through these systems range from caustic chemicals to dense, high-viscosity products, calling for specifications that cater to precise application needs.
Positive displacement pumps—the workhorses of fluid transfer—are a common component in these systems but come with many choices, including gear, lobe, air-operated diaphragm, progressive cavity pumps and more. With so many options available, however, systems can become piecemeal. It is prudent for operators to routinely review their systems, as a streamlined approach can offer many benefits.
An external circumferential piston (ECP) style pump can not only consolidate components in a system but offer additional benefits along the way. ECP pumps are similar to rotary pumps because their continuous piston motion creates an inlet suction and discharge output flow. This design makes for a constant and accurate displacement output with products ranging from thin to viscous, and it can handle soft particulates as well. The construction of this style of pump offers many advantages given the long internal rotor paths that offer little slip, highly efficient fluid transfer, repeatable output/revolution and low pulsation.
Given their range and flexibility, ECP pumps make for a good choice for many systems and should be on the list for consideration when choosing a positive displacement pump.
Considerations for Selecting a Pump
When evaluating the factors and features needed to select a pump, there is always a wide variety of considerations. Often, gear and lobe pumps are similar options to an ECP pump, but the outcomes of each are not the same, especially when looking at aspects like self-priming capability, shear sensitivity, noise level and more.
When comparing flow rate control, ECP pumps are known for stable and pulsation-free flow, giving them a more precise flow rate. Other styles of pumps, such as lobe and diaphragm pumps, often generate much more pulsation. This can reduce efficiency, increase wear and tear and can even lead to instrumentation or system failures. With a smoother fluid contacting rotor, ECP pumps are gentler on shear-sensitive fluids. They also have larger clearances and are better at handling entrapped air or vapor. The meshing gears found in other styles of pumps such as gear pumps can cause shear forces that adversely impact sensitive fluids. Due to their gear design, ECP pumps also tend to have lower internal noise, resulting in a quieter system overall.
ECP pumps can be a good fit for many industrial applications, given their flexibility and wide range of uses.
A Streamlined System Helps With Optimization & Efficiency
Operators may find themselves using multiple types and styles of pumps throughout a system. While this may be useful or necessary in some situations, in others, streamlining can help increase efficiency and decrease costs in the long run. Choosing a single ECP pump to replace multiple pumps can often lead to better performance and component consolidation. Fewer pumps means fewer parts and kits, reducing inventory complexity and simplifying staff training requirements.
An ECP pump that offers the latest in technological advancements is optimized for fluid transfer, thus resulting in energy savings and maximizing output. Its design minimizes slip (internal leakage), which leads to higher overall efficiency.
A single ECP pump utilizes less space, making it an option for those looking for a smaller footprint compared to other options, such as a progressive cavity pump, for example. While it may be an initial capital investment to upgrade the equipment, it can pay dividends overall, given the ECP pump’s energy efficiency, easy maintenance and additional output.
Reliability & Maintenance
A streamlined system with fewer pumps also means a simpler production process and less chance for downtime. By choosing an ECP from a reputable supplier and quality manufacturer, operators can enjoy reduced maintenance costs and extend the life span of the pumping equipment. ECP pumps can feature fewer parts than other positive displacement pumps reducing overall maintenance downtime and costs. They can also include robust mechanical seals and optional bearing isolators that can allow for extended run times. With streamlined maintenance, there is also only one point of contact for service, which is easy and cost-effective.
Real-World Benefits
Consider the recent experience of one consumer cleaning products manufacturer. The business found itself using various pump technologies—including air-operated diaphragm pumps, progressive cavity pumps and gear pumps—across multiple production lines. As the business prepared to introduce a new medium-viscosity cleaner, it needed a cost-effective solution that could standardize operations across multiple new fill lines.
The goal was clear: Find a single, reliable and versatile pump that could handle the demanding application while offering long-term cost savings. An ECP-style pump did just that. By replacing a range of pumps with an industrial ECP, the business achieved major improvements. The end user now enjoys consistent, reliable performance across all fill lines, ensuring smooth operations and high product quality.
Simplifying Pump Processes Can Future-Proof Systems
The industrial space is changing fast, from updated designs to energy efficiency improvements. In a field where abrasive, harsh environments or ingredients are key, it is important to utilize equipment that will set a system up for the best performance throughout its lifetime. ECP pumps may just be the answer when it comes time to consider where to streamline a system while taking advantage of the latest innovations.