Corn-based ethanol is a vital part of the total global energy requirement. During the past decade, the U.S. has become the largest producer of ethanol in the world, with a 56.8 percent share totaling more than 13.7 billion gallons (52 billion liters) produced in 2013. Production has doubled since 2007, and improvements in equipment, systems and processes have contributed to this increase. One Midwest-based research center is working to improve the ethanol process. Located outside of St. Louis, Missouri, this research center focuses on validation and commercial testing of products, technologies and new concepts. The center is fully equipped to meet all research or technology validation needs, providing laboratory, fermentation and pilot plant production process services in an integrated setting.
Pilot Plant
Costs associated with the design and development of products for the renewable fuel market represent a tremendous investment. Knowing precisely how these products will perform in a real plant before that investment is made can make a significant difference in a company's success or failure. The 24,000-square-foot pilot plant, equivalent to a 1/250th scale ethanol production facility, operates at a 100 to 400 bushel per day capacity and offers continuous or batch-run operation. The pilot plant ethanol process begins with the whole corn kernel ground into meal. The meal is then slurried with water to form a mash. Enzymes are added to convert the starch to dextrose, a simple sugar. Ammonia is added for pH control and as a nutrient to the yeast. The mash is processed in a high-temperature cooker to reduce bacteria levels before fermentation. It is then cooled and transferred to fermenters where yeast is added, and the conversion of sugar to ethanol and carbon dioxide begins. The fermentation process generally takes about 40 to 50 hours. During this part of the process, the mash is agitated and kept cool to facilitate the activity of the yeast. After fermentation, the resulting "beer" is transferred to distillation columns where the ethanol is separated from the remaining stillage. The ethanol is concentrated to 190 proof using conventional distillation and then dehydrated to approximately 200 proof. The ethanol is blended with about 5 percent denaturant (such as natural gasoline) to render it undrinkable and exempt from beverage alcohol tax. It is then ready for shipment to gasoline terminals or retailers. The pilot plant is staffed with an experienced team of engineers and operators. The ethanol plant operating coordinator is a veteran of the industry. It is his job to keep the pilot plant operating at optimum efficiency. Finding the right equipment is critical to his mission.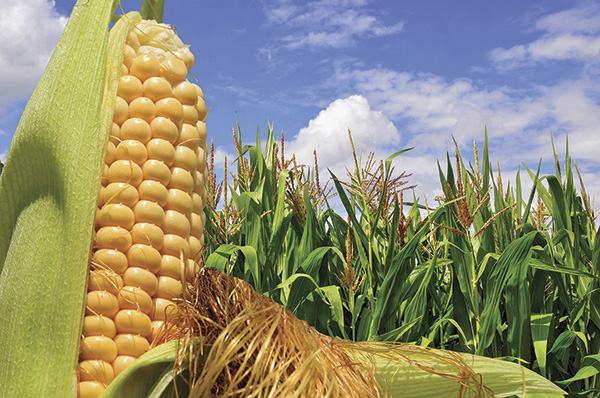
Room for Improvement
One of the maintenance requirements of the fermentation process is flushing the tank periodically with a caustic hot water (160 to 180 degrees F) cleaning solution. The blend of corn fines and corrosive water is then flushed into a sump where the wastewater is held before treatment. The cast-iron pumps responsible for clearing the sump, however, experienced excessive wear and short service life. The operating coordinator consulted with a Midwest industrial distributor with experience in ethanol production. The distributor recommended high-temperature, stainless-steel submersible pumps for the sump application. The selected pumps are designed to handle high-temperature corrosives and provide solids handling for the bottom-settling corn fines. Non-clog, single vane impellers deliver the high volume and lift performance that is required for the sump service. All of the wear and "wetted" parts, such as the impellers and wear-plates, are made of cast 316 stainless material. The elastomers—such as O-rings, lip seals and gaskets—are made of chemically resistant, high heat resistant flouroelastomers. An additional life cycle enhancing feature provides three-seal motor protection. The submersible motor is protected by double mechanical seals. The lower seal is made of silicon carbide/silicon carbide, and the upper seal is made of carbon/ceramic. An additional lip seal is installed above the impeller to prevent abrasives such as corn fines from entering into the seal chamber. Additional winding protection, National Electrical Manufacturers Association Class R motor insulation and a thermal cut-out switch that will allow the stator to reach a winding temperature of up to 300 F are standard.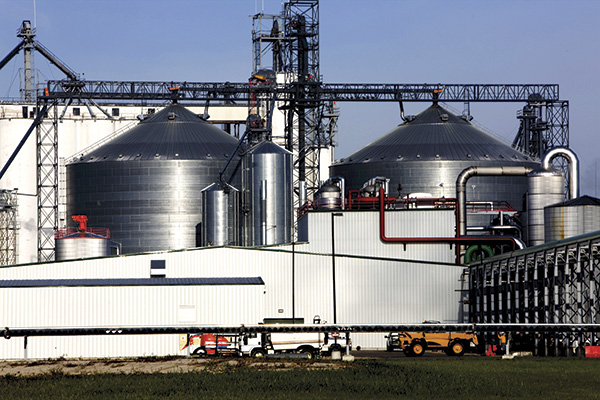