With the high price of petroleum, U.S. producers must maximize every dollar from a barrel of crude oil. Every 42-gallon barrel produces 45 gallons of petroleum products. Most of the petroleum is refined into gasoline (47 percent) followed by heating oil/diesel fuel (20 percent) and jet fuel (8 percent). After that, the percentages decrease significantly as refiners produce liquid and gas distillates for industry and construction. One of these is petroleum coke. During the petroleum refining process, distillates are separated from residual oil after it goes through a vacuum distillation unit. These lighter grade petroleum products—such as hydrocarbon gases, naphtha and light and heavy gas oils—are separated from the oil in a coker unit. After distilling the desired petroleum byproducts, the remaining carbonaceous solid residue is petroleum coke, which has to be cut out of the coker unit with high-pressure water. Petroleum coke (often abbreviated as petcoke), is more than 90 percent carbon and releases 5 to 10 percent more carbon dioxide than coal when burned. Petcoke, depending upon the grade—either high or low in sulfur and metals—is used as inexpensive fuel in offshore power generation, coal fired boilers or in the steel and aluminum industries. U.S. refineries produced more than 61.5 million tons of petcoke in 2011—enough to fuel 50 average coal plants each year.
Case Study
Oil refineries usually store petcoke onsite awaiting pending sales or ship it to other companies that store and sell it. PABTEX, L.P., an affiliate of Kansas City Southern Industries, located in Port Arthur, Texas, is a major bulk-commodity handling facility and vessel-loading terminal. It specializes in exporting petroleum coke and receives petroleum coke by train from one of several refineries in the area. On its 29 acres of outside storage, PABTEX can store 500,000 tons of petcoke before transferring it to shipping terminals for transport to global end users.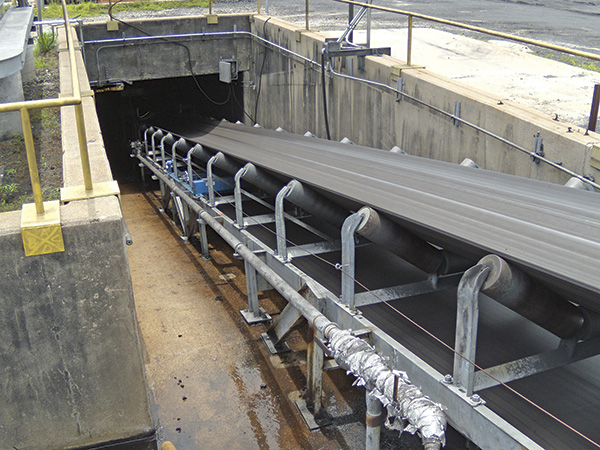
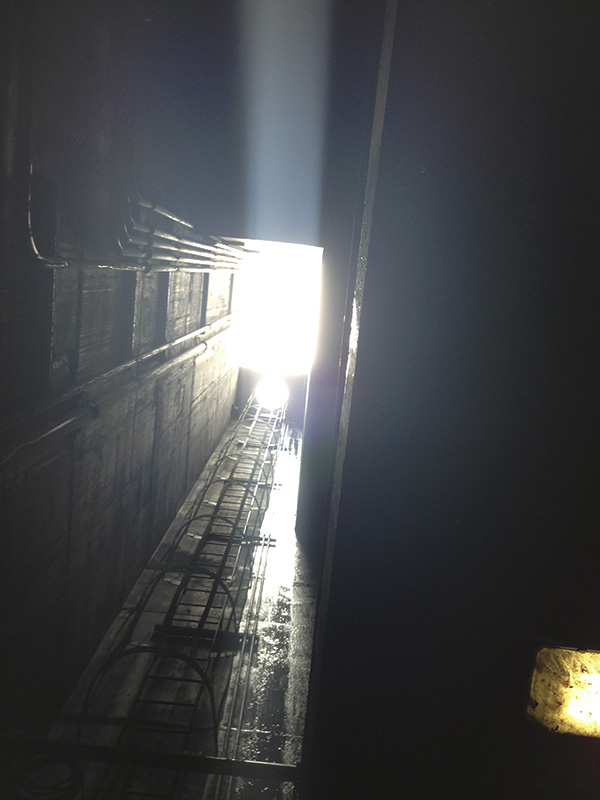
- Optimum wear resistance—all wetted parts are constructed of abrasive-resistant, 28-percent chrome iron (600 Brinell, 57 Rockwell C) for maximum wear life. In addition, a replaceable hardened wear plate is located on the suction side, where erosion would cause a loss of pump performance.
- Maximum solids-handling capability—an integral agitator fluidizes settled solids into a slurry, making them easier to pump with less chance of clogging. The semi-open impeller handles abrasive solid concentrations as high as 70 percent by weight.
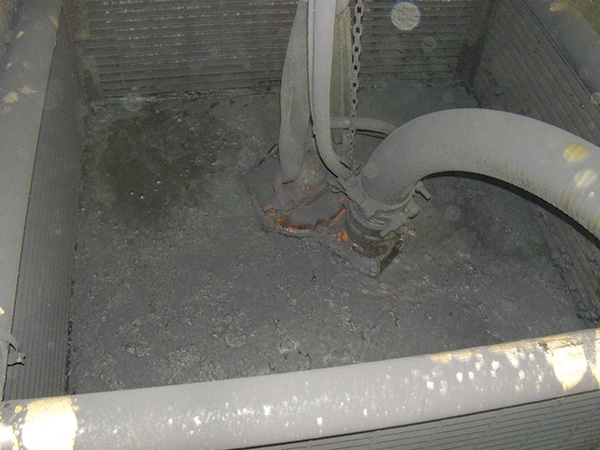
- Class H motor insulation and built-in amperage (full load amp) and temperature overload protection
- Double silicon carbide mechanical seals in a separate oil filled seal chamber
- Heavy-duty lip seal—additional protection for the mechanical seals
- Stainless steel shaft and shaft sleeve, which provides maximum wear and corrosion protection
- Pump volutes cast from hardened ductile iron (300 Brinnell hardness), which is twice as abrasive resistant as standard ductile iron with extra thick walls where pumped slurry enters the discharge