Q. What are some typical indicators of an inefficient pumping system? A. Many pumping system components are not dynamic. These components allow fluid or heat transfer, but aside from thermal expansion or structural vibration, they do not move and do not have dynamic surfaces that wear out. Leakage, fouling, valve failures and cracks in pipe supports are the most common problems. For many industrial facilities, the energy consumed to move fluids makes up a large part of the facility’s overall electricity usage. Operators are often unaware of how to use the energy required to pump fluids. Ineffective energy monitoring may affect a large part of the plant, even the entire facility. A few symptoms in pumping systems often indicate if improper sizing, selection, operation or other issues affect the system’s performance. These include:
- Valves are throttled to regulate flow rate, level and pressure
- Bypass (recirculation) flow regulation
- Batch-type processes, but one or more pumps operate continuously
- Frequent on/off cycling of a pump in a continuous process
- Cavitation noise either at the pump or elsewhere in the system
- Equipment procurement policies based solely on lowest bid price
- A multiple, parallel pump system in which the same number of pumps are always in operation
- A pumping system that has undergone a change in function with no change in pump equipment or operation
- A pumping system with no flow, pressure or power indication
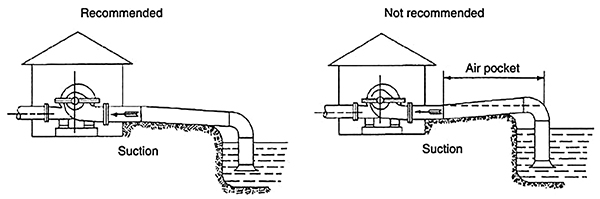