Level sensor and pump liner flaws increase avoidable costs for mining facilities.
12/12/2014
In complex systems, many factors can affect overall performance. For example, a mining facility was experiencing problems with small system components that caused its pumps to run faster without increasing flow rate. These issues meant increasing costs without greater production. To resolve the issue, a predictive analytic software solution was implemented to help this facility diagnose the problem and regain system efficiency.
Level Sensor
The remote monitoring and diagnostic (RM&D) software solution detected that a pump at a South African mining facility was not operating at the speed that was expected based on previous historical data. The software identified that the percentage of time a proportional-integral-derivative (PID) control loop for a pump had exceeded its operating limits was increasing above historic values. While further analyzing the pump’s operational history, personnel found periods of time when the pump was operating at 100 percent speed when it was expected, given the loading conditions of the pump, to operate at 80 percent speed. During the time that the pump was run at full capacity, a suction level sensor was returning flat line values. The RM&D team investigated this issue and discussed it with the customer during the weekly maintenance call.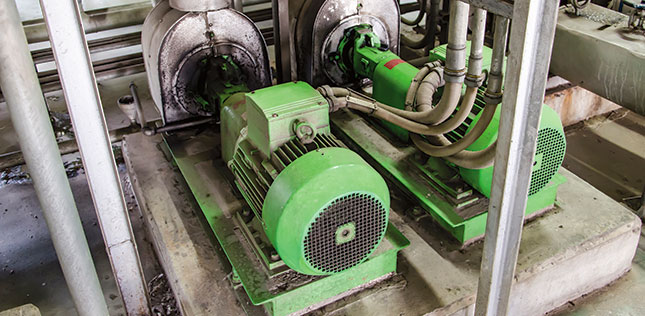