Life-cycle cost calculations for wastewater installations can produce huge savings over time for wastewater companies. The life-cycle costs summarize the total cost of a wastewater installation, and the pump system plays a major role. It is the key element to ensuring the installation’s long-term cost-effectiveness. Total lifetime costs normally include planning, design, purchasing, investment, installation, commissioning, energy, maintenance and operation, and downtime costs. A system can also incur environmental and disposal costs at the end of its lifetime. The pump system has the highest impact on the lifetime cost of the wastewater installation. However, only three of the costs listed above play a significant role in the pump system’s contribution to life-cycle costs: investment, energy and maintenance.
Investment
The initial procurement cost is often seen as the best way to ensure low cost. Meeting investment budgets means keeping in mind that the cost of operation, maintenance and disposal could be five to 20 times higher than the initial investment. This is why municipalities and contractors increasingly consider the requirements for performance, reliability and energy consumption when purchasing a pump system.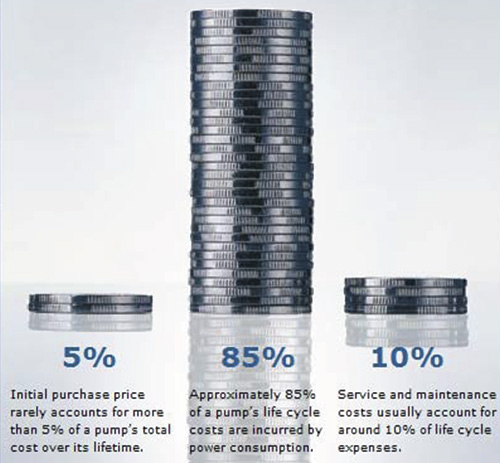
Energy
Decision makers might think that the energy cost of the pump is easy to calculate. But many things must be considered when determining the energy cost of a pump—such as wear, variable load, installation and clogging. If the wrong wastewater pump is chosen, the media content leads to wear, costly breakdown and 3 to 5 percent lower efficiency for every year the pump is not maintained. Most pump brands make it possible to restore efficiency loss. Some have a replaceable wear ring, while others have built-in trimming that allows adjustment of the impeller clearance using outside bolts. Because wear also affects non-replaceable parts of the pump, full restoration of efficiency is impossible. The design of the pump impeller is a key issue, since a simple design with large free passage and no inserts or moving parts will wear less than a design without these features, thus ensuring a high efficiency over the pump lifetime. The pump’s duty point is seldom constant and varies over the course of a day, a year and a pump’s lifetime. Users should look for a pump with a flat efficiency curve. This ensures high efficiency over a wide duty range and determines whether the pump is using a variable speed drive. If the pump is running with variable speed, a pump with a duty point to the right of the curve should be selected. When adjusting the speed downward, the pump’s duty point moves to a part of the curve with higher efficiency.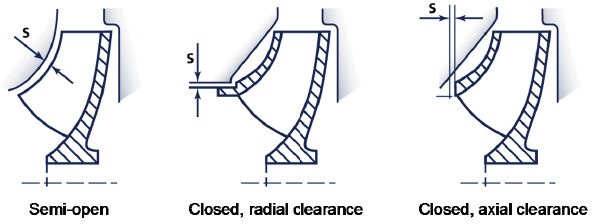
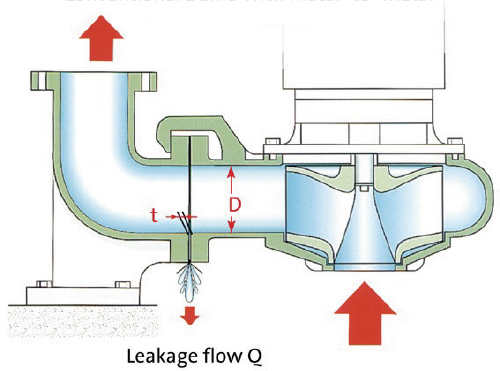
Maintenance
Maintenance costs are often difficult to estimate. Planned maintenance costs will vary depending on many different factors, such as:- Pump value
- Pump maintenance costs
- Operational experience
- Pump failure consequences
- Pump failure probability
- System design
- Maintenance to be performed on the pump
- Time required for maintenance activity
- Number of personnel involved
- Spare parts cost for maintenance activity