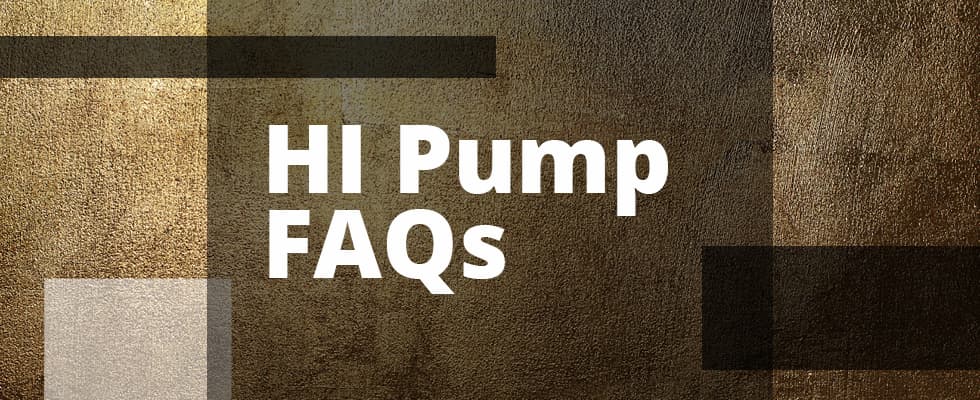
How should temperature measurements be used for monitoring the condition of rotary pumps?
Temperature monitoring is an important practice because it can extend the life of rotary pumps and their components. This monitoring can be used to prevent failure caused by bearings, seal faces, net positive inlet pressure available variation, cooling-loop blockage and decoupling of magnetic couplings. Since certain components are subject to different temperatures and allowable temperature values, different temperature monitoring methods are used for different components.
Additionally, certain locations within the pump may be subject to rapid temperature changes, which must be taken note of when taking measurements.
For instance, motor insulation deteriorates faster at higher temperatures. Temperature is dependent on load, frequency of starts and cooling effectiveness. Winding temperature is more often measured by thermocouples located at the center of the end turns.
Temperatures of contacting surfaces of sleeve bearings, thrust bearings, pumping elements and mechanical seal faces can change rapidly when the liquid film is not supporting the load correctly or not providing proper lubrication to the parts. For these components, temperature sensors located near the contact surfaces can frequently detect distress before failure.
Certain liquids are temperature-sensitive, so care must be taken to ensure an accurate temperature measurement. For liquids that must be maintained at high temperature to control viscosity, locate the sensor in the least heated area and allow time for temperature stabilization.
Since there is a direct link between viscosity of the pumped liquid and rotary pump performance, if the temperature and viscosity characteristics of the pumped liquid are known, then temperature monitoring can help maintain pump performance while monitoring potentially harmful conditions such as low viscosity, low volumetric efficiency and cavitation.