The handling of liquid resources is not a clear-cut process. In fact, it is as fluid as the liquid itself. Every wastewater project has specific criteria that demand a combination of design innovation and product versatility. The key to successfully handling wastewater is selecting the right pump to solve the liquid handling needs.
Maintaining Flow
The flow of wastewater can be compromised, and an interim pumping solution may be required for many reasons:
- When a sewer system needs scheduled maintenance
- If a wastewater treatment plant must be expanded
- During critical emergency response situations—such as floods or overflows
- In these situations and many others, a temporary or rental liquid handling provider will be needed to supply critical equipment—from a centrifugal trash pump to a floating pump system.
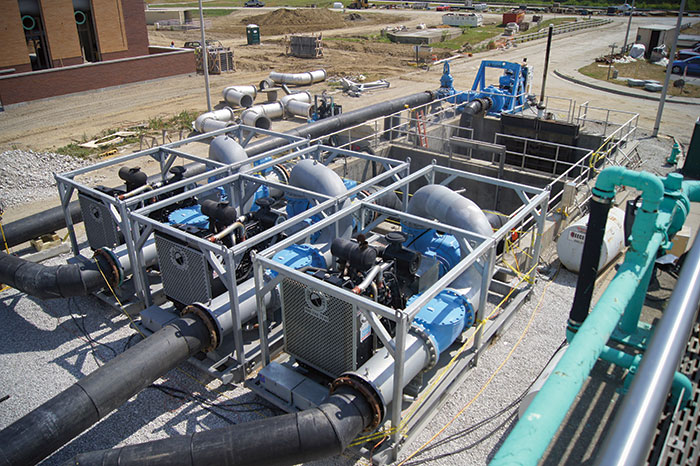
Case Studies
In this section, three case studies provide examples of how wastewater handling challenges were solved through the careful evaluation and the selection of the right pumping solution.
Floating Pump System Saves Louisiana Parish Homes from Floodwaters
In a residential area outside Baton Rouge, La., heavy winter rains flooded a swollen levy and lock drainage system, resulting in more than 10 feet of floodwater that threatened homes and residents. For almost two weeks, residents scrambled for sandbags to keep the encroaching water from their homes. However, with the ongoing danger from additional winter storms, the water was not draining from the area fast enough.
Local parish officials reached out to a liquid handling solution provider to help design a system that would accelerate the draining process while protecting homes and infrastructure from the floodwaters. Within hours, this provider designed a solution to meet the critical needs of the community.
The system used two floating pumps stations. Each station consisted of a 42-inch, two-stage high-efficiency, self-contained axial flow pump that was capable of producing the high water flows that are ideal for flood control and large dewatering projects. It delivered maximum flows of up to 68,500 gallons per minute and produces a maximum head of 27 feet.
The two floating dewatering systems removed more than 96,000 gallons per minute of floodwater from the aging system of levies and locks. They operated 24 hours per day for three consecutive weeks and reduced the water levels from 14 feet above flood stage to normal.
With no more winter storms on the horizon, officials were able to focus on a long-term solution rather than the water at their doorsteps, and residents were able to pack away the sandbags and carry on with their lives.
As a result of current and past projects with the parish, the solution provider has become the area’s go-to resource for temporary pump, dewatering and bypass needs. A parish official stated, “… the water will still take about two weeks to completely return to normal levels, but that is better than the month it would have taken if we had not called on [this company] to set up the pumping operation.”
A Bypass for a Wastewater Treatment Plant
To tie new construction into the existing wastewater infrastructure, an expanding wastewater treatment plant required a screened sewage bypass of up to 75 million gallons per day. The project was time sensitive and offered only a small footprint for bypass pumps to operate effectively.
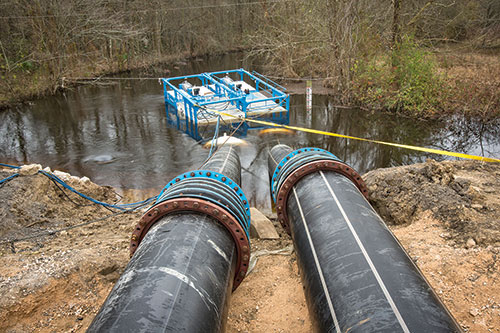
The plant’s contractors selected a two-pump bypass solution consisting of a primary system with two large, self-priming centrifugal trash pumps and one smaller, self-priming trash pump to manage the 75 million gallons per day. A backup system using an additional large trash pump was also provided.
The large, centrifugal pump is one of the largest portable, diesel-powered, self-priming centrifugal pumps available for rent—a 30-inch suction x 24-inch pump that delivers up to 28,000 gallons per minute of pumping and up to 96 feet of head. The smaller pump is a self-priming centrifugal pump with an 18-inch suction and 16-inch discharge that delivers a maximum of 16,000 gallons per minute of pumping and up to 200 feet of head. These pumps are usually mounted on a skid and feature a standard vacuum priming system that allows them to run continuously, unattended and even run dry.
Using three pumps with one backup for the bypass was cleaner and easier to maintain within the tight space constraints at the plant, and it used less diesel fuel throughout the continuous month-long bypass. Because of the liquid handling solution providers’ practice of stamping the high-density polyethylene (HDPE) to secure the welds and hydro-testing the system, the successful bypass was spill-free, cutting the plant contractor’s costs.
Multiphase Engineered Bypasses Aid in Crucial Sewer System Upgrades
Halfway through a multibillion dollar wastewater treatment upgrade, a city in the southeastern U.S. began the crucial separation of its antiquated combined sewer overflow (CSO) system. With nearly 2 million customers, the city did not want residents to be adversely impacted by the upgrade to a separated wastewater and stormwater system.
Contractors for the city engaged a liquid handling solution provider at the outset to be directly involved in the engineering, planning and deployment of the temporary bypasses needed during the combined installation of more than five miles of sewer line.
Many pumps and more than two miles of HDPE pipe were engineered into multiphase sewer bypasses, allowing for sewer repair and upgrades. During the project, more than 30 bypasses were performed to manage up to 20 million gallons of sanitary sewer flow per day using several different rental pumps.
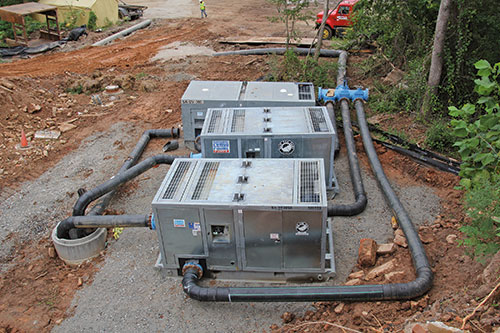
To minimize the impact on residents in nearby neighborhoods, noise and environmental precautions were also taken. Sound attenuating pumps were used, and every bypass was designed with a backup pump and a special telemetry alarm agent to automatically alert individuals via cell phone if the system required immediate attention, such as when the volume rose too high. Before the sewage began to run through the bypass, all the 12-inch and 18-inch HDPE pipe was hydro-tested with clean water to ensure that no leaks were present.
The solution provider’s extensive bypass experience, backed by engineered design, ensured that the new sewer system could be installed smoothly and without any complications or spills. This allowed the pipeline contractors to focus on their trenchless and rehab work, leaving the solution provider to manage the liquid handling.