A large, investor-owned utility in the southern US wanted to reduce corrosion problems and boiler downtime.
11/15/2015
Electricity-generating power plants rely on high-pressure steam to drive turbines and create electricity. The water used to create the steam can contain minerals, so it is imperative to extract these to prevent them from being deposited on the turbine blades and corroding the steam circuit. To achieve these goals, power plants typically treat the condensate with ion exchange resins.
.jpg)
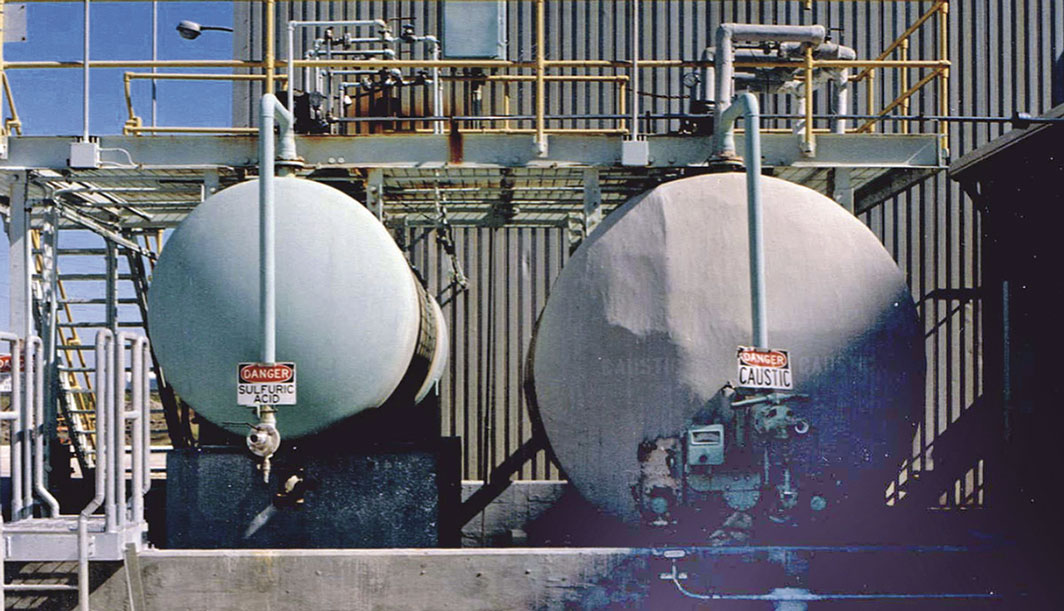
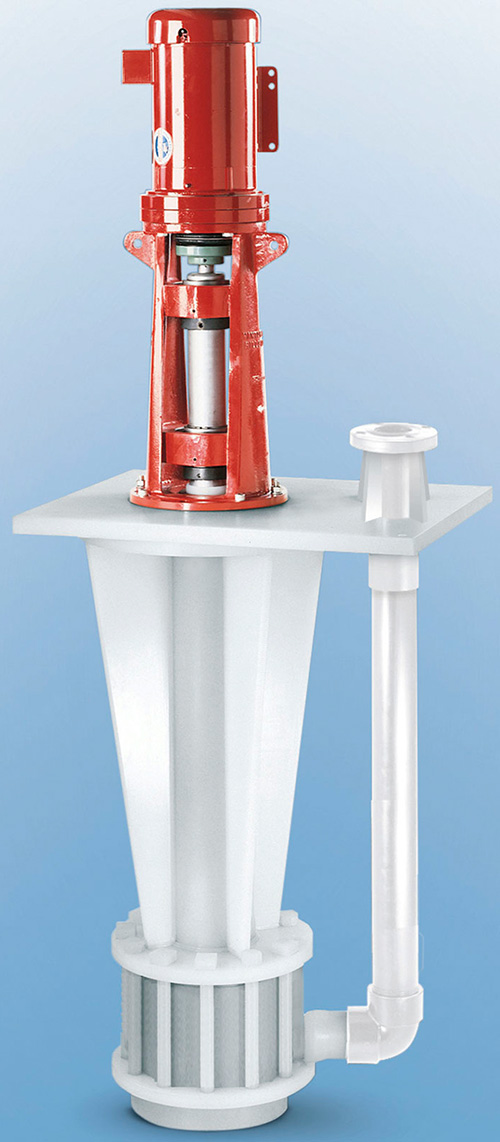