07/24/2014
In my June column on pump and motor testing, I said that three-phase voltage variation and unbalance can have a significant effect on motor insulation life. Voltage variation is defined as the difference between the motor nameplate voltage and the incoming source voltage. This assumes that all three phases are the same voltage. Variation can be either negative or positive. Unlike variation, voltage unbalance refers to the differing voltages that can occur in each of the three phases. This month’s column reviews voltage variation. Next month’s column will cover voltage unbalance.
Low-Voltage Motor Requirements
Prior to the introduction of the T-frame motor in 1964, low-voltage motors were designed to operate at 220 and 440 volts. Today, that standard is 230 and 460 volts and is referred to as the utilization voltage (American National Standards Institute C84.1). These voltages were selected because they reside in the middle of the service range that a utility is required to supply. They also allow for the voltage drop that can occur because of the distance between the motor and the service entrance. The National Electrical Manufacturers Association (NEMA) standards recommend that motors should be designed to operate satisfactorily at a voltage variation of plus or minus 10 percent. For 230 volts, that range is 207 to 253 volts; for 460 volts, it is 414 to 506 volts. The word “satisfactorily” is important because parts of this range can be less than optimal. Figure 1 shows the effect of voltage variation on several motor performance characteristics. It can be used to show the general effects, but variations will occur based on a particular motor design. The intersection of the zero points on the x- and y-axes represents the motor nameplate voltage.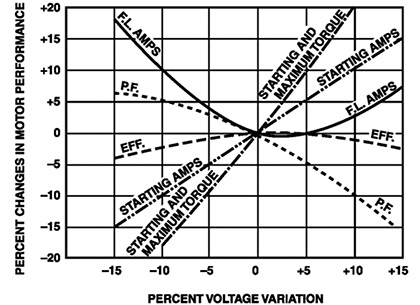