The manufacturing industry increasingly uses predictive maintenance regimes to keep tabs on machine health to detect system problems as early as possible. Vibration monitoring is a vital part of this. Its affordability, accuracy and ease of use means it can be widely used to monitor industrial machinery. Maintenance staff are generally familiar with vibration monitoring. They are comfortable taking readings and know what to do if conditions stray outside operating parameters. However, the conditions that cause vibration to arise in the first place are less understood. In a machine diagnosis context, vibration is the motion of a mechanical part when it strays outside its natural position. When a bearing begins to wear, for instance, this affects its motion along the raceway. At some point, it will become loud enough to hear. But the problem can be discovered much earlier with vibration monitoring.
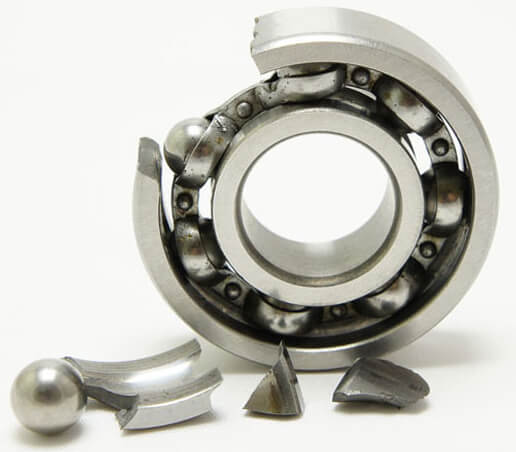
Vibration Parameters
The three main vibration parameters are frequency, amplitude and phase. Measuring the frequency of the vibration identifies the specific vibrating component because the monitor will detect the component’s characteristic frequency. Adding a technique like acceleration enveloping separates the frequency of one component, such as a bearing, from another, such as its casing.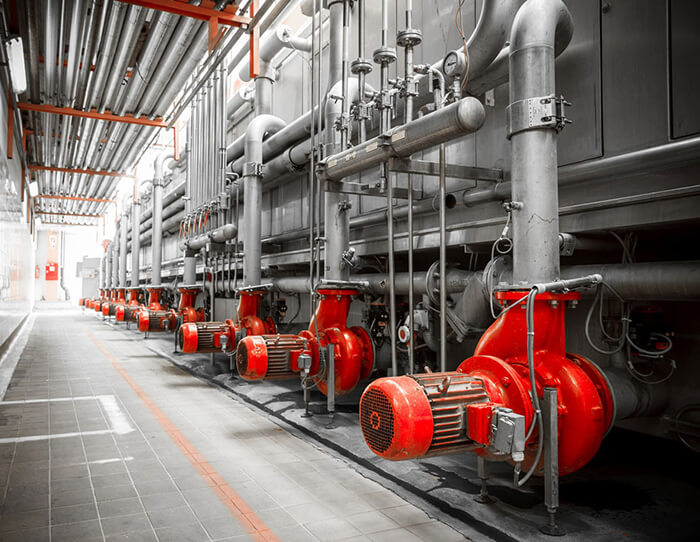
Bearing Damage
Bearing problems are often the root cause of excess machine vibration. The main reasons for bearing failure are inadequate lubrication, poor installation or handling, age and excessive loads. While inadequate lubrication usually refers to a lack of lubrication, it can also mean over-lubrication, which is another common cause of failure. Another lubricant-related problem is contamination, which is caused by factors such as leaking seals. If a bearing is not installed correctly in its housing, it will not perform optimally, and it will be prone to failure. Potential reasons for this include operator inexperience, rushing the installation or simply using the wrong tools. The age of the bearing is an obvious potential weak point, but with preventative maintenance, bearing issues can quickly be identified and replaced if the component begins to fail. Finally, excessive bearing load is usually caused by imperfections elsewhere, such as misaligned shafts, imbalance or looseness. This puts excessive force on parts of the bearing, creating tiny cracks on the bearing and raceway that can develop into more serious flaws caused by wear.Types of Vibration
While excessive wear is considered the main cause of failure in machinery and the main enemy of maintenance teams, a few other conditions need to be closely monitored, especially imbalance, misalignment and looseness, which, if left unchecked, can damage components and machinery. Imbalance occurs when the center of mass differs from the center of rotation. This creates a centrifugal force, leading to high vibration amplitudes at frequencies equal to 1 x rotational speed in spectral data with a sinusoidal waveform in the time domain. On rigidly mounted machines, amplitudes are usually highest in the horizontal direction. Misalignment happens when the shaft centerlines of two directly mating components meet at an angle, or are offset from one another. Misaligned couplings and bearings typically cause high radial or axial vibration. A combination of angular and offset misalignment is the most common cause of problems.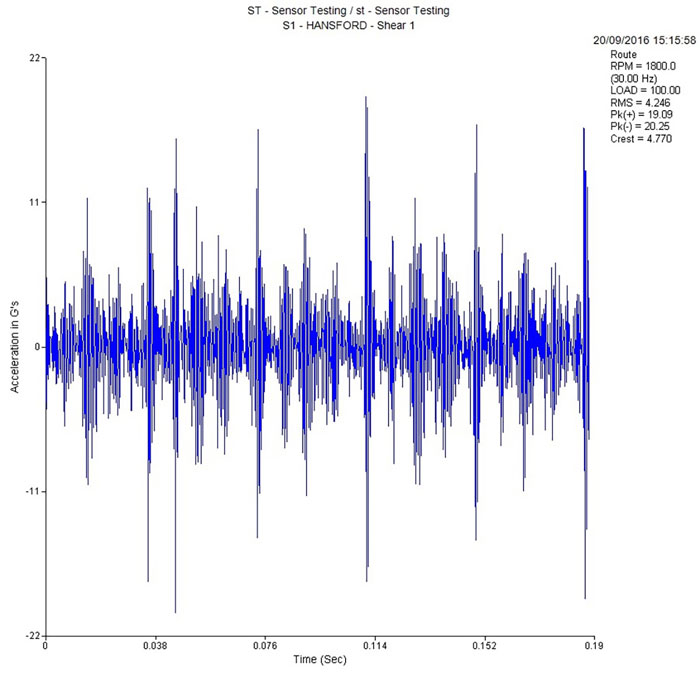