For a large pump package, a medium-voltage motor (above 1,000 volts) incurs significant cost. For this reason, many users ask a common question: How can motor cost be reduced? When looking at the specifications, the question becomes: What are the cost drivers for a larger motor? Are the options and accessories driving the cost, or is it the testing—or maybe some part of the specification that has been passed down—that is harming the reliability in the new application? Many motor specifications are passed down from previous projects or are a general specification created to cover every contingency. The “inheritance” of a specification leads to little understanding of cost or value for the requirements laid out in the document. How does an engineer who is specifying get an idea of a specification’s cost drivers or know when a specific requirement is needed in the application? The cost of a motor, much like that of a pump, is based on frame size. When an end user communicates the power required to drive the pump to the motor vendor, the base frame size is determined. The motor supplier tries to provide a motor with the smallest frame for that power rating because each increase in frame size adds 25 to 35 percent to the cost of medium-voltage motors. Some parts of a specification may increase the frame size beyond the initial power requirements.
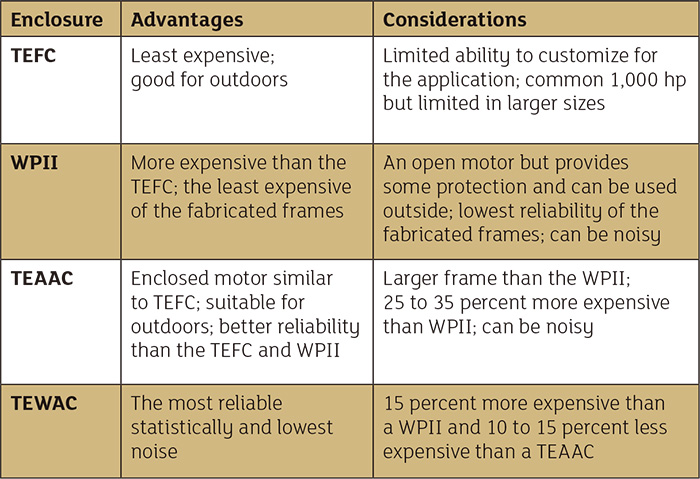
Motor Enclosures
The first driver of the frame size other than power is the enclosure type. Users must evaluate and understand the pros and cons of each to determine the best solutions for their applications. The least expensive enclosure is the totally enclosed fan-cooled (TEFC) type, which is also called a cast-frame or finned-frame motor. TEFC enclosures are the oversized “big brother” of typical low-voltage (below 1,000 volts) industrial motors. The motor is enclosed, so it is suitable for outdoor applications. Because these motor types have little air inside to circulate for cooling, a fan at one end cools the drive end bearing. The lack of cooling limits the horsepower (hp) in this type of enclosure. Because the frame is cast, this enclosure type can limit options and accessories, and is generally more of a “stock” product. Fabricated frames, on the other hand, are used for motors in the megawatt range and can be fully adapted to the specification.TEFC Cast Frames vs. Fabricated Frames
Fabricated frames are more expensive than cast versions and come in several basic types. Weather Protected II (IC01) Weather Protected II (WPII) is an open enclosure seen primarily in North America and is suitable for outdoor operation. It is open, but the cooling air must make multiple turns before passing through the motor to keep airborne debris out of the motor’s internal parts. This effective cooling method means the frame can be a minimum size. This type can be less reliable than other fabricated frames because it is open, and noise control can be difficult. A fabricated frame is more expensive by 25 to 50 percent. TEAAC When the motor is outdoors and too big for a TEFC and when a WPII type is not acceptable for environmental reasons, a totally enclosed air-to-air cooled (TEAAC) enclosure is usually the next choice. The motor has a large air-to-air cooler on top so hot air created in the motor is circulated up and over the heat exchanger. Ambient air is forced by a shaft-driven fan through the heat exchanger. The motors are statistically more reliable than a WPII. Air-to-air heat exchangers are not efficient using ambient air of 40 C, so the frame will be larger compared with an open or a WPII motor. TEAAC types are also noisy because the air is forced through the small tubes of the heat exchanger. This motor is typically one frame larger than a WPII, which increases cost by 25 to 35 percent. TEWAC In many applications, the most reliable choice statistically is a totally enclosed water air-cooled (TEWAC) type, but it requires a cooling water system. The efficiency of the air-to-water exchanger reduces the frame to the size of the WPII. The cost is generally halfway between the WPII and TEAAC.Service Factor
When discussing service factor, the safety margins for the system must be considered. Service factor for a motor is defined by National Electrical Manufacturers Association (NEMA) MG1 for medium-voltage motors differently than for low-voltage motors. Medium-voltage motors must meet the service factor rating continuously. In other words, a 1,000-hp motor at 1.15 is actually designed as a 1,150-hp motor, which will probably cause the frame size to increase. The pump specification may require 10 percent additional operating margin or safety factor. If the motor is also increased 15 percent above the pump margin, the service factor becomes 26 percent, creating an oversized motor. There needs to be some margins above the calculated load, but only one safety margin should be required either at the pump or on the motor.Starting Requirements
Starting requirements are a common specification that is inherited with little understanding of what it is or the cost. A standard large motor will typically include a 2C/1H on the nameplate, which means two cold starts or one hot start and indicates that the motor can start twice when the motor temperature is below ambient and once when it is above ambient without damage. The 600 percent inrush or starting current decreases until the motor speed approaches its nominal operating speed. The extra inrush current that is not converted to torque becomes heat, so the motor’s interior heats rapidly because the cooling fans do not move much air until the speed is well above 50 percent. If the pump is starting in a lightly loaded condition, this specification has no impact on motor sizing or pricing. If the specification calls out 3C/2H (three cold or two hot starts) and the pump cannot be fully unloaded, the only way to accommodate this requirement is to increase frame size. If multiple restarts are not required, then this requirement should be reviewed.Operating Voltage
The higher the voltage, the higher the cost of the motor. This phenomenon typically occurs at 10,000 volts and higher. This is the point where most motor insulation systems add corona protection and the insulation for the coils has the maximum layers that the vacuum pressure impregnation (VPI) resin can fully penetrate. As the insulation gets thicker, there is less room for the copper “magnetics,” so the frame for higher-voltage motors will be larger for the same power rating. Also note that switchgear costs go up at a higher voltage, which may be offset by lower cabling costs due to reduced amperage. For pump stations with a high voltage of 10,000 volts or more available from the utility, adding a stepdown transformer to operate at 6,000 volts or less can reduce costs substantially. The reduced cost of the motor and switchgear can be significant if the motor sizes are 5,000-hp or less.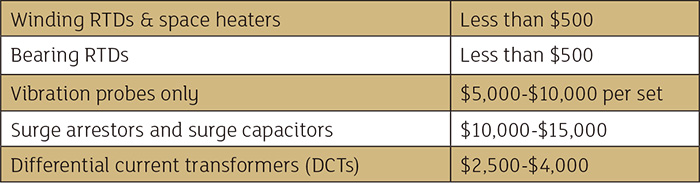